-
- News
- Books
Featured Books
- pcb007 Magazine
Latest Issues
Current IssueInventing the Future with SEL
Two years after launching its state-of-the-art PCB facility, SEL shares lessons in vision, execution, and innovation, plus insights from industry icons and technology leaders shaping the future of PCB fabrication.
Sales: From Pitch to PO
From the first cold call to finally receiving that first purchase order, the July PCB007 Magazine breaks down some critical parts of the sales stack. To up your sales game, read on!
The Hole Truth: Via Integrity in an HDI World
From the drilled hole to registration across multiple sequential lamination cycles, to the quality of your copper plating, via reliability in an HDI world is becoming an ever-greater challenge. This month we look at “The Hole Truth,” from creating the “perfect” via to how you can assure via quality and reliability, the first time, every time.
- Articles
- Columns
- Links
- Media kit
||| MENU - pcb007 Magazine
Estimated reading time: 3 minutes
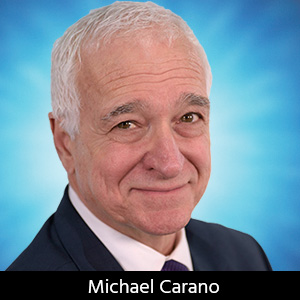
Contact Columnist Form
Trouble in Your Tank: A Tale of Zinc Tails
Introduction
Copper foil used in the fabrication of printed circuit boards is subjected to a plurality of copper layer treatments, including a roughening treatment followed by a locking or gilding treatment to form a matte surface on the copper foil. The matte surface is then coated with a thin layer of zinc and heated to produce a brass layer that provides the copper foil with sufficient bonding sites to enhance the interlaminar bond strength between the resin and the copper foil. This brings me to a tale—a zinc “tail”—but what exactly is a zinc tail?
Origin of the Zinc Tail
An electrodeposited copper foil to be laminated on a substrate for a PCB is treated with either a brass or zinc coating. This barrier layer serves several purposes, including improving the adhesion of the foil to the laminate resin materials and acting as a diffusion barrier. How does this play into the creation of the zinc tail? The mechanism, while not well understood, is believed to have its origins after the use of plasma for desmear/etchback. In particular, the zinc tail is prominently visible if plasma provides a three-point connection (Figure 1).
Figure 1: Zinc tail at C-stage to copper interface.
In Figure 1, the protruding foil treatment (tail) extends from the foil into the electrolytic copper. Several fabricators have documented this condition and the subsequent degradation of PTH reliability after thermal excursions. It is easy to see why the zinc tail left unremoved would act as a fulcrum causing weakening in the plated through-hole (PTH). Another issue is that the tail may be misinterpreted as poor adhesion of the electroless copper deposit.
Figure 2: SEM/EDAX results of protruding area and foil treatment shown in Figure 1.
Figure 2 shows the results of the SEM/EDAX of the protruding tail. One can easily see the high level of zinc present.
Figure 3: Zinc tail evident on C-stage.
Figure 3 shows another example of the zinc tail as it protrudes into the via. Subsequent metalization is forced to plate around the tail.
Zinc Tail as a Possible Cause of PTH Failures
Thermal cycling leads to the majority of failures in the plated through-hole. It is also critical to put in perspective the environment in which the circuit board will be used. A harshuse environment (HUE), such as automotive applications under the hood or on an engine, qualifies as the most severe of environments. Reliability testing should simulate the thermal excursions of a PTH throughout its life. This would include thermal cycling at temperature extremes of -40°C to +125°C. In addition, the most severe thermal cycles are experienced during assembly and rework. Thus, simulating assembly reflow and rework cycles will provide a more in-depth understanding of the board’s long-term reliability. More to come on this topic in a future column.
As previously mentioned, the concern is that the protruding zinc tail, if not removed prior to metalization, will lead to stress points within the electrodeposited copper at a minimum. If one clearly studies the failure hierarchy within the PTH, one surmises that the plated-through via expands quite rapidly in the Z-axis at a temperature above the Tg of the resin material. During these temperature excursions, the PTH acts as a rivet working to resist expansion. However, when there are various anomalies in the PTH, including protruding glass fiber bundles and zinc tails, stress points are introduced. Remember, the weakest link in the chain breaks first. If the chain’s weakest link is thin-plated or brittle copper, then one can expect the failure to occur at this point. Keep in mind that the number of thermal cycles to failures is affected by the strain imposed on the PTH during each cycle. Thus, the concern with additional strain created by the protruding zinc tail.
Regardless, it is a given that the zinc tail can have a negative impact on PTH thermal reliability. Therefore, it is best to understand how to minimize its formation, or at least provide a means to mitigate the negative effects of the zinc tail.
One way to remove zinc is to be somewhat aggressive with the microetch prior to electroless copper plating. Strong acids, such as hydrochloric acid, will also remove the zinc without etching the copper interconnects. I recommend that if zinc tails become an issue, testing of acid soak cleaners, such as hydrochloric acid-based and persulphate-based microetchants, be evaluated.
Michael Carano is VP of technology and business development for RBP Chemical Technology.
This article originally appeared in the August 2018 issue of PCB007 Magazine, click here.
More Columns from Trouble in Your Tank
Trouble in Your Tank: Metallizing Flexible Circuit Materials—Mitigating Deposit StressTrouble in Your Tank: Can You Drill the Perfect Hole?
Trouble in Your Tank: Yield Improvement and Reliability
Trouble in Your Tank: Causes of Plating Voids, Pre-electroless Copper
Trouble in Your Tank: Organic Addition Agents in Electrolytic Copper Plating
Trouble in Your Tank: Interconnect Defect—The Three Degrees of Separation
Trouble in Your Tank: Things You Can Do for Better Wet Process Control
Trouble in Your Tank: Processes to Support IC Substrates and Advanced Packaging, Part 5