Making Better Batteries
May 31, 2018 | Imperial College LondonEstimated reading time: 3 minutes
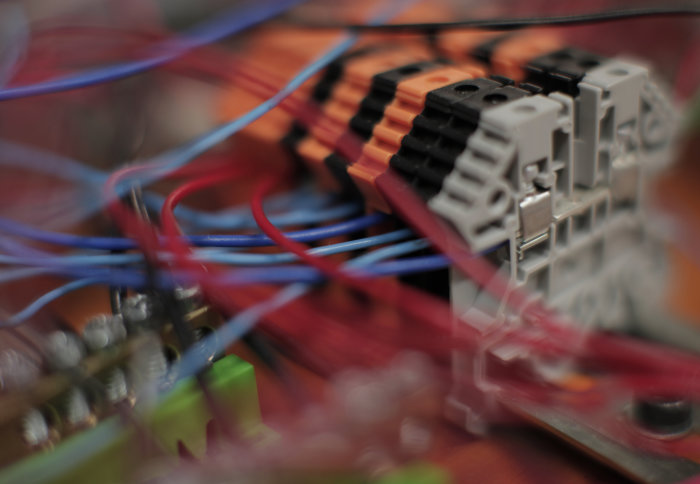
Research focused on upscaling of energy-storage devices was presented by Dr Billy Wu and Professor Jason Riley in an IMSE Lunchtime Seminar last week. The Institute for Molecular Science and Engineering (IMSE) co-ordinates a range of integrated activities to bring Imperial College London’s world class engineers, scientists, medics and business researchers together to collaborate on pressing global challenge problems.
The Lunchtime Seminar Series is a key part of these community-building endeavours. They provide the opportunity for Imperial staff and students to learn about different aspects of research projects that are ongoing in College, in a relaxed environment.
Renewable Revolution
The stone age came to an end, not because we had a lack of stones, and the oil age will come to an end not because we have a lack of oil. Sheikh Yamani Former Saudi Oil Minister
In the latest of these seminars, Dr Billy Wu (Dyson School of Design Engineering) and Professor Jason Riley (Department of Materials and Associate Director of IMSE) described some of their current research on the topic of upscaling energy-storage technologies.
These efforts are occurring within the modern ‘renewable revolution’, in particular the growing worldwide drive towards electric vehicles and the reduction of greenhouse gas emissions. For example, the UK government – as laid out in the Clean Growth Strategy – wants all new cars to be electric by 2030.
A Multidisciplinary, Multiscale Problem
Dr Wu began his talk by explaining how the overarching problem of trying to make better batteries is a multiscale and multidisciplinary problem. He and his colleagues work across the interface of fundamental science and application-based engineering so that they are equipped to tackle the challenge from a range of perspectives.
The aim is to eventually develop high-power, high-energy batteries at a competitive cost, and some of the most important factors to consider in this work include:
- the best chemistry (combination of materials) for a battery
- the availability and sustainability of necessary resources
- physical phenomena (i.e., how to best use the materials)
- how to scale-up laboratory-scale batteries to full-scale, usable cells for specific applications (e.g., electric cars)
Room for Improvement
"A key challenge for battery producers is the length of time it takes to develop a scientific breakthrough into a workable technology. This can take more than 10 years, with no return on investment in that time," said Dr Billy Wu Dyson School of Design Engineering.
Dr Wu’s group are currently working on a number of different ways to improve standard battery fabrication techniques. These conventional methods tend to involve many steps and have not really evolved in recent years. As such, there is plenty of room for optimisation.
In recently published work, led by Dr Xinhua Liu (Dyson School of Design Engineering), the method of ‘electrospinning’ was examined as a way to produce supercapacitor systems. Although the nanofiber structure devices exhibit high-power characteristics, the materials are inherently porous and thus have poor energy densities. In their current work, however, Dr Wu’s group is examining the possibility of coating electrospun carbon nanofibre frameworks with zinc materials to produce high-performance energy-storage devices.
The group is also investigating ways to improve the thermal management systems for battery cells. Such systems are an important – and expensive – part of full-scale cells. Their work will allow the degradation of cells, and their potential lifetimes, to be better understood.
Microstructure Control
How to store large amounts of renewably generated electricity is becoming a major issue for many countries around the world. Professor Jason Riley IMSE Associate Director
In the second half of the Lunchtime Seminar, Professor Riley described a number of studies in which his group have examined how the microstructure of battery and capacitor materials can influence the performance – particularly the energy storage capacity – of devices.
For example, Professor Riley spoke about work on zinc-based metal-organic frameworks (MOFs) and phosphorous-doped graphene oxide. By precisely tuning the chemistry and internal structure of these materials, their energy storage capacities and stabilities can be substantially improved.
Going forward, Professor Riley’s team hopes to apply their methodologies to a range of other material systems and to thus improve their suitability for energy -storage technologies.
Suggested Items
Indium Corporation Expert to Present on Automotive and Industrial Solder Bonding Solutions at Global Electronics Association Workshop
06/26/2025 | IndiumIndium Corporation Principal Engineer, Advanced Materials, Andy Mackie, Ph.D., MSc, will deliver a technical presentation on innovative solder bonding solutions for automotive and industrial applications at the Global Electronics A
Gorilla Circuits Elevates PCB Precision with Schmoll’s Optiflex II Alignment System
06/23/2025 | Schmoll MaschinenGorilla Circuits, a leading PCB manufacturer based in Silicon Valley, has enhanced its production capabilities with the addition of Schmoll Maschinen’s Optiflex II Post-Etch Punch system—bringing a new level of precision to multilayer board fabrication.
Day 1: Cutting Edge Insights at the EIPC Summer Conference
06/17/2025 | Pete Starkey, I-Connect007The European Institute for the PCB Community (EIPC) Summer Conference took place this year in Edinburgh, Scotland, June 3-4. This is the second of three articles on the conference. The other two cover the keynote speeches and Day 2 of the technical conference. Below is a recap of the first day’s sessions.
American Made Advocacy: Supporting the Entire PCB Ecosystem—Materials to OEMs
06/17/2025 | Shane Whiteside -- Column: American Made AdvocacyWith the addition of RTX to PCBAA’s membership roster, we now represent the interests of companies in the entire PCB ecosystem. From material providers to OEMs, the insights of our collective members help us educate, advocate, and support legislation and policy favorable to America’s microelectronics manufacturers. The industry veterans who lead these companies provide valuable perspective, and their accumulated wisdom makes us an even stronger association.
Ventec Strengthens Commitment to Halogen-Free PCB Manufacturing in Europe
06/11/2025 | Ventec International GroupVentec International Group, the PCB materials innovator, manufacturer, supplier and one-stop shop for copper clad laminates, prepregs, as well as process consumables and PCB manufacturing equipment has established volume inventory of halogen-free FR4.1 and FR15.1 PCB materials at its European hub in Germany.