-
- News
- Books
Featured Books
- pcb007 Magazine
Latest Issues
Current IssueInventing the Future with SEL
Two years after launching its state-of-the-art PCB facility, SEL shares lessons in vision, execution, and innovation, plus insights from industry icons and technology leaders shaping the future of PCB fabrication.
Sales: From Pitch to PO
From the first cold call to finally receiving that first purchase order, the July PCB007 Magazine breaks down some critical parts of the sales stack. To up your sales game, read on!
The Hole Truth: Via Integrity in an HDI World
From the drilled hole to registration across multiple sequential lamination cycles, to the quality of your copper plating, via reliability in an HDI world is becoming an ever-greater challenge. This month we look at “The Hole Truth,” from creating the “perfect” via to how you can assure via quality and reliability, the first time, every time.
- Articles
- Columns
- Links
- Media kit
||| MENU - pcb007 Magazine
Cicor’s Approach to Miniaturization: Cost of Function, and More
January 22, 2018 | Barry Matties, I-Connect007Estimated reading time: 14 minutes
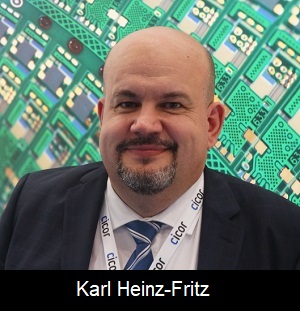
Cicor is a Swiss PCB manufacturer offering turnkey solutions and HDI work to their customer base, which currently includes four of the five biggest hearing aid manufacturers in the world. Barry Matties spoke with Karl Heinz-Fritz, VP of technology, about Cicor’s newest product line, which can shrink the size of a circuit by up to 40%, and the importance of measuring the cost of functionality.
Barry Matties: Karl, I understand you have 25 years of experience in PCB fabrication. Please tell our readers a bit about that.
Karl Heinz-Fritz: Well, I'm Austrian. I was working for several companies in this business. The first 13 years I spent at AT&S, and then I moved to Norway for a year. Then I went to Switzerland, working for Dyconex for almost four years. Since February 2011, I've been with Cicor in different positions, currently working as vice president of technology for Cicor Group.
Matties: In your PCB days, what was your role?
Heinz-Fritz: I started as a chief operator in the electroplating and plating department, and I did several jobs in the quality department. I spent something like seven years as production manager. But I always have had a very strong affinity for technology, and I think that's where I most like to work.
Matties: That gave you a good balance or overview of the entire process.
Heinz-Fritz: Exactly. I know the business pretty much from that basis.
Matties: What do you do as VP of technology?
Heinz-Fritz: I'm responsible for technology development, dealing with all of our product groups. Given my background in electronics, meaning substrate manufacturing, PCBs, thin film circuits, thick film circuits, as well as the micro-assembly of these boards, a big part of my role is to elaborate solutions together with customers. And that is what I like the most about this job: making contact with customers, trying to find solutions, and trying to offer alternatives if something is not possible or feasible. I don't like to say, "No, that's not possible." This is also what I'm encouraging my people to do, to try to offer options to help our customers to make products more stable, more reliable. Design for manufacturability is a big part of our business.
Matties: When you say you're meeting with a customer, are you referring to OEMs, designers, or all of them?
Heinz-Fritz: All of them. Going through OEMs, trying to show our capabilities and our expertise along the value chain. Of course, some want just PCBs. There is the focus, clearly, on PCBs. But what I see as one of the biggest advantages in Cicor is the diversity of work we can do. So we can do PCBs, but we can also do up to a finished device.
Matties: You're a turnkey solution, right?
Heinz-Fritz: Absolutely. We have our own development departments where we are doing product development as well, and that makes it interesting. That's the most interesting part, to make best of what we have to offer our customers.
Matties: Tell me a little bit about your manufacturing facility.
Heinz-Fritz: Our PCB manufacturing facility is in Western Switzerland, close to Neuchatel, pretty much in the middle between Zürich and Geneva. In August last year, we had the 50th anniversary there. The initiator of this PCB business was the Swiss watch industry, which still plays an important role, but not as strong as it was in the past.
Matties: The phone has taken over.
Heinz-Fritz: Yes, exactly. The phone, not so much the smart watch, but the phone. And around this expertise, we've of course improved our capabilities to do more complex boards. Our PCB shop is specialized in miniaturized printed circuit boards with a lot of flex circuit manufacturing, multilayer flex circuits. Four out of the five biggest hearing aid manufacturers worldwide, that's one of our core competencies. There is a need for ever-smaller devices.
Matties: So you're doing HDI there?
Heinz-Fritz: Yes, absolutely. We are currently running HDI in significant volumes, 2-mil lines and spaces, for several areas in the medical industry. There are hearing aid manufacturing things that we think about, like making units more than just a sound or noise amplifier. There is a need for further miniaturization to integrate more functionality within this device.
Matties: What sort of functionality?
Heinz-Fritz: For example, different sensors. Currently, the average age of a person who gets their first hearing aid is around 65 to 67 years, and very often these people have not just a loss of hearing but also other medical conditions. Companies are thinking about, for example, putting gyroscopes in to detect whether this person is falling. They would like to integrate temperature sensors, blood oxygen separation sensors, and a bunch of different things into the hearing aid to make it a multi-purpose device.
Matties: All in the size of a thumbtack.
Heinz-Fritz: Exactly. The size of hearing aid has historically always been a major concern for patients wearing it. Of course, they don't want to make the hearing aids bigger, and there is a need for further miniaturization. That is what we were working on in the past, and this is what our new product line, DenciTec® is about, mainly. We can do line width and spacing down to 1 mil, still enabling us to keep the full range of interconnection technology like stacked vias, staggered vias and via-in-pad structures. DenciTec® technology is enabling our customers to either shrink the size of a circuit by up to 40%, keeping the functionality the same, or use the gained 40% to put additional functions in. This is what this technology is about, and all that at a very attractive price. So, we are calling it “cost of function.” It means the PCB area is slightly more expensive, as the process is more complex, but you can get more functionality in it. That means the cost of function is at the same level as the standard board and what they consider a standard PCB.
Matties: Do many companies look at that, or is this kind of new?
Heinz-Fritz: We have several companies, especially from the medical industry, looking at the cost of function.
Matties: A justification for the higher prices.
Heinz-Fritz: Exactly.
Matties: That makes it easier for you to sell it.
Heinz-Fritz: Absolutely. And there are several companies offering 25-micron lines and spaces for these types of projects or products. But they have to do concessions, especially in terms of copper thickness. They are typically somewhere in the range of, let's say, 6−10 microns, while we still can maintain 20 microns, which is crucial for the wireless function of a hearing aid. Most of these new hearing aids are working wirelessly. Most of them, the strongest growing part, are connected to smartphones. They're working on the 2.4 gigahertz band right now, and there you need to have a certain copper mass to make it still work, and this is not possible. Well, it is still theoretically possible if you have just 6−10 microns of copper, but you would increase the size of the circuit again. That’s a downside we don't have with our technology.
Matties: Is this a technology that is exclusive to you? Or is this something that you are licensing to others as well?
Heinz-Fritz: Currently, it is exclusive to us, but I don't want to exclude the possibility of licensing it.
Matties: It seems like your technology would be a viable product in its own right.
Heinz-Fritz: Yes. And what makes it so special is we also can do that on flex circuits, where you currently are not able to use a standard substrate manufacturing process, delivering this line within spaces.
Matties: So how does the new process work? Tell me about the application.
Heinz-Fritz: Well, I cannot go into too much in detail, but it's neither a semi-additive process, nor is it a subtractive process. It is something in between where we are using PCB materials as well as PCB processes, only. That makes it possible for us to do that, what we did there, which is look at what we can do with what we have in our production, and that's what was the background behind this development.
Matties: So it has evolved out of the production processes that were already in place.
Heinz-Fritz: Exactly. We shuffled the processes around a bit, using new, advanced alignment methods, for example, to make sure that the boards work the way they should without making any concessions on reliability.
Matties: It sounds like you have a good R&D department.
Heinz-Fritz: Well, "R" is probably a bit too much; it's more product development. It's more application engineering, and there we have am excellent team to do that. Very open-minded people looking for solutions, and looking for new ways to produce products to offer something to the market that differs from our competitors, because Switzerland is not classically a low-cost country, so you need to offer something that has a value-add.
Matties: In miniaturization, I understand where this product plays a big role. What other sorts of applications are there? Is there a durability factor that comes with this that could be applied to, say, automotive applications?
Heinz-Fritz: Well, if there's need for that, I don't want to exclude it. Currently, the biggest interest is coming from medical industry. For example, ultrasound probes.
Matties: For the miniaturization?
Heinz-Fritz: Well, in this particular case, it's less about making it smaller, but about having a higher signal density on the circuits. In the past there was a two-dimensional, monochromatic ultrasound. Currently, there are color, three-dimensional ultrasound devices. The amount of signal has just increased dramatically, and the ultrasound probe should keep the same size. So it's not necessarily making the device smaller, and this is exactly one of the cases which allows our customer to get more functionality in the device. Keeping the shape and size of the ultrasound probe the same, but enabling a much higher amount of signals.
Matties: Has the cellphone market taken notice? It seems like this would be a classic example of functionality.
Heinz-Fritz: We had some very interesting discussions with well-known cellphone manufacturers around that. The thing is that the cellphone market, the consumer market, is not necessarily in our focus for the time being.
Matties: But your product group… This might be an area where licensing would be a good play.
Heinz-Fritz: Absolutely. That could very well be interesting for them. Yes.
Matties: And it would be a well-received license if they could add that functionality, because it's all about, "How much can we jam into these things now?" So in your years of experience, what is the thing that may have surprised you the most?
Heinz-Fritz: That's a very good question. The market development, and as quick as our Asian competitors are catching up, that's one of the bigger surprises I have. But, of course, they're putting a lot more resources into it, and buying knowledge and buying expertise by hiring people. For example, if you see Huawei, they have 70,000 development engineers working worldwide, with a lot of them sitting in Europe, coming from former companies like Ericsson and Nokia, trying to get the knowledge out of that. But, as it's been a very dynamic market since I've been working in this business, there's nothing surprising me anymore.
Page 1 of 2
Testimonial
"Advertising in PCB007 Magazine has been a great way to showcase our bare board testers to the right audience. The I-Connect007 team makes the process smooth and professional. We’re proud to be featured in such a trusted publication."
Klaus Koziol - atgSuggested Items
How Good Design Enables Sustainable PCBs
08/21/2025 | Gerry Partida, Summit InterconnectSustainability has become a key focus for PCB companies seeking to reduce waste, conserve energy, and optimize resources. While many discussions on sustainability center around materials or energy-efficient processes, PCB design is an often overlooked factor that lies at the heart of manufacturing. Good design practices, especially those based on established IPC standards, play a central role in enabling sustainable PCB production. By ensuring designs are manufacturable and reliable, engineers can significantly reduce the environmental impact of their products.
50% Copper Tariffs, 100% Chip Uncertainty, and a Truce
08/19/2025 | Andy Shaughnessy, I-Connect007If you’re like me, tariffs were not on your radar screen until a few months ago, but now political rhetoric has turned to presidential action. Tariffs are front-page news with major developments coming directly from the Oval Office. These are not typical times. President Donald Trump campaigned on tariff reform, and he’s now busy revamping America’s tariff policy.
Global PCB Connections: Understanding the General Fabrication Process—A Designer’s Hidden Advantage
08/14/2025 | Markus Voeltz -- Column: Global PCB ConnectionsDesigners don’t need to become fabricators, but understanding the basics of PCB fabrication can save you time, money, and frustration. The more you understand what’s happening on the shop floor, the better you’ll be able to prevent downstream issues. As you move into more advanced designs like HDI, flex circuits, stacked vias, and embedded components, this foundational knowledge becomes even more critical. Remember: the fabricator is your partner.
MKS’ Atotech to Participate in IPCA Electronics Expo 2025
08/11/2025 | AtotechMKS Inc., a global provider of enabling technologies that transform our world, announced that its strategic brands ESI® (laser systems) and Atotech® (process chemicals, equipment, software, and services) will showcase their latest range of leading manufacturing solutions for printed circuit board (PCB) and package substrate manufacturing at the upcoming 17th IPCA Show to be held at Pragati Maidan, New Delhi from August 21-23, 2025.
MKS Showcases Next-generation PCB Manufacturing Solutions at the Thailand Electronics Circuit Asia 2025
08/06/2025 | MKS Instruments, Inc.MKS Inc, a global provider of enabling technologies that transform our world, today announced its participation in Thailand Electronics Circuit Asia 2025 (THECA 2025), taking place August 20–22 at BITEC in Bangkok.