Part 2: EIPC’s Winter Conference in Lyon, France: Day 2 Review
February 21, 2018 | Pete Starkey, I-Connect007Estimated reading time: 9 minutes
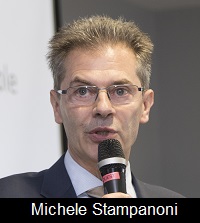
Editor's Note: If you missed the beginning of this article, click here.
The final session, on European needs for new technology, product safety and training, was introduced and moderated by EIPC board member Dr. Michele Stampanoni, vice president of strategic sales and business development at Cicor Group.
His first presenter was Emma Hudson, vice-chairman of EIPC and UL’s industry lead for PCBs in Europe, the Middle East, Africa, and Latin America, continuing in her campaign to help the PCB industry through the safety certification process, this time by advising how the solder limits for UL-Recognised PCBs required to be updated to reflect the realities of surface mount assembly soldering processes. She explained that solder limits represented the soldering processes the PCB would be exposed to during assembly, and that many PCB fabricators were using outdated values related to wave soldering, where the traditional solder float conditions did not represent current SMT soldering processes. It was clear there was a significant possibility that PCBs passing the solder float test would not pass when SMT soldering processes were used. Therefore, using inaccurate solder limits for safety testing was not acceptable and if the recognised solder limits were exceeded in production then the recognition, which was in effect the safety assessment, would be invalidated,
To help make implementation easier, UL would be offering standardised soldering profiles based on IPC-TM-650 2.6.27 T230 and T260, although it was acknowledged that many different product-specific soldering profiles were in use, and that fabricators could define their own limits if they meaningfully represented the conditions their boards would experience. Ms. Hudson gave comprehensive guidance on how to define and interpret solder limits, and described the procedures for updating them for different base materials and multilayer constructions, explaining where the CCIL Program could and could not be used. Similarly, for solder resists, with examples of when the permanent coating program could and could not be used.
She advised that, commencing in 2018, UL follow-up services would require evidence of the actual soldering profiles used for the PCB assembly, to confirm that the soldering processes to which the PCB had been exposed did not exceed the recognised solder limits and so invalidate the recognition. But UL were prepared to help, and she urged fabricators to get in touch and get their requalification programmes in progress without delay.
In his presentation on printed electronics for flexible and conformal applications, Dr. Neil Chilton, technical director at Printed Electronics Limited (PEL), grouped printed electronics, flexible electronics, plastic electronics and organic electronics under one collective heading: large-area electronics, meaning processes that could be employed on roll-to-roll substrates or those that were generally in larger format than PCB or silicon processes. He gave a background to the market, which was expanding rapidly in the areas of displays and lighting, power, and logic and memory. There was a substantial market in printed sensors, dominated by mass-produced glucose test strips, but sustained growth was forecast for non-bio sensors, principally photodetectors, gas sensors and temperature sensors. In stretchable electronics, the key innovation areas were stretchable inks, flex-to-rigid connections, and sensor structures and materials. And sportswear was leading the way in Smart clothing.
IDTechEx had forecast that the market for stretchable and conformable electronics would reach $600M by 2017, and Dr. Chilton explored the opportunities for nano-metal inkjet printed circuits in this technology area. The principal benefit was that circuits could be printed directly onto a pre-existing surface, so eliminating the substrate and its weight. Because the technique was digital, additive and direct, it gave the benefits of additive manufacturing. A limitation was that the circuitry was usually thinner, more fragile and more resistive than conventional electronics, and could not carry significant current. He considered that single layers of inkjet were more applicable to direct-printed sensors than to general circuitry. However, if inkjet was used to print a seed layer, more substantial conductors could be built up with electroless copper.
Generally, inkjet inks were very low viscosity, so they needed a high-quality substrate and could not achieve the same resolution as photolithography. Neither was it easy to print on 3D surfaces. But PEL had developed a system for printing viscous inks by digital 3D deposition, which gave thicker deposits and could be used for antennas. Dr. Chilton showed examples of printing on cylindrical pre-forms for defence applications. It was also possible to use the technique for producing embedded electronics.
Continuing the theme of printed electronics, Hortense Gaya, product manager for DuPont PVAM inks at CCI Eurolam, discussed the latest developments in materials for applications in wearables and in-mould electronics.
She began by describing the formulation of a conductive ink: The base polymer required good elasticity, good adhesion to substrates and the ability to withstand high temperatures. The solvent needed the ability to effectively solubilise the polymer to give good screen printing properties and to be compatible with printed circuit and graphics inks. The filler could be a dielectric, the choice depending on whether it was for an under-print or an over-print application, or a conductor, for example silver or carbon. The resulting functional ink should have a balance of conductivity and stretchability, and a balance of viscosity and good printing properties, as well as compatibility with substrates and graphic inks.
The market for wearable electronics was expanding rapidly, predominantly in sport and fitness and healthcare, but also in home and lifestyle, industrial, commercial and military applications. Smart sportswear could monitor heart rate, breathing and muscle fatigue, using for example silver paste as a conductor and silver/silver chloride as electrodes and dielectric, optimised for stretchability and adhesion to a thermoplastic polyurethane substrate to give a comfortable garment. Combination with active components could enable wireless communication, processing of data and intelligent feedback systems. In healthcare applications, parents and caregivers could get real-time information on vital signs of infants or the elderly. In military or emergency-response situations, real-time monitoring of vital signs could protect personnel, environmental sensors could let personnel know when safety limits had been reached, and location monitoring could coordinate responses and facilitate rescue.
DuPont had developed a family of stretchable base and cover films, silver and carbon conductor inks and encapsulants specifically for applications in wearable electronics. Ms. Gaya reviewed processing techniques: combinations of screen printing, die or laser cutting and hot lamination to fabric, and discussed the evaluation and measurement of performance in terms stretchability and elastic durability, washability and comfort.
Moving on to the topic of in-mould electronics, which she defined as printed electronic circuits that had undergone a thermoforming and injection moulding process, she explained that the technique combined film, graphics and electronics, and that the circuitry, with or without mounted components, remained functional as the conductor tracks followed the contours of the 3D shape of the mould. Typical applications were 3D circuits with capacitative switches, and LED lighting controls in automotive, avionics and domestic appliances. There was a substantial weight saving, and buttons and wires were eliminated. DuPont had formulated a complete suite of electronic inks designed to survive the intense stretching and heat of the thermoforming and injection moulding processes.
Page 1 of 2
Testimonial
"We’re proud to call I-Connect007 a trusted partner. Their innovative approach and industry insight made our podcast collaboration a success by connecting us with the right audience and delivering real results."
Julia McCaffrey - NCAB GroupSuggested Items
Indium Corporation Promotes Two Leaders in EMEA (Europe, Middle East, and Africa) Markets
08/05/2025 | Indium CorporationWith its commitment to innovation and growth through employee development, Indium Corporation today announced the promotions of Andy Seager to Associate Director, Continental Sales (EMEA), and Karthik Vijay to Senior Technical Manager (EMEA). These advancements reflect their contributions to the company’s continued innovative efforts with customers across Europe, the Middle East, and Africa (EMEA).
MacDermid Alpha Electronics Solutions Unveils Unified Global Website to Deepen Customer, Talent, and Stakeholder Engagement
07/31/2025 | MacDermid Alpha Electronics SolutionsMacDermid Alpha Electronics Solutions, the electronics business of Elements Solutions Inc, today launched macdermidalpha.com - a unified global website built to deepen digital engagement. The launch marks a significant milestone in the business’ ongoing commitment to delivering more meaningful, interactive, and impactful experiences for its customers, talent, and stakeholders worldwide.
KOKI to Showcase Analytical Services and New HF1200 Solder Paste at SMTA Guadalajara 2025
07/31/2025 | KOKIKOKI, a global leader in advanced soldering materials and process optimization services, will exhibit at the SMTA Guadalajara Expo & Tech Forum, taking place September 17 & 18, 2025 at Expo Guadalajara, Salón Jalisco Halls D & E in Guadalajara, Mexico.
Weller Tools Supports Future Talent with Exclusive Donation to SMTA Michigan Student Soldering Competition
07/23/2025 | Weller ToolsWeller Tools, the industry leader in hand soldering solutions, is proud to announce its support of the upcoming SMTA Michigan Expo & Tech Forum by donating a limited-edition 80th Anniversary Black Soldering Set to the event’s student soldering competition.
Koh Young Appoints Tom Hattori as President of Koh Young Japan
07/21/2025 | Koh YoungKoh Young Technology, the global leader in True 3D measurement-based inspection solutions, announced the appointment of Tom Hattori as President of Koh Young Japan (JKY).