-
- News
- Books
Featured Books
- pcb007 Magazine
Latest Issues
Current IssueInventing the Future with SEL
Two years after launching its state-of-the-art PCB facility, SEL shares lessons in vision, execution, and innovation, plus insights from industry icons and technology leaders shaping the future of PCB fabrication.
Sales: From Pitch to PO
From the first cold call to finally receiving that first purchase order, the July PCB007 Magazine breaks down some critical parts of the sales stack. To up your sales game, read on!
The Hole Truth: Via Integrity in an HDI World
From the drilled hole to registration across multiple sequential lamination cycles, to the quality of your copper plating, via reliability in an HDI world is becoming an ever-greater challenge. This month we look at “The Hole Truth,” from creating the “perfect” via to how you can assure via quality and reliability, the first time, every time.
- Articles
- Columns
- Links
- Media kit
||| MENU - pcb007 Magazine
Estimated reading time: 4 minutes
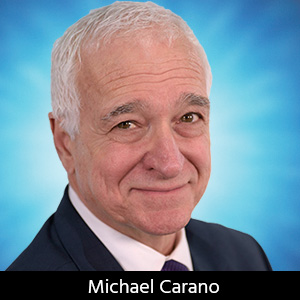
Contact Columnist Form
Trouble in Your Tank: Flexible Metalization, Part II
In previous columns and elsewhere in literature, concerns about electroless copper peeling from polyimide material have been reported. The main concern with is the creation of a void caused by peeling or blistering (Figure 1).
It is hypothesized that the blisters originate from one of, or a combination of, the potential causes listed below:
- Excessive catalyst adsorption causing a hyperdeposition of electroless copper
- Highly stressed electroless copper deposit
- Plasma residues causing poor bondability of electroless copper
- Overactive resin surface due to plasma
- Lack of surface profilometry due to plasma
Often, fabricators resort to double passing the circuits through the electroless copper process with the hope that the second pass will cover the void and prevent further blistering. Just remember, “Hope is not a strategy.”
It is recognized that plasma desmear leaves the surface in somewhat of an inert state. It is important that the fabricator work very closely with the plasma supplier to ensure an optimized process. It is also critical that residues from the plasma desmear process be removed prior to electroless copper plating.
As is often the case, adhesive-based flexible circuit constructions present another challenge related to achieving void-free metalization. Due to the difficulty in plating flexible materials (particularly when plasma-treated only), one would think that alkaline permanganate treatment could be used to enhance the plating of a void-free deposit. Unfortunately, using a full permanganate cycle can have disastrous consequences (Figure 2).
The suggestion is if one has voiding issues with certain flexible or rigid-flex builds, use a modified permanganate cycle after plasma.
In this case, modified means to skip the solvent-sweller step (either NMP or butyl/caustic-based) and only immerse the parts in the permanganate solution, followed by the neutralization step.
Another critical success factor relates to the operational and chemical conditions within the electroless copper deposition process. These key aspects will now be presented in some detail. Much of what is detailed below are the results of many DOEs. These experiments yielded several important pieces of information.
After several DOEs and other tests, the best condition for eliminating the peeling electroless is to implement what is known as a low deposition rate electroless copper process. The definition of low deposition is a process that deposits 1.0 to 1.5 µin of copper per minute of dwell time in the electroless copper solution. This is achieved by making several modifications to the current process. First, the electroless copper plating solution should be reduced in temperature to 80−90°F with a deposition time of 20 minutes. The target deposit thickness is 20−25 µin in 20 minutes.
To further slow the deposition rate of the bath, the amount of palladium-based catalyst deposited on the dielectric materials must be reduced. This is accomplished by reducing the cleaner/conditioner as well as catalyst concentrations. Of course, it helps if the cleaner/conditioner chemistry is designed to reduce the thickness of the catalyst layer as it is adsorbed onto the polyimide material. Reducing the catalyst layer thickness, and in turn the amount of palladium on the material, improves adhesion and reduces the tendency of the electroless copper to blister from the substrate.
Polyimide Materials
It is a good idea to review the chemistry involved in polyimide flex materials. Polyimide materials are a condensation reaction of a dianhydride and a diamine compound in a dipolar aprotic solvent, such as DMF and DMAc. Poly(amic acid) is converted to the final polyimide product by thermal imidization. Figure 2 details the reaction showing the synthesis of polyimide. Polyimide has exceptional solvent resistance, high thermal stability, and good dielectric properties.
One of the critical aspects of plating is the ability to activate the substrate to be plated.
Amides, such as polyimide, are one such material. Amides and imides are the least reactive of the carboxylic acid derivatives. However, they are attacked by strong base and acid (heat). Base hydrolysis of an amide is shown in Figure 3 using 1M KOH at 80°C for 20 minutes, followed by 0.2N HCl at RT for five minutes.
It is highly recommended that this type of procedure be implemented when attempting to metalize polyimide. This is referred to as a preconditioning step.
Successful metalization of flex and rigid-flex board structures is challenging. However, if one understands the limitations of the wet processes (never assume you can apply FR-4 processing here), a void-free continuous adherent copper deposit is achievable.
A few additional caveats:
- Not all electroless copper processes perform equally
- Plasma leaves the surface in an inert state, which is not easy to obtain adhesion and coverage
- Pay attention to the pre-plating parameters and tighten the operating window as needed
- Flex and rigid-flex is “not your father’s FR-4” anymore
Michael Carano is VP of technology and business development for RBP Chemical Technology. To reach Carano, or read past columns, click here.
This article originally appeared in the July 2018 issue of PCB007 Magazine, click here.
More Columns from Trouble in Your Tank
Trouble in Your Tank: Metallizing Flexible Circuit Materials—Mitigating Deposit StressTrouble in Your Tank: Can You Drill the Perfect Hole?
Trouble in Your Tank: Yield Improvement and Reliability
Trouble in Your Tank: Causes of Plating Voids, Pre-electroless Copper
Trouble in Your Tank: Organic Addition Agents in Electrolytic Copper Plating
Trouble in Your Tank: Interconnect Defect—The Three Degrees of Separation
Trouble in Your Tank: Things You Can Do for Better Wet Process Control
Trouble in Your Tank: Processes to Support IC Substrates and Advanced Packaging, Part 5