-
- News
- Books
Featured Books
- pcb007 Magazine
Latest Issues
Current IssueInventing the Future with SEL
Two years after launching its state-of-the-art PCB facility, SEL shares lessons in vision, execution, and innovation, plus insights from industry icons and technology leaders shaping the future of PCB fabrication.
Sales: From Pitch to PO
From the first cold call to finally receiving that first purchase order, the July PCB007 Magazine breaks down some critical parts of the sales stack. To up your sales game, read on!
The Hole Truth: Via Integrity in an HDI World
From the drilled hole to registration across multiple sequential lamination cycles, to the quality of your copper plating, via reliability in an HDI world is becoming an ever-greater challenge. This month we look at “The Hole Truth,” from creating the “perfect” via to how you can assure via quality and reliability, the first time, every time.
- Articles
- Columns
- Links
- Media kit
||| MENU - pcb007 Magazine
Estimated reading time: 5 minutes
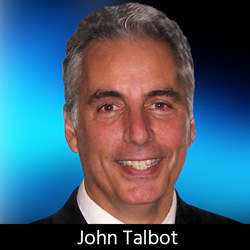
Acrylic vs. Epoxy Adhesives for Flexible Circuits
Two of the most common applications for flexible circuits are static and dynamic. A static scenario is one where the flexible circuit is put into place, even if it has to flex to get there, and then remains static throughout the lifetime of the product. A dynamic application is one where the flexible circuit is in motion during the lifetime of the product. Think of a flip phone, a printer, or an MRI machine. A flexible circuit used in a static operation can be thought of as a derivative of the traditional PCB, albeit lighter and more malleable. However, in a dynamic application the circuit must be, not only flexible, but robustly so. We must be able to exploit all of the inherent advantages of the materials to their fullest extent. In either of these cases the adhesive plays an important role. Let’s review another factor that affects the choice of adhesive.
The environment where the product will reside during the majority of its life-cycle also enters into the adhesive choice. Will the environment be excessively hot or cold? Will the circuit be immersed in water or chemicals? Does the circuit need to be flame retardant or not? These are all questions that may make a difference in the adhesive system chosen for the circuit. For instance, if the circuit will or can be immersed in water, we’ll want to choose an adhesive system that is the least absorptive. If the circuit will be used in an application that will see it covered in chemicals or biological fluids, we’ll want the most chemical-resistant system. If the circuit will see higher than ambient temperatures, we’ll want an adhesive that performs well at those temperatures without any degradation of the lamination. Does the circuit need to per-form to UL94 V.0? That is, must the circuit be flame retardant as in automotive or aerospace applications? All of these concerns must be addressed when choosing the adhesive system for your flexible circuit.
Surprisingly, the design of the circuit matters as well when choosing an adhesive system. If the circuit will be single-sided (one layer of copper) or double-sided (two layers of copper), then either adhesive system will perform equally well, all other criteria being equal. However, if the design will be a multi-layered circuit, then the characteristics of the adhesive have a significant effect. Small plated through-holes less than 8 mils in diameter may also have an effect on the performance of the circuit if the wrong adhesive is chosen.
As you can see, there is a lot to consider when deciding on an adhesive-based system for your flexible circuit. Now, let’s discuss some of the properties for both types of systems and see how they relate to the discussion above.
Acrylic adhesive is the best choice for dynamic applications because it stays malleable after it is cured. That is its most valuable characteristic. That is, unless, it must be flame retardant. In order for acrylic adhesive to com-ply with UL94 V.0, brominated flame retardants must be added which reduces the reliability for dynamic flexing. It reduces the thermal stability as well. Acrylics do not perform well at higher temperatures either. The material starts to soften in the 180–200°C range, which can cause delamination of the insulating layers as well as the copper traces. Acrylic doesn’t per-form well for wire bond designs either. The softer adhesive tends to absorb the ultrasonic wire bonding energy causing difficulties in the assembly process. And finally, it has a higher coefficient of expansion. This causes movement in the Z-axis which means that it is not a good choice for multilayer circuits because of the damage that could be done to plated through-holes.
Epoxy adhesive, on the other hand, is not a good choice for dynamic operations because it cures hard. However, that makes it a better choice for a lot of other applications. For instance, it has the best bond strength at high temperatures and has a low coefficient of expansion, making it a great choice for multi-layer designs and circuits that will reside in higher temperatures. It is also very good for wire bond designs because it cures hard and doesn’t absorb the ultrasonic energy the way acrylic adhesives do. Epoxy-based adhesives have great chemical resistance and better mois-ture absorption rates making it a good choice for medical applications and moisture sensors of all kinds.
In the case of a multilayer rigid-flex hybrid circuit, both adhesives may be used in the same circuit. For instance, the flexible portion of the circuit may use acrylic adhesive for flexibility and the multilayer rigid section may use epoxy adhesive because of its increased stability.
Clearly, both types of adhesive systems have their ideal uses. Both are reliable and perform well as long as the applications they’re used in are considered carefully. Both adhesives are used frequently to manufacture flexible circuits. Some designers insist on acrylic adhesives because the first vendor they worked with called it out on their design.
However, it’s prudent to consider the application and the specifications seriously before you decide on an adhesive system for your flexible circuit application. There are times when either system will work equally well and times when the decision means the difference between a robust circuit or one that performs poorly without an obvious cause. Consider this the next time you design a flex-ible circuit.
More Columns from Consider This
Consider This: Designing Via-in-Pad for Higher Density Flexible CircuitsConsider This: Termination of Flex Circuits
Consider This: Reaching the Limit on Stiffeners
Consider This: PCB Technologies We Need Now and Later
Consider This: Advancements in Printed Circuit Manufacturing Equipment
Consider This: Heavy-Copper Flex Circuits See Large Growth
Consider This: Buried Capacitance Power Planes
Consider This: Let’s Talk About the Basics of Flex