-
- News
- Books
Featured Books
- pcb007 Magazine
Latest Issues
Current IssueInventing the Future with SEL
Two years after launching its state-of-the-art PCB facility, SEL shares lessons in vision, execution, and innovation, plus insights from industry icons and technology leaders shaping the future of PCB fabrication.
Sales: From Pitch to PO
From the first cold call to finally receiving that first purchase order, the July PCB007 Magazine breaks down some critical parts of the sales stack. To up your sales game, read on!
The Hole Truth: Via Integrity in an HDI World
From the drilled hole to registration across multiple sequential lamination cycles, to the quality of your copper plating, via reliability in an HDI world is becoming an ever-greater challenge. This month we look at “The Hole Truth,” from creating the “perfect” via to how you can assure via quality and reliability, the first time, every time.
- Articles
- Columns
- Links
- Media kit
||| MENU - pcb007 Magazine
From Math to Marketing: Orbotech CMO’s Worldview of the Industry
April 9, 2018 | Barry Matties, I-Connect007Estimated reading time: 18 minutes
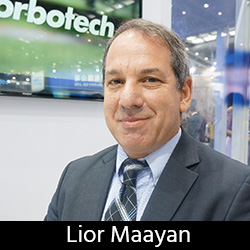
Barry Matties met with Orbotech’s corporate VP of Business Development and CMO, Lior Maayan, in Shenzhen and spoke about the next-generation processes currently challenging Orbotech's R&D team. Most notable among them are additive technologies like the automated optical shaping solution, and the growth of MSAP, flex, and HDI. Lior also offered his advice to board shops trying to survive in today’s market and how to deal with a new breed of customers.
Barry Matties: Lior, tell me a little bit about Orbotech.
Lior Maayan: Orbotech has been a world leader for over 30 years in manufacturing solutions for electronics. We have grown from initiating the AOI role for inspection into production solutions for PCBs, such as direct imaging and drilling, and added display. Over the last three years we have added etch and deposition solutions and modules for the advanced packaging and sensor world. We are involved in today's electronics in a meaningful way. For example, Orbotech's solutions touch more than 30 different modules in the recently released, most advanced generation of smartphones, and this can be seen clearly in the tear-downs.
Matties: That's quite an accomplishment. Now, you're a CMO—chief marketing officer.
Maayan: Correct, and I am the corporate vice president of business development. My basic background is math and physics. I have a master’s degree in science and engineering, and then I moved into business. I joined Orbotech over three years ago to strengthen our customer-facing abilities as well as our presence in the full ecosystem of electronics.
Matties: That's quite a jump from physicist to marketing. It works well though, because you're selling a technical product here.
Maayan: Indeed. The first challenge in resolving substantial processes is the ability to interact with our customers and with the ecosystem, understand their ‘must-haves,’ and how to translate new processes into manufacturing solutions. We are taking designers' dreams and we are taking designers' aspirations regarding how a new product should look and translating them into manufacturing processes. That calls for technical as well as business understanding. I hope that our ability as a team, and my specific responsibilities, allows us to help in that.
Matties: How much time do you spend personally with customers?
Maayan: With the ecosystem, and that means our customers and others, probably more than two-thirds of my time.
Matties: So you have real industry input from that experience?
Maayan: Sure. This industry has emerged from a state where technologies were introduced into the industry by external technical teams into an engine of creation, where the innovation comes from the industry itself, with its new processes, new materials, new production processes, and from the designers themselves, who have more and more demanding requirements. There are multiple examples of this. After the tear-downs of the last smartphones came out, we know that a new era in PCB manufacturing emerged with the SLP, or so-called MSAP processes. That shows how the industry can deliver new technologies that meet designers’ demands for smaller and denser devices with more and more functionality.
Matties: It's all about functionality, we want more and more function in the same space, or smaller. That's really the drive.
Maayan: Indeed, the fight is for space, because you want to allow for more and more battery space. If you look at the tear-down of the iPhone X, for example, you already see two batteries. This is enabled as a result of the ability to shrink the PCB, which is the third largest real-estate element in the mobile phone.
Matties: When you look at the roots, you start with AOI, but now you have a portfolio of drilling, of direct imaging, solder mask systems, the Precise™ automated optical shaping (AOS) and additive printing. Where do you head from here?
Maayan: The key is the processes. Production processes have multiple steps, and we are enabling more and more of those processes with new materials and new solutions. And that calls for a new offering. We started over 35 years ago by generating the automatic optical inspection field. Around 20 years ago, we added the first direct imaging (DI) production solution, which is now the foundation of any high-end PCB, which in turn is the foundation of all meaningful electronics. We added to that drilling, the very high-end side of drilling, inkjet solutions for marking, as well as 3D printing applications and the very important software and traceability capabilities. We're trying to answer all the digital steps of PCB and substrate manufacturing with our solutions. Because without integration between systems, the ability to deliver high yields with those processes and to improve one's ramp-up, is at risk. We have made this industry that was historically a separated, disintegrated, solution-based industry, into a combined integrated workflow. And that's where we're headed.
Matties: I know you invest a lot of money in R&D, maybe the most in the industry. When you look at your R&D, do you look at how to eliminate the process steps primarily? Take for example, direct imaging, you took multiple steps and compressed it to one. Your new AOI is taking multiple steps and bringing it into one unit. Is that a strategy that's by design, and is that what you've set out to do?
Maayan: I would say, for sure, yes. We have two by-design strategies for any production process we look at. One is to allow or enable steps which cannot be executed with today's technology. For example, one cannot repair traces of under 40 microns. It manually cannot be done. To allow for a shaping solution that will be part of the production process of PCBs, of today’s highest smartphones, one must think about, and deliver innovation, such as the automated optical shaping we brought to the market. This is one major design aim we have. The other one is to look at inefficiencies in the process, parallel activities that are done on different machines, and combine them into one set of tools. Replace more and more analog processes that are chemistry-based with laser-based and other digitalized technologies, additive technologies, which allow for streamlining the process, and optimization of cost inefficiencies.
Matties: When you look into the distant future, whatever that happens to be based on your answer, do you look at a time where it's a completely additive process that's built in a box?
Maayan: In theory, a completely additive process has advantages. At the end of the day, it should mean less initial material for the same output, and much more digitized and straight from-design-to-production processes. The optimization of subtractive processes is such that, and this is true of other industries as well, it will still take time before the theoretical advantages of additive manufacturing will step in. We are leading that transition and putting our focus where things could make a difference today. For example, our inkjet solutions, which initially are playing in this industry for marking, legend-based solutions, are already depositing material in an additive manner in some substrate and advanced packaging applications. So this is where we see we're finding the niche, in which additive is an enabling element, because it's still a long way before it will become a cost-driving element.
Matties: Your shaping is essentially an additive process, right? It's the basis for one.
Maayan: Yes. When you look at Orbotech’s automated optical shaping, it is by nature an additive process. We are depositing material and the essential part of it is that we have found the right niche in the application process that will benefit from such an enabling technology. With the additive capabilities that we have today and will have in the near-future, it is much more realistic to look at systems that add specific materials in key elements of the process, and not a full-blown replacement for PCB processes.
Matties: Like one of your neighbors, Nano Dimension. They're going from base material up. They're taking a bit of a different approach.
Maayan: Yes. Technology-wise it is achievable. We have solutions, and the industry has solutions that could build a PCB from scratch, from design to a board using 3D printing technology. The key issue is the essential applications. For years, one of Orbotech’s biggest advantages has been its ability to bring real production solutions, not only technologies to market. As a technologist, I'm always intrigued and scouting for new solutions, but the end application needs to be clear and these technologies need to be put into the right sector. What we have done is incredibly innovative as our solution is the only one on the market which takes the actual material and 3D shapes it. It is not diluted inkjet-based deposition, but the copper itself that is being deposited. We've taken it into a realistic shaping application that adds real quantifiable value to the customer, and not only plays a role as a technology demonstrator.
Matties: And with the automated optical shaping, you've redefined what PCB repair is. Because that's all it is.
Maayan: Indeed, we have. I want to maybe rephrase or re-look at the definition of repair. Repair is a secondary process, a manual process that is used to overcome defects in the production process. Shaping starts with that, but shaping goes a step further, because shaping allows you to take the original design, and when you know you have demanding design requirements, ask yourself, can I do this using an additive process? And then implement it in a very selective part of the process. By doing that, we are reshaping the ability to translate design into production, and not only replacing manual work. And we enable a process that simply cannot be done by the human eye or hand.
Matties: Because it just gets finer, and finer, and finer.
Maayan: Exactly. It cannot be done.
Matties: So it's a nice recovery of asset, by being able to provide that.
Maayan: Yes. We can say today that, to allow for the modern smartphone MSAP processes, to allow for reasonable yields, one needs a shaping element in the process. And that comes from Orbotech’s automated optical shaping.
Matties: Now let's shift gears a little. You spend two-thirds of your time with customers. What sort of issues, or demands or trends, are you seeing in the marketplace?
Maayan: That's a wide question. I would say there are clearly five or six major trends. First is a new level of PCB manufacturing—MSAP or SLP, the so-called substrate-like PCB. Related to that, is the continuum between SLP and substrate work, and advanced packaging. People are starting to offer alternative solutions to the same need, coming from different historical supply chains. Next is the dramatic growth in flex, and the dramatic growth in the functionality that flex represents in the final product. It’s not only the ability to replace the copper substrate, but the ability to act as a substrate for additional elements in a more and more meaningful way. Another trend is the emergence of high-end electronics and PCB into the automotive industry. This is a major trend that generates very positive dynamics for our industry.
People are highly engaged in automating the processes, so you see more and more automation, which relates to the demand for industry 4.0 or smart factory, which relates as well to traceability. People are becoming more and more aware of the processes that offer an automatic ability to identify yield issues and to fully track their production process at each stage of production. I think that these four or five trends clearly demonstrate how very vibrant, positive and forward-looking the industry is after experiencing a slowdown in growth for some years. Importantly, this has also resulted in another larger scale phenomenon, namely the increased involvement of the OEM design community in the supply chain. OEMs today are increasingly able to communicate with their suppliers—our customers—and demand more sophistication. The effect of that is that our industry is much more on its toes, and much more competitive and experienced.
Page 1 of 2
Testimonial
"Advertising in PCB007 Magazine has been a great way to showcase our bare board testers to the right audience. The I-Connect007 team makes the process smooth and professional. We’re proud to be featured in such a trusted publication."
Klaus Koziol - atgSuggested Items
Indium Corporation Promotes Two Leaders in EMEA (Europe, Middle East, and Africa) Markets
08/05/2025 | Indium CorporationWith its commitment to innovation and growth through employee development, Indium Corporation today announced the promotions of Andy Seager to Associate Director, Continental Sales (EMEA), and Karthik Vijay to Senior Technical Manager (EMEA). These advancements reflect their contributions to the company’s continued innovative efforts with customers across Europe, the Middle East, and Africa (EMEA).
MacDermid Alpha Electronics Solutions Unveils Unified Global Website to Deepen Customer, Talent, and Stakeholder Engagement
07/31/2025 | MacDermid Alpha Electronics SolutionsMacDermid Alpha Electronics Solutions, the electronics business of Elements Solutions Inc, today launched macdermidalpha.com - a unified global website built to deepen digital engagement. The launch marks a significant milestone in the business’ ongoing commitment to delivering more meaningful, interactive, and impactful experiences for its customers, talent, and stakeholders worldwide.
KOKI to Showcase Analytical Services and New HF1200 Solder Paste at SMTA Guadalajara 2025
07/31/2025 | KOKIKOKI, a global leader in advanced soldering materials and process optimization services, will exhibit at the SMTA Guadalajara Expo & Tech Forum, taking place September 17 & 18, 2025 at Expo Guadalajara, Salón Jalisco Halls D & E in Guadalajara, Mexico.
Weller Tools Supports Future Talent with Exclusive Donation to SMTA Michigan Student Soldering Competition
07/23/2025 | Weller ToolsWeller Tools, the industry leader in hand soldering solutions, is proud to announce its support of the upcoming SMTA Michigan Expo & Tech Forum by donating a limited-edition 80th Anniversary Black Soldering Set to the event’s student soldering competition.
Koh Young Appoints Tom Hattori as President of Koh Young Japan
07/21/2025 | Koh YoungKoh Young Technology, the global leader in True 3D measurement-based inspection solutions, announced the appointment of Tom Hattori as President of Koh Young Japan (JKY).