New 3D Printer Can Create Complex Biological Tissues
May 21, 2018 | UCLA Samueli School of EngineeringEstimated reading time: 2 minutes
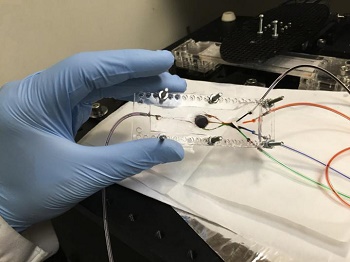
A UCLA Samueli-led team has developed a specially adapted 3D printer to build therapeutic biomaterials from multiple materials. The advance could be a step toward on-demand printing of complex artificial tissues for use in transplants and other surgeries.
"Tissues are wonderfully complex structures, so to engineer artificial versions of them that function properly, we have to recreate their complexity," said Ali Khademhosseini, who led the study and is UCLA's Levi James Knight, Jr., Professor of Engineering at the UCLA Samueli School of Engineering. "Our new approach offers a way to build complex biocompatible structures made from different materials."
The technique uses a light-based process called stereolithography, and it takes advantage of a customized 3D printer designed by Khademhosseini that has two key components. The first is a custom-built microfluidic chip -- a small, flat platform similar in size to a computer chip -- with multiple inlets that each "prints" a different material. The other component is a digital micromirror, an array of more than a million tiny mirrors that each moves independently.
The researchers used different types of hydrogels - materials that, after passing through the printer, form scaffolds for tissue to grow into. The micromirrors direct light onto the printing surface, and the illuminated areas indicate the outline of the 3D object that's being printed. The light also triggers molecular bonds to form in the materials, which causes the gels to firm into solid material. As the 3D object is printed, the mirror array changes the light pattern to indicate the shape of each new layer.
The process is the first to use multiple materials for automated stereolithographic bioprinting -- an advance over conventional stereolithographic bioprinting, which only uses one type of material. While the demonstration device used four types of bio-inks, the study's authors write that the process could accommodate as many inks as needed.
The researchers first used the process to make simple shapes, such as pyramids. Then, they made complex 3D structures that mimicked parts of muscle tissue and muscle-skeleton connective tissues. They also printed shapes mimicking tumors with networks of blood vessels, which could be used as biological models to study cancers. They tested the printed structures by implanting them in rats. The structures were not rejected.
The study's other authors include first author Amir Miri, who was a postdoctoral scholar at Harvard Medical School when the study was conducted and is now at Rowan University. The co-senior author is Yu Shrike Zhang of Brigham and Women's Hospital and Harvard Medical School. The other authors are from University of Santiago de Compostela, Spain; Sharif University of Technology, Iran; and UC San Diego.
Khademhosseini, who joined UCLA in November 2017, has faculty appointments in bioengineering and in chemical and biomolecular engineering, as well as in the David Geffen School of Medicine at UCLA. He is the director of the Center for Minimally Invasive Therapeutics and an associate director of the California NanoSystems Institute.
The study was funded by the Office of Naval Research and the National Institutes of Health.
Suggested Items
Indium Corporation Expert to Present on Automotive and Industrial Solder Bonding Solutions at Global Electronics Association Workshop
06/26/2025 | IndiumIndium Corporation Principal Engineer, Advanced Materials, Andy Mackie, Ph.D., MSc, will deliver a technical presentation on innovative solder bonding solutions for automotive and industrial applications at the Global Electronics A
Gorilla Circuits Elevates PCB Precision with Schmoll’s Optiflex II Alignment System
06/23/2025 | Schmoll MaschinenGorilla Circuits, a leading PCB manufacturer based in Silicon Valley, has enhanced its production capabilities with the addition of Schmoll Maschinen’s Optiflex II Post-Etch Punch system—bringing a new level of precision to multilayer board fabrication.
Day 1: Cutting Edge Insights at the EIPC Summer Conference
06/17/2025 | Pete Starkey, I-Connect007The European Institute for the PCB Community (EIPC) Summer Conference took place this year in Edinburgh, Scotland, June 3-4. This is the second of three articles on the conference. The other two cover the keynote speeches and Day 2 of the technical conference. Below is a recap of the first day’s sessions.
American Made Advocacy: Supporting the Entire PCB Ecosystem—Materials to OEMs
06/17/2025 | Shane Whiteside -- Column: American Made AdvocacyWith the addition of RTX to PCBAA’s membership roster, we now represent the interests of companies in the entire PCB ecosystem. From material providers to OEMs, the insights of our collective members help us educate, advocate, and support legislation and policy favorable to America’s microelectronics manufacturers. The industry veterans who lead these companies provide valuable perspective, and their accumulated wisdom makes us an even stronger association.
Ventec Strengthens Commitment to Halogen-Free PCB Manufacturing in Europe
06/11/2025 | Ventec International GroupVentec International Group, the PCB materials innovator, manufacturer, supplier and one-stop shop for copper clad laminates, prepregs, as well as process consumables and PCB manufacturing equipment has established volume inventory of halogen-free FR4.1 and FR15.1 PCB materials at its European hub in Germany.