Using Spin Current to Convert Mechanical Vibrations Into Electricity
July 20, 2018 | RIKENEstimated reading time: 2 minutes
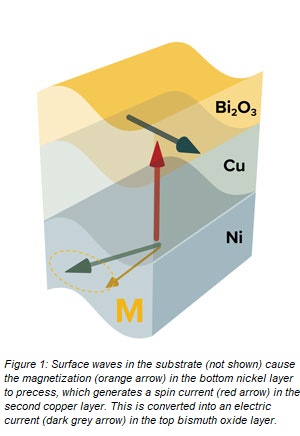
A nanoscale device that converts mechanical ripples into an electrical current via a ‘spin current’ has been made by RIKEN researchers1. Further development of this technology could see it used in devices that permit sound waves to pass in one direction but block them in the opposite direction.
Conventional electronic devices are based on shunting electrons around circuits. Because electrons possess charge, they give rise to electric currents when they move. The emerging field of spintronics, however, harnesses another property of electrons: their spin. Spin currents are the spintronic equivalent of electric currents, but unlike electric currents, they can flow without the electrons actually moving since spin can be transferred between stationary electrons.
As well as holding out the promise of resistance-free energy flow, electron spin can be used to convert between various forms of energy, including electricity, light, sound, vibrations and heat. This ability to switch between different energy forms will lead to a wide range of versatile devices.
Jorge Puebla at the RIKEN Center for Emergent Matter Science and Mingran Xu at the University of Tokyo and colleagues have made a three-layered nanodevice that converts mechanical vibrations into electric current. Waves generated on the surface of a substrate cause the magnetization of the bottom nickel layer of the device to sweep out arcs (Fig. 1). This periodic motion of the magnetization generates a spin current in the second copper layer. Finally, the spin current is converted into an electric current at the interface with the top bismuth oxide layer.
The team found that the spin current generated in the second layer was particularly large. “In our field, researchers are seeking to generate higher spin currents,” explains Xu. “Our method produces quite a huge spin current.”
“We’re approaching spin currents that are large enough to move magnetic domain walls, which could be used in memory devices,” adds Puebla. “We’re still below the spin currents needed, but believe we should be able to get close by optimizing our devices.”
Another advance was the use of a relatively new way to convert a spin current into an electrical one. Often expensive metals such as platinum are required for this conversion, but the method the team used worked with copper. “I think in terms of technology, people might find this approach cheaper to produce real devices,” comments Xu.
Since the output varied with direction, a potential application is audio devices that allow sound to flow in one direction but not the opposite one. “You could have headphones that allow you to listen to music and hear what others are saying, but other people cannot hear what you’re listening to,” says Puebla.
Suggested Items
The Evolution of Picosecond Laser Drilling
06/19/2025 | Marcy LaRont, PCB007 MagazineIs it hard to imagine a single laser pulse reduced not only from nanoseconds to picoseconds in its pulse duration, but even to femtoseconds? Well, buckle up because it seems we are there. In this interview, Dr. Stefan Rung, technical director of laser machines at Schmoll Maschinen GmbH, traces the technology trajectory of the laser drill from the CO2 laser to cutting-edge picosecond and hybrid laser drilling systems, highlighting the benefits and limitations of each method, and demonstrating how laser innovations are shaping the future of PCB fabrication.
Day 2: More Cutting-edge Insights at the EIPC Summer Conference
06/18/2025 | Pete Starkey, I-Connect007The European Institute for the PCB Community (EIPC) summer conference took place this year in Edinburgh, Scotland, June 3-4. This is the third of three articles on the conference. The other two cover Day 1’s sessions and the opening keynote speech. Below is a recap of the second day’s sessions.
Day 1: Cutting Edge Insights at the EIPC Summer Conference
06/17/2025 | Pete Starkey, I-Connect007The European Institute for the PCB Community (EIPC) Summer Conference took place this year in Edinburgh, Scotland, June 3-4. This is the second of three articles on the conference. The other two cover the keynote speeches and Day 2 of the technical conference. Below is a recap of the first day’s sessions.
Preventing Surface Prep Defects and Ensuring Reliability
06/10/2025 | Marcy LaRont, PCB007 MagazineIn printed circuit board (PCB) fabrication, surface preparation is a critical process that ensures strong adhesion, reliable plating, and long-term product performance. Without proper surface treatment, manufacturers may encounter defects such as delamination, poor solder mask adhesion, and plating failures. This article examines key surface preparation techniques, common defects resulting from improper processes, and real-world case studies that illustrate best practices.
RF PCB Design Tips and Tricks
05/08/2025 | Cherie Litson, EPTAC MIT CID/CID+There are many great books, videos, and information online about designing PCBs for RF circuits. A few of my favorite RF sources are Hans Rosenberg, Stephen Chavez, and Rick Hartley, but there are many more. These PCB design engineers have a very good perspective on what it takes to take an RF design from schematic concept to PCB layout.