-
- News
- Books
Featured Books
- pcb007 Magazine
Latest Issues
Current IssueInventing the Future with SEL
Two years after launching its state-of-the-art PCB facility, SEL shares lessons in vision, execution, and innovation, plus insights from industry icons and technology leaders shaping the future of PCB fabrication.
Sales: From Pitch to PO
From the first cold call to finally receiving that first purchase order, the July PCB007 Magazine breaks down some critical parts of the sales stack. To up your sales game, read on!
The Hole Truth: Via Integrity in an HDI World
From the drilled hole to registration across multiple sequential lamination cycles, to the quality of your copper plating, via reliability in an HDI world is becoming an ever-greater challenge. This month we look at “The Hole Truth,” from creating the “perfect” via to how you can assure via quality and reliability, the first time, every time.
- Articles
- Columns
- Links
- Media kit
||| MENU - pcb007 Magazine
Estimated reading time: 3 minutes
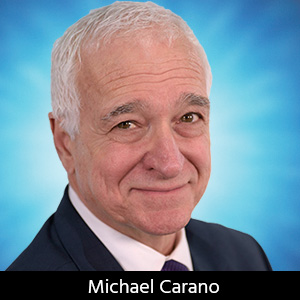
Contact Columnist Form
Trouble in Your Tank: PTH Failure Mechanisms and Using IST as a Tool, Part 1
Introduction
Getting to the root cause of a defect is not a simple task. As stated numerous times in these columns over the last several years, a defect may have its genesis in a process or processes several steps removed from the operation where the defect manifests itself. This edition of “Trouble in Your Tank” will elucidate the difficulty of root cause defect analysis when incorrect assumptions (and thus conclusions) are made. Further, I will illustrate that when proper tools are used to study the issue, additional data is gathered that supports the actual cause of the defect.
The Issue
In this instance, a fabricator was in the process of evaluating a different electroless copper process. While the initial start-up and subsequent production was satisfactory, there was a defect noted after several weeks of operation. At first, in-circuit test (ICT) found an open. Crosssectioning revealed a fracture in the electroplated copper after solder float. The fabricator then decided to perform additional testing using interconnection stress test (IST) from PWB Interconnect Solutions. The internal brainstorming team strongly felt this issue must be related to the electroless copper process. Yet there was no concrete evidence to support this theory.
What follows is a systematic procedure to get to the root cause of the problem. But first, a bit of background on IST.
IST Testing and Mechanism
IST has been a standard failure analysis method in the industry for over two decades. IST is a tool that provides insight into PWB failure mechanisms and allows fabricators and chemistry/material suppliers to make improvements in the fabrication process to enhance long-term reliability. These improvements are not exclusive to process and materials as design of the PWB may also contribute to failure.
IST has both the capability of effectively and rapidly quantifying the integrity of the plated through-hole (PTH) and the unique ability to identify the presence and levels of post separation within the multilayer board (MLB)[1]. A typical IST coupon has two circuits typically designed into the coupon: a power circuit for direct heating through the interconnect and a sensing circuit to measure stress and strain in the barrel of the PTH.
This test method measures cycles to failure on these specially designed IST coupons that are thermally cycled using current flow through internally heated circuits that heat the coupon and the adjacent plated-through holes. Failure is defined as a 10% increase in the resistance of the PTH[2].
In short, there are any number of factors that can precipitate the failure of either the electroless copper-to-post interconnect, or the failure of the electroplated copper in the via itself. In terms of failure in the plated-through hole or the post interconnect, thermal excursions are the major cause of failures. Figure 1 depicts a schematic of key defects in the plated throughhole that are thermally induced.
The primary cause of barrel cracking is the CTE mismatch between the resin matrix and the electrodeposited copper. This is taking place in the Z-axis. Movement in the X-Y plane is somewhat more restricted than in the Z-axis due to the glass fiber reinforcement. In addition, the resin CTE increases sharply above its glass transition temperature, causing further CTE mismatch strain induction on the copper and the potential for PTH/PTV failure.
With all this information, where does the fabricator go from here? Certainly, using higher Tg, lower CTE materials would be a benefit for improved reliability. But at what added material cost? In addition, a change in material will certainly impact other aspects of the board including electrical functionality that may not be acceptable to the end user.
Interconnect defects (ICD)—that is, the separation of the plated copper (either electroless or electrolytic) from the post innerlayer—is a different failure mechanism than described above. The good news is that IST testing can differentiate between barrel cracking failures and ICD failures. The bad news is these are both failures. However, understanding what the actual failure is will help guide the troubleshooter to get to the root cause of the defect. So, assuming the material set is as is and the board construction is as is, let’s first describe the defect and work through the troubleshooting process.
To read the full version of this article which originally appeared in the June 2018 issue of PCB007 Magazine, click here.
More Columns from Trouble in Your Tank
Trouble in Your Tank: Metallizing Flexible Circuit Materials—Mitigating Deposit StressTrouble in Your Tank: Can You Drill the Perfect Hole?
Trouble in Your Tank: Yield Improvement and Reliability
Trouble in Your Tank: Causes of Plating Voids, Pre-electroless Copper
Trouble in Your Tank: Organic Addition Agents in Electrolytic Copper Plating
Trouble in Your Tank: Interconnect Defect—The Three Degrees of Separation
Trouble in Your Tank: Things You Can Do for Better Wet Process Control
Trouble in Your Tank: Processes to Support IC Substrates and Advanced Packaging, Part 5