Digitization in Motor Vehicle Manufacturing
January 2, 2018 | Fraunhofer-GesellschaftEstimated reading time: 2 minutes
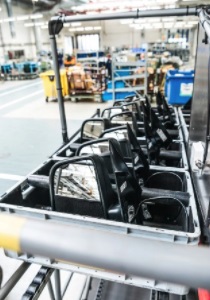
Pressure to optimize is intense on the floors of motor vehicle manufacturers’ factories: Variance is steadily increasing. Costs have to be contained. Fraunhofer researchers are now using RFID technology to introduce more transparency in motor vehicle manufacturers’ supply chains and manufacturing operations. This reduces time and labor, thus boosting cost effectiveness.
A variety of options in motor vehicle manufacturing: Outwardly, many parts are virtually indistinguishable to workers.
Anyone who has ever ordered a new car knows that the list of options is long. The variety of options is constantly growing. Such customization entails major challenges for carmakers. Outwardly, many parts are virtually indistinguishable to workers – a seatbelt for German cars looks remarkably like one for non-EU cars. That is why safety-related parts are given barcodes, which require manual scanning. In the course of digitization, RFID is freeing employees from this routine task, while automatic inspection simultaneously gives them certainty that they have installed the correct parts.
Boosting Process Reliability and Transparency
Researchers from the Fraunhofer Institute for Factory Operation and Automation IFF in Magdeburg are readying manufacturing and supply chain operations for digitization and Industrie 4.0 respectively. “Radio frequency identification or RFID tags on parts can boost process reliability and efficiency significantly,” says Marc Kujath, research scientist at the Fraunhofer IFF. “We have demonstrated this in feasibility studies and wireless tests conducted jointly with Mercedes-Benz Vans at their factory in Ludwigsfelde near Berlin.” Such RFID systems consist of RFID tags on parts and a scanner that reads out information optically. In a first step, the researchers analyzed which of the numerous vehicle parts are best suited for this and identified as many as forty parts. For the start, the experts focused on mirrors and seats for further developments.
Automatic Inspection during Assembly
The RFID tags are affixed to every single safety-critical part, individual mirrors for instance. Much like barcode, a serial number is stored on the tags, the major difference being that, whereas barcode merely stores information identifying the type of mirror the number on an RFID tag delivers abundant information such as the vehicle in which a mirror is to be installed. Whereas barcodes have to be read manually with a handheld scanner one by one, RFID tags can all be read automatically and optically at the same time by one scanner – even when the parts have been installed. This means that information can be retrieved from RFID tags in seconds at any given time. This is a crucial advantage for manufacturing. For instance, the installation of all the requisite parts can be verified while a front or rear axle is being mounted. Previously, this was not checked until final inspection – by employees conducting visual inspections and using paper lists. “RFID tags enable us to boost transparency,” explains Kujath
Testimonial
"Advertising in PCB007 Magazine has been a great way to showcase our bare board testers to the right audience. The I-Connect007 team makes the process smooth and professional. We’re proud to be featured in such a trusted publication."
Klaus Koziol - atgSuggested Items
The Power Shift in U.S. Manufacturing Ownership
08/20/2025 | Nolan Johnson, I-Connect007The U.S. manufacturing landscape is driven by reshoring initiatives, supply chain realignments, and a surge of foreign interest. What does that mean for U.S.-based PCB and EMS companies? In this interview, mergers and acquisitions expert Tom Kastner breaks down the forces reshaping the industry—why foreign investors are eager to enter the U.S. market, why many are evaluating greenfield facilities over acquisitions, and why the high-mix, low-volume focus of most domestic shops doesn’t always align with foreign buyers’ goals.
SoftBank Group and Intel Corporation Sign $2B Investment Agreement
08/19/2025 | Intel CorporationSoftBank Group Corp. and Intel Corporation today announced their signing of a definitive securities purchase agreement, under which SoftBank will make a $2 billion investment in Intel common stock.
Kimball Electronics Mexico Hosts First-Ever Charity Run in Reynosa to Support Children Battling Cancer
08/19/2025 | Kimball ElectronicsKimball Electronics Mexico (KEMX) proudly organized its first-ever Charity Run at the Polideportivo of Reynosa, bringing together employees and their families for a meaningful cause.
Green Electronics Manufacturing Market to Grow $131.64 Billion by 2032, at 25.83% CAGR
08/19/2025 | Globe NewswireThe Green Electronics Manufacturing Market size was valued at USD 21.00 billion in 2024 and is expected to reach USD 131.64 billion by 2032, growing at a CAGR of 25.83% over the forecast period of 2025-2032.
University Of Minnesota Team Claims Victory In Bright Manufacturing Challenge 2025 Round 1
08/19/2025 | EMACThe Electronics Manufacturing & Assembly Collaborative (EMAC) recently announced that Team "Rise and Grind Crew" from the University of Minnesota has emerged victorious in Round 1 of the Bright Manufacturing Challenge 2025.