Flex Circuit Assembly: Challenges and Strategies for Success
July 27, 2018 | Stephen Las Marias, I-Connect007Estimated reading time: 7 minutes
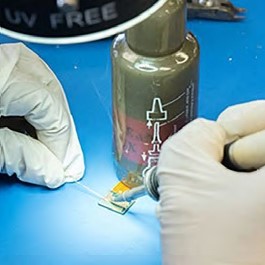
The continuing trend towards miniaturization and the increasing functionality in smaller and smaller devices are the primary drivers for the growth of the flexible printed circuit market. Everything is getting smaller, faster, and more complex. The segments that have consistently driven it are more on the consumer side, such as mobile phones and smart electronics. On the industrial side, contributing markets include medical—portable medical electronics, diagnostic electronics—and military/defense.
Of course, dealing with flex circuits during assembly is very different from rigid PCBs. And among the key challenges here are the material itself, and the word 'flexible,' according to David Moody, director of sales and marketing at Lenthor Engineering: "Flexible circuits are flexible; they aren’t flat, they aren’t rigid, and they conform to a shape. The other portion of it is the three-dimensionality of a flex circuit; you’re trying to do circuit mount assembly with small components, BGAs, and working on substrates’ flex circuits that often have different plane levels. There are higher portions on the circuit, so evening things out is really the challenge to getting the nice, flat, secure surface to mount the components on."
Lenthor has been in the flex and rigid-flex fabrication business for 35 years. It brought in-house flex and rigid-flex assembly 10 years ago as a value-add for its customers. Moody notes that it had been difficult for them and their customers at the time to find people in the assembly business that had a proficiency in flex circuit assembly, because there are some peculiarities regarding flex circuitry that you don’t find in rigid board assembly. "Being able to bring that in-house, we’ve been able to advance that portion of our offering to the customers."
Dealing with flex circuit assembly, Lenthor does a good mixture of hand assembly and automated assembly. "Flex circuits themselves generally have a combination of some hand assembly, and automated, surface-mount line, reflow, and pick and place," explains Moody. "Rigid-flex design typically replicates rigid-board assembly, because most of the functionality on a rigid-flex board is all centered in the rigid area. The flex area of a rigid-flex is usually the interconnect between the flex areas. So, it becomes a little less problematic; but flex circuits themselves do lend themselves far more to the multiple process environment."
Lenthor found flex circuit assembly challenging initially. “Luckily for us, we hired a really good engineer who’s been able to design a lot of the fixturing that we use, and that’s what really makes us succeed in assembly,” says Moody. “In the beginning it was difficult, there was far more rework than we have today. But the techniques, the equipment that we’ve got now, have really lent themselves to an assembly that’s predictable. We get a very good first yield rate. I would guess it’s 96-97% in the first pass yield. It wasn’t that way 10 years ago.”
Indeed, when dealing with flex circuits, the overarching theme to ensure successful assembly is proper fixturing.
According to Bob Wettermann, principal of BEST Inc., an electronics rework/repair and PCB assembly firm, "In the rigid world, you have a coplanar surface and components with known fixed dimensions, and so the pick and place machine knows exactly how and where to place the device. It’s always a planar surface. Now, you add the three dimensionality as well as the lack of rigidity of the surface and it becomes very difficult to place micro components on essentially a noodle."
"Fixturing is key to tackling this problem. Having a good coplanar surface to remove and replace devices is key to reworking complex devices on flex circuitry. In terms of physical repair, such as IPC-7721-related type of physical repairs, there just aren’t any standards for flex materials. You have to make the process up as you go along. The other day, a client sent us a case where we were refereeing the acceptability criteria for the solder joints of an SOIC placed onto a flex circuit. We were dealing with an epoxy attachment to flex. And guess what? There are no industry acceptability criteria. So, it’s still a little bit of the Wild West, I would call it, in terms of standards, knowledge and practices. You make it up as you go along."
Throw it Over the Wall
In our conversations with industry experts, they always mention a critical factor to success when it comes to design, fabrication, or assembly—communication along the supply chain. Because most often than not, the industry continues to have a 'throw it over the wall' mentality.
This case is no different. "It's just because of the kind of business that we are in in terms of assembly—we're the prototyping guys, so our job is to get the customer functional units so they can go to round two or round three," says Wettermann. "Generally, the boards are not ending up in end customers' hands. Our job is to get functional units."
Moody echoes what Wettermann is saying. "In the prototype stage, a lot of customers are just simply looking to get some functionality out of the initial product, and they just want you to go figure it out. On the other hand, because we do get into some production stuff with our customers, and it’s still interesting to me that when we begin the conversation, and we begin in sometimes even at the design stage, the assembly aspect of the build is still not being considered until it’s almost necessary. No matter how much you try to drive the conversation in the beginning, I don’t know why, but there is still some reluctance to concentrate on what the assembly is going to has to be done before assembly."
Page 1 of 2
Testimonial
"The I-Connect007 team is outstanding—kind, responsive, and a true marketing partner. Their design team created fresh, eye-catching ads, and their editorial support polished our content to let our brand shine. Thank you all! "
Sweeney Ng - CEE PCBSuggested Items
Indium Corporation Promotes Two Leaders in EMEA (Europe, Middle East, and Africa) Markets
08/05/2025 | Indium CorporationWith its commitment to innovation and growth through employee development, Indium Corporation today announced the promotions of Andy Seager to Associate Director, Continental Sales (EMEA), and Karthik Vijay to Senior Technical Manager (EMEA). These advancements reflect their contributions to the company’s continued innovative efforts with customers across Europe, the Middle East, and Africa (EMEA).
MacDermid Alpha Electronics Solutions Unveils Unified Global Website to Deepen Customer, Talent, and Stakeholder Engagement
07/31/2025 | MacDermid Alpha Electronics SolutionsMacDermid Alpha Electronics Solutions, the electronics business of Elements Solutions Inc, today launched macdermidalpha.com - a unified global website built to deepen digital engagement. The launch marks a significant milestone in the business’ ongoing commitment to delivering more meaningful, interactive, and impactful experiences for its customers, talent, and stakeholders worldwide.
KOKI to Showcase Analytical Services and New HF1200 Solder Paste at SMTA Guadalajara 2025
07/31/2025 | KOKIKOKI, a global leader in advanced soldering materials and process optimization services, will exhibit at the SMTA Guadalajara Expo & Tech Forum, taking place September 17 & 18, 2025 at Expo Guadalajara, Salón Jalisco Halls D & E in Guadalajara, Mexico.
Weller Tools Supports Future Talent with Exclusive Donation to SMTA Michigan Student Soldering Competition
07/23/2025 | Weller ToolsWeller Tools, the industry leader in hand soldering solutions, is proud to announce its support of the upcoming SMTA Michigan Expo & Tech Forum by donating a limited-edition 80th Anniversary Black Soldering Set to the event’s student soldering competition.
Koh Young Appoints Tom Hattori as President of Koh Young Japan
07/21/2025 | Koh YoungKoh Young Technology, the global leader in True 3D measurement-based inspection solutions, announced the appointment of Tom Hattori as President of Koh Young Japan (JKY).