-
- News
- Books
Featured Books
- pcb007 Magazine
Latest Issues
Current IssueInventing the Future with SEL
Two years after launching its state-of-the-art PCB facility, SEL shares lessons in vision, execution, and innovation, plus insights from industry icons and technology leaders shaping the future of PCB fabrication.
Sales: From Pitch to PO
From the first cold call to finally receiving that first purchase order, the July PCB007 Magazine breaks down some critical parts of the sales stack. To up your sales game, read on!
The Hole Truth: Via Integrity in an HDI World
From the drilled hole to registration across multiple sequential lamination cycles, to the quality of your copper plating, via reliability in an HDI world is becoming an ever-greater challenge. This month we look at “The Hole Truth,” from creating the “perfect” via to how you can assure via quality and reliability, the first time, every time.
- Articles
- Columns
- Links
- Media kit
||| MENU - pcb007 Magazine
Orbotech’s Strategic Decision for End-to-End Partnership Benefits Everyone
February 14, 2018 | Barry Matties, I-Connect007Estimated reading time: 14 minutes
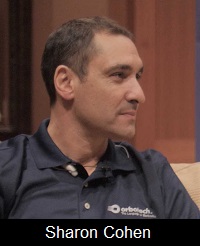
Barry Matties met with Sharon Cohen, president of Orbotech West, at productronica 2017 to discuss what’s new at Orbotech, specifically their shift to be more customer-centric and to provide regional coverage across the globe. He also discusses the current trends in the marketplace and Industry 4.0.
Barry Matties: Sharon, can you start by telling us a little bit about the show?
Sharon Cohen: First of all, this show has been very successful for us. We expected it to be busy, but it completely exceeded our expectations. We started off with a thank-you dinner for close to 100 of our long term customers and partners. This set the tone for the rest of the show which was both busy and very productive, with more than a hundred meetings each day.
Matties: Were those all pre-arranged meetings, or was a lot of this spontaneous, as well?
Cohen: About 50% of the meetings were pre-arranged, so we expected a busy show. But it ended up being much busier than we expected. It was successful and we got a lot of feedback from our customers and fielded a lot of questions. Our customers shared their plans for moving forward, and of course, we had the opportunity to share our plans as well. So all in all, it was a very productive show.
Matties: What kind of concerns or questions are your customers coming to you with at this time?
Cohen: There’s a lot of focus on increasing productivity and throughput as the world of PCB manufacturing becomes more and more competitive. Our customers want to know how can they improve their production quality and how can they make sure that they remain competitive, not just for the short term but also for the long term. They also want our opinion on the manufacturing trends in China and Asia and how those trends may impact the European and the U.S. market.
Matties: And when they ask about the trends, what sort of response are you giving them?
Cohen: So first of all, in Asia we see a clear move towards mSAP, the modified semi-additive process, with finer lines and additional layers. We see increased HDI participation in other segments as well, such as automotive and more. And we also see those trends coming here in the future. Right now, the Western market is mainly focused on QTAs and prototypes, and they are looking for solutions to improve the turnaround time.
Matties: Here in Europe, I hear reports that the economy is doing quite well. The industry is robust at the moment. I'm guessing that's the same sort of feeling you have as well?
Cohen: Absolutely. Actually, we had a conversation here about an hour ago with a couple of suppliers who also admitted that it was a better year for them than they expected. I can see from our angle, we're working with most of the PCB manufacturers here in Europe. We see a lot of busy shops, a lot of customers trying to increase their capacity. It's a great opportunity for them to explore new technologies, and a great opportunity for us to assist.
Matties: Part of the understanding is that Orbotech is becoming more customer-focused. Tell me about that. What is the strategy now with your customers?
Cohen: True. So first of all, we changed our structure not just to become more customer-friendly, but also to become the best partners we can possibly be to our customers. The process started about a year and a half ago, when we began the restructuring. We shifted to a regional structure to help us create and maintain long-term relationships with our customers and to support their different needs—not just for specific purposes like post-sales or problem solving, but actually so that we could listen better to our customers’ needs and build strong relationships that would enable us to anticipate more and plan together. That was the first phase.
The next stage was the monitoring center. We created capabilities that we could remotely monitor, and that could provide us with actionable intelligence which we use to improve our customers’ experience. I’ll give you an example. We have the ability to know ahead of time if a particular machine is going to need maintenance or a part replaced. We can act on that intelligence and schedule the repair before an error occurs and can even prevent it from happening. These actions provide more flexibility to our customers, since the downtime can be scheduled at their convenience, at a time that will cause the least disruption possible. This is something that we're really proud of, and we're putting a lot of effort into this.
Matties: Orbotech has such insight and a wealth of information, because you're in a lot of different aspects, from imaging and beyond. Your data must just give you such an incredible advantage in product development and customer service. How do you use that data?
Cohen: It ties back in to the technology. Our goal is to increase the capacity and offer better support. We changed the organizational structure, we created the monitoring center, and we're actively supporting the yield of our customers. Last year we introduced the Precise™ 800, our automated optical shaping solution or AOS as we call it. The Precise leverages two incredibly innovative technologies—3D Shaping (3DS) Technology™ and Closed Loop Shaping Technology™—that allow for copper deposition as well as copper ablation, so we can increase the yield and the throughput of our customers. The data allows for partnering on the process, maintaining, and monitoring the performance, and helping at the tail end of the production to make sure that our customers can deliver what they need to their customers.
Matties: You introduced the Precise about a year or so ago. How many installs do you have, and how's that working out?
Cohen: I'm not able to share exact numbers of installation base, but I can say that we're very proud, and very successful.
Matties: But you have it out in the field, and it's being used?
Cohen: Absolutely. We have tens of machines already working in Europe, in the U.S. and, of course, in Asia, where the biggest install base is so far.
Page 1 of 3
Testimonial
"In a year when every marketing dollar mattered, I chose to keep I-Connect007 in our 2025 plan. Their commitment to high-quality, insightful content aligns with Koh Young’s values and helps readers navigate a changing industry. "
Brent Fischthal - Koh YoungSuggested Items
Indium Corporation Promotes Two Leaders in EMEA (Europe, Middle East, and Africa) Markets
08/05/2025 | Indium CorporationWith its commitment to innovation and growth through employee development, Indium Corporation today announced the promotions of Andy Seager to Associate Director, Continental Sales (EMEA), and Karthik Vijay to Senior Technical Manager (EMEA). These advancements reflect their contributions to the company’s continued innovative efforts with customers across Europe, the Middle East, and Africa (EMEA).
MacDermid Alpha Electronics Solutions Unveils Unified Global Website to Deepen Customer, Talent, and Stakeholder Engagement
07/31/2025 | MacDermid Alpha Electronics SolutionsMacDermid Alpha Electronics Solutions, the electronics business of Elements Solutions Inc, today launched macdermidalpha.com - a unified global website built to deepen digital engagement. The launch marks a significant milestone in the business’ ongoing commitment to delivering more meaningful, interactive, and impactful experiences for its customers, talent, and stakeholders worldwide.
KOKI to Showcase Analytical Services and New HF1200 Solder Paste at SMTA Guadalajara 2025
07/31/2025 | KOKIKOKI, a global leader in advanced soldering materials and process optimization services, will exhibit at the SMTA Guadalajara Expo & Tech Forum, taking place September 17 & 18, 2025 at Expo Guadalajara, Salón Jalisco Halls D & E in Guadalajara, Mexico.
Weller Tools Supports Future Talent with Exclusive Donation to SMTA Michigan Student Soldering Competition
07/23/2025 | Weller ToolsWeller Tools, the industry leader in hand soldering solutions, is proud to announce its support of the upcoming SMTA Michigan Expo & Tech Forum by donating a limited-edition 80th Anniversary Black Soldering Set to the event’s student soldering competition.
Koh Young Appoints Tom Hattori as President of Koh Young Japan
07/21/2025 | Koh YoungKoh Young Technology, the global leader in True 3D measurement-based inspection solutions, announced the appointment of Tom Hattori as President of Koh Young Japan (JKY).