Riding the Tsunami of Success in Asia
January 23, 2018 | Barry Matties, I-Connect007Estimated reading time: 21 minutes
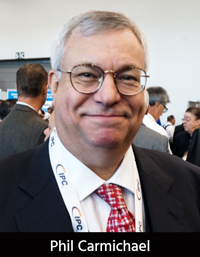
Since Phil Carmichael has overseen IPC Asia, the program and its membership have grown substantially, and with good reason. Phil met with Barry Matties at HKPCA to discuss how IPC offerings such as the QML program and helping suppliers become CSR compliant has allowed IPC to become a vital resource for suppliers in Asia.
Barry Matties: Good to see you, Phil.
Carmichael: Welcome to Shenzhen and to the booming country of China.
Matties: It's amazing what I'm seeing here. It's really incredible. Yesterday, John Mitchell told me about some of the success you've had here in China. I think you've been with IPC for about five and a half years now, and at that point there were maybe 300 members. And now I think you've hit 1000 members?
Carmichael: That's right.
Matties: Congratulations.
Carmichael: I started in fourth quarter of 2012, and we have been successful in adding members every year on a steady basis; we're over 1000 and we continue to grow.
Matties: Where do you see the drive for people who come in? Is it around the education offering?
Carmichael: There's a couple of different value propositions, depends on the company. One of them is that we developed a couple years ago, a process called the QML and QPL. It's the Qualified Manufacturing List, and the objective for that is to have a qualified, highly technical audit of your processes and your plan that will actually reduce the number of audits that your OEM will make. So, we've had success with a couple of major OEMs who have said, "Okay, we like the process," and they have now driven it in to their supply chain, and so the suppliers are being told, "Okay, you want to sell to us, that's great. Go do this QML and get qualified, and then we have to audit you less," so it's a win-win for both sides. Internal audits are always a difficult thing for both the supplier and the OEM, and if you can reduce that and also upgrade your quality, that's in everybody's interest.
So that's one of the drivers; we've had really great success with that program. The QML program has been more successful in China than anywhere in the world. And that's partly because there's more manufacturing here. The other thing that I've mentioned before is that direct engagement makes a big difference. Here in Asia, we talk to people face to face more than we do by sending email blasts, so that we here in China, every member company who is a member of IPC has a person who is a portal into IPC, an actual live person that they talk to. They can pick up the phone and say, "Hey, the new 610 G version's coming out, do you want to schedule training or do you want to get some hard copies for your factory?" We proactively talk directly to our members.
Each of our member relationship staff have probably 50 to 60 companies that they talk to directly. Think about it that way; it means they can devote a week of time to each person. That ought to be very effective. In addition, we have a toll-free number in China that is used for customer service, but we're like the Maytag people—we don't get a lot of customer service calls because we're responsive. So that function also turns around and does direct calling to our members to make sure that they're satisfied, they have issues, and so on, so forth. All those things put together, and a strong team, means that we're going to continue to grow here.
Matties: John said that membership globally is going up as well and this show looks great.
Carmichael: I think the traffic was good yesterday; I'm not sure how strong it'll be today, but it’s had good traffic.
Matties: This show looks great and what's interesting is I'm seeing a lot of first-time Americans here looking at equipment, and some Americans and Europeans who have been coming for many years. One of the comments that really strikes me is that they don't have the options for equipment in their regions like they see here. For example, drills. There's 12-15 different drills to choose from here, maybe more.
Carmichael: And guys who do soldering, there's 10 of those. You can pick everything you want.
Matties: And then the other comment I heard is that the quality of the equipment they're seeing here has gone up substantially; even in the last two years, there's a noticeable increase.
Carmichael: I'd say that's true. I think that as China moves up the knowledge value chain, they're making more sophisticated equipment and just like anywhere else, the fact that they compete regionally with Japan and Korea means that they have to up their game. So that the quality of equipment is very high.
Matties: Now, your responsibility is not just for China, you're all of Asia.
Carmichael: Yes. All of Asia, except for India.
Matties: So, when you look at China, what are the current trends here and what should people be aware of?
Carmichael: One of the things, and I can't be too specific, but we're going to be putting some more resources further west. The reason is because the Chinese government is putting more resources further west. They periodically have talked about this in the past, but they're pretty serious about it now and it's part of the Belt and Road initiative, and there's more resources moving to Szechuan and provinces to the west, and so we will be doing some in that line as well. I do see that government is serious about that, and I had a chance last year, I was at an event in Chongqing, and I decided to take a train back to Qingdao, which is an all-day process, but it is only a single-day process. I left at 6:50 a.m. and got back at 9:00 p.m. I basically saw all of China, and for the first two hours, you're in the mountains going through Szechuan, and the rest of the time you're looking at factories the whole way back. It's amazing.
It's time to move more off of the coast and inland, because the cost of manufacturing is more competitive and so forth. So I see that happening. I see specialization happening, so we run technical seminars across the country. In the past, they’ve been about high reliability or tin whiskers and soldering, this type of thing. What I see coming next is we will have a high-reliability conference that's only focused on automotive, or a high-reliability conference that's focused on aerospace and space technology.
Matties: It's market-driven.
Carmichael: Market-driven, customer-focused, and there are certain elements within industries that are specific to that industry. So, I think that you'll see more targeted and focused technical events across the country. We just finalized our calendar, and I think we've got 24 booked for next year, which is up from, again, talk about growth, when I first came here we had three a year, and now we're up to 24. So, it's a pretty sizeable growth. Each of these conferences usually have between 150 and 200 participants, so it's pretty big.
Matties: There's a strong thirst for this knowledge. When you first started coming to China, it wasn't just a day to get around, you would have to plan by the week it seems, right?
Carmichael: Well, when I first came to China, Barry, it was 1976 and you could not buy a round trip airfare. You had to have an invitation to go visit someone, and you got there and the first thing you wanted to do would be to say, "How long are we going to be here?" Because you don't have a ticket out. That's how difficult it was.
Matties: It seems like there was only one flight a week out as well.
Carmichael: Mondays and Fridays, and it was the same people coming in and going out. It was a challenge in the old days. You look at it today, and I think a couple things have happened. One is, the Chinese government recognized that they could not go landline in this country, they'd use the entire world's copper supply and still be short, so they jumped over to mobile. They looked at saying, "Well, gee, we're going to be buying 50% of the world's airplanes, and we can't afford that, so we'll do two things. We'll build our own, and then we'll also put high-speed rail across the country." Which they did in, I don't know, three years, and it's everywhere. The fact that you can go from Chongqing to Qingdao in 14 hours is amazing. I'd say that the infrastructure here, if you step back and compare within the region, this is one thing that the Chinese are very good at, is building infrastructure. From a business standpoint, what drives business is the ability to move around easily and get to places and to have the support that you need, and China has figured that one out.
Matties: There's also a cultural shift, a generational shift going on in the industry as well. We see the millennials in America, but we also see that here in China. What sort of impact does that have on the manufacturing? Job-hopping is one trend that we've seen.
Carmichael: I have heard people say that there's a strand in Chinese DNA that says every Chinese wants to be an entrepreneur and have their own company, and there are a lot more Chinese people under 40 who are thinking about their own business than anywhere else. Certainly more than in Europe, and maybe more than even in the U.S. We're also going through a shift where somebody's father started a company, grew it to a certain size, and now one of the sons or daughters is ready to step up and take it over, and surprisingly, in this industry at least, that seems to be going fairly smoothly. There are a lot of places where the son goes off to the UK or U.S., gets educated, and says, "Yeah, I'm not going to do this type of thing anymore." I sat with three different people yesterday who are all in that category, second generation taking over a father's business and fully committed and interested in doing this. Maybe it's because this is still a growth industry.
The point that people should remember is that yes, my team has grown IPC in China for sure, but the whole pie has grown as well. Electronics are ubiquitous in everything now, and we just need more of them, whether it's in your refrigerator or your smartphone, or in the control systems that allow high-speed rail to have 20 trains on the same line without touching each other, because they're communicating very carefully through a wireless mobile system.
Page 1 of 2
Suggested Items
RF PCB Design Tips and Tricks
05/08/2025 | Cherie Litson, EPTAC MIT CID/CID+There are many great books, videos, and information online about designing PCBs for RF circuits. A few of my favorite RF sources are Hans Rosenberg, Stephen Chavez, and Rick Hartley, but there are many more. These PCB design engineers have a very good perspective on what it takes to take an RF design from schematic concept to PCB layout.
Trouble in Your Tank: Causes of Plating Voids, Pre-electroless Copper
05/09/2025 | Michael Carano -- Column: Trouble in Your TankIn the business of printed circuit fabrication, yield-reducing and costly defects can easily catch even the most seasoned engineers and production personnel off guard. In this month’s column, I’ll investigate copper plating voids with their genesis in the pre-plating process steps.
Elephantech: For a Greener Tomorrow
04/16/2025 | Marcy LaRont, PCB007 MagazineNobuhiko Okamoto is the global sales and marketing manager for Elephantech Inc., a Japanese startup with a vision to make electronics more sustainable. The company is developing a metal inkjet technology that can print directly on the substrate and then give it a copper thickness by plating. In this interview, he discusses this novel technology's environmental advantages, as well as its potential benefits for the PCB manufacturing and semiconductor packaging segments.
Trouble in Your Tank: Organic Addition Agents in Electrolytic Copper Plating
04/15/2025 | Michael Carano -- Column: Trouble in Your TankThere are numerous factors at play in the science of electroplating or, as most often called, electrolytic plating. One critical element is the use of organic addition agents and their role in copper plating. The function and use of these chemical compounds will be explored in more detail.
IDTechEx Highlights Recyclable Materials for PCBs
04/10/2025 | IDTechExConventional printed circuit board (PCB) manufacturing is wasteful, harmful to the environment and energy intensive. This can be mitigated by the implementation of new recyclable materials and technologies, which have the potential to revolutionize electronics manufacturing.