ESI Targets Growing HDI Space
April 5, 2018 | Stephen Las Marias, I-Connect007Estimated reading time: 7 minutes
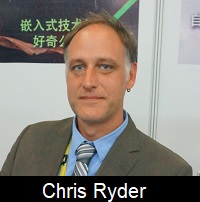
At the recent HKPCA and IPC Show 2017 in Shenzhen, China, Chris Ryder, director of product management for HDI at Electro Scientific Industries Inc. (ESI), discusses how laser-based processing is addressing the challenges in HDI development, and MSAP technology and its impact on the PCB industry.
Stephen Las Marias: Chris, for anyone who’s not familiar with your company, give us a quick background.
Chris Ryder: ESI is a laser solutions provider, and that embodies several aspects of laser processing—via drilling, cutting, routing, trim. So, when it comes to laser processing, that's ESI. We've been in the business for a long time, and we have solutions that encompass most relevant types of lasers, including various wavelengths, UV, CO2, green, etc. My role at ESI is Director of HDI product management. We’re a relatively new segment at ESI and my main focus right now is introducing our CO2 systems to the HDI/SLP via drilling market.
Las Marias: You mentioned you’re relatively new. Why? Is it because the industry is adopting more and more HDI?
Ryder: For sure. I come from the PCB industry myself, and I initially observed a slower rate of adoption in the non-communications sector in implementing and innovating HDI products. The technology had to prove itself in terms of reliability before segments like automotive and industrial applications would adopt it. It can be a challenge to implement smaller products into a smaller space with smaller vias. What we're seeing now is basically the increase in use of HDI in products across a broader range, so automotive, Internet of Things (IoT), and in the industrial sector as well. Basically, companies are making use of smaller, denser designs so they can pack these systems and the products that they're creating with more features.
Las Marias: Does 5G, which is expected to come up in 2018, offer a very bright future for HDI?
Ryder: Yes. And since HDI is joined at the hip with laser processing, ESI is an exciting place to be right now. We have a good grasp of all the different laser technologies, and also manipulating laser for the different products involved. Laser-based processing is in high demand.
Las Marias: Is laser-based processing the only efficient way to do HDI via drilling?
Ryder: Effectively, yes. Laser is certainly the best option for vias at a higher density. But what you’ll find is that as vias become smaller, as designs become denser, we’re helping customers manage the new challenges through our experience in laser processing. At ESI, our tools span the gap from semiconductor to larger-scale laser-cut products. So, we’re able to leverage this experience with fine structures, small vias and high accuracy as customers’ products become more complex and denser.
Las Marias: What are the critical challenges that your customers are facing right now?
Ryder: The main challenge right now for our customers is their own changing process landscape. The traditional subtractive process such as in the PCB industry is being increasingly challenged through what you'll hear very often called the MSAP technology. MSAP is modified semi-additive plating, and this brings with it a whole new host of design rules. Some of the companies have been dealing with this for many years, especially those PCB shops that have substrate manufacturing as well. But for a lot of companies, this presents a very big challenge, and part of that is, of course, laser drilling and all the other functions that you would get from laser-based processing.
Substrate manufacturing is typically linked to the packaging industry, so we're talking interposer or package substrate type of products. But what we're finding is that these two worlds are converging more and more. We’re seeing HDI products meet together with the design rules of a substrate package; there are different names for these products, some call them a substrate-like PCB or SLP, and some call them hybrid or convergence products. But essentially, what we're seeing is the meeting of both worlds.
Las Marias: What is the impact of this in HDI development?
Ryder: Well, what it means for us is that we have to listen even more closely to the customer, and we have to be engaged at several levels beyond the customers and try to engage with OEMs to be a little bit more proactive in determining where those designs are going to go. The point is that we want to be ready to meet the challenges before they become HVM. This engagement with the broader industry is much bigger than has been thus far. Of course, you always listen to your customers and what they want, what they need, but things are moving so fast now that you have to be a couple of steps ahead.
Las Marias: How do you position ESI in the HDI segment of the PCB industry?
Ryder: In the flex world, we’re the market leader. This has been the case for some time. In the rigid-flex world, similarly. We are somewhat new to the rigid board HDI products, with our CO2 platform nViant, but we’re by no means a beginner. We have all the experience of other ESI systems, of all our decades of processing experience built into these tools.
Las Marias: How do you see the market opportunity for it in this region [China]?
Ryder: Of course, this is the world's factory, especially for microelectronics. What I find fascinating is that by no means is this a solely commodity-based manufacturing region any more. This is a development region. In cities like Shenzhen and Shanghai, we're seeing product development at a much more advanced pace than we’ve seen thus far. It’s really great for ESI, because we have our footprint all over the region, and we engage with these customers as well as their customers, each and every day, to make that happen.
Las Marias: How do you deal with competition?
Ryder: Well, competition is a double-edged sword. So we learn a lot from our competition, we learn a lot from how they manage the problems that they're faced with, and also we learn a lot about what we're successful with and how we can build on those successes. So I think by no means do we underestimate the competition. The HDI competition is very stiff, and we're up against some very fine companies. But again, ESI brings a lot of experience, a lot of history, and a lot of very smart minds to the table, that I believe can build on what the competition cannot.
Las Marias: From your perspective, is it true that by going to HDI will save costs for manufacturers?
Ryder: This is a tricky question. It depends ultimately on what your product is and what your value proposition is. If this means that you can pack more features that give it a higher selling price, so that you can eke out more margin or you can eke out more value for your customer, then for sure. You know, this has always been the reason behind the slow development of technologies like HDI into the automotive space because automotive has typically not been space-constrained. What you're finding is that there’s not a sudden space constraint, but the demand for all the applications and features on a car are much more similar to a smartphone or PC, so you have to pack this value into a tighter device space. Part of that is because a lot of the same silicon is being used for similar applications. If you can design smartly, and you work together with your PCB manufacturers and your PCB shops, and work together with the general industry, even in terms of laser processing, I think if you do smart design, it doesn’t have to increase costs. Of course, versus a standard multilayer board, with a lower per-square-inch price? Yeah, it's going to increase costs. But the question is what value—what do you value? It's a value improvement, and if that value improvement is worth something to your customer, then ultimately, you’re going to make more money.
Las Marias: It is communication that is important, right?
Ryder: Correct. We’re an industry. No one company is completely self-sufficient. We grow on each other’s mistakes, we grow on each other’s learnings, and customers need to increasingly work together with their supply base as partners, as things become more fast-paced. Honestly, there’s more at stake for a lot of these companies, so that level of partnership has to increase.
Las Marias: Finally, what comes next for ESI when it comes to HDI?
Ryder: That’s a good question. We’re working on a lot of great things right now. We continue to develop our CO2 rigid PCB platform. We continue to add features that are important to customers, not only in the MSAP manufacturing landscape, but also in the general array of products that the customers are offering. We will continue to develop products geared towards this SLP market niche, where this convergence of substrate design rules and PCB manufacturing is happening. And simply, we'll continue to make our product a part of our customers’ industrial design, including implementation of Industry 4.0, and specific automation needs the customers may have. Again, we want to increase the value that our tool has on the customer's shop floor.
Las Marias: Thank you very much, Chris.
Ryder: Thank you for having us.
Testimonial
"The I-Connect007 team is outstanding—kind, responsive, and a true marketing partner. Their design team created fresh, eye-catching ads, and their editorial support polished our content to let our brand shine. Thank you all! "
Sweeney Ng - CEE PCBSuggested Items
Meet the Author Podcast: Martyn Gaudion Unpacks the Secrets of High-Speed PCB Design
07/16/2025 | I-Connect007In this special Meet the Author episode of the On the Line with… podcast, Nolan Johnson sits down with Martyn Gaudion, signal integrity expert, managing director of Polar Instruments, and three-time author in I-Connect007’s popular The Printed Circuit Designer’s Guide to... series.
Intervala Hosts Employee Car and Motorcycle Show, Benefit Nonprofits
08/27/2024 | IntervalaIntervala hosted an employee car and motorcycle show, aptly named the Vala-Cruise and it was a roaring success! Employees had the chance to show off their prized wheels, and it was incredible to see the variety and passion on display.
KIC Honored with IPC Recognition for 25 Years of Membership and Contributions to Electronics Manufacturing Industry
06/24/2024 | KICKIC, a renowned pioneer in thermal process and temperature measurement solutions for electronics manufacturing, is proud to announce that it has been recognized by IPC for 25 years of membership and significant contributions to electronics manufacturing.
Boeing Starliner Spacecraft Completes Successful Crewed Docking with International Space Station
06/07/2024 | BoeingNASA astronauts Barry "Butch" Wilmore and Sunita "Suni" Williams successfully docked Boeing's Starliner spacecraft to the International Space Station (ISS), about 26 hours after launching from Cape Canaveral Space Force Station.
KIC’s Miles Moreau to Present Profiling Basics and Best Practices at SMTA Wisconsin Chapter PCBA Profile Workshop
01/25/2024 | KICKIC, a renowned pioneer in thermal process and temperature measurement solutions for electronics manufacturing, announces that Miles Moreau, General Manager, will be a featured speaker at the SMTA Wisconsin Chapter In-Person PCBA Profile Workshop.