-
- News
- Books
Featured Books
- pcb007 Magazine
Latest Issues
Current IssueInventing the Future with SEL
Two years after launching its state-of-the-art PCB facility, SEL shares lessons in vision, execution, and innovation, plus insights from industry icons and technology leaders shaping the future of PCB fabrication.
Sales: From Pitch to PO
From the first cold call to finally receiving that first purchase order, the July PCB007 Magazine breaks down some critical parts of the sales stack. To up your sales game, read on!
The Hole Truth: Via Integrity in an HDI World
From the drilled hole to registration across multiple sequential lamination cycles, to the quality of your copper plating, via reliability in an HDI world is becoming an ever-greater challenge. This month we look at “The Hole Truth,” from creating the “perfect” via to how you can assure via quality and reliability, the first time, every time.
- Articles
- Columns
- Links
- Media kit
||| MENU - pcb007 Magazine
Estimated reading time: 4 minutes
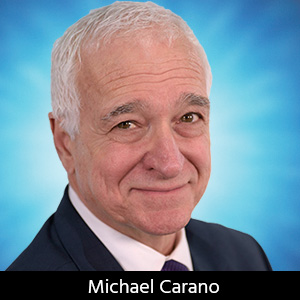
Contact Columnist Form
The Art and Science of Photoresist Stripping, Part 1
In the world of chemical processes, the action of the chemistry to bring about the desired result is often a blend of both art and science. The two mesh together quite easily. The job of the chemical supplier is to ensure that sound science is behind the formulation and designed for the job at hand. Remember, the PWB fabricator hires a product or process to perform a certain job, but it is not that simple. Photoresist stripping has become a complicated process due to many unique resist formulations on the market. The expectation is that many new concoctions will be introduced over the next few years. What happens chemically during the stripping process depends on a myriad of factors. Some of these factors are easy to understand, while others seemingly resemble alchemy.
Problems and Solutions
Stripping problems usually result from two performance deficiencies: failure of the anti-tarnish system and/or wide variance of stripping speed and quality with use of the stripper.
Figure 1: Stripping behavior of a MEA/choline-based resist stripper over time.
Most photoresist strippers give adequate anti-tarnish performance when the stripper is fresh but at some time during the life of the stripper, the panels start coming out tarnished. This is frequently thought to be the result of the anti-tarnish chemistry being consumed, which is not the case. The real reason this occurs is that dissolved copper in the stripper is a catalyst that accelerates the tarnishing of the copper metal substrate. As the stripper is used, the dissolved copper content builds and the stripper becomes increasingly corrosive to the exposed copper metal substrate. This is a good reason to not use high pH resist stripper formulations with concerns such as the oxidation or tarnishing of the copper. Some fabricators continue to employ low-cost, highly concentrated caustic-based strippers, but they are mistaken because this approach is not actually low cost (more on this later).
Thus, in reality, the tarnishing of panels in a used stripper is a failure of the anti-tarnish chemistry to deal with the increased corrosivity of the copper-contaminated stripper. This unfortunate situation can be avoided by selecting a stripper with anti-tarnish chemistry robust enough to overcome the corrosivity of high levels of dissolved copper. This choice can result in saving a tidy sum of money on stripper chemistry. The stripper can then be used to its real capacity rather than being prematurely dumped because it is tarnishing the copper. This is the more obvious problem.
A second issue relates to the dramatic decrease in speed of stripping with usage of the stripping chemistry. This results in an increase in resist stripping cost. Costs can come in several forms: lost productivity, potential for rejects due to resist residues remaining on the surface, adding fresh resist stripper to the working solution, and inadequate removal of resist skins from the sump. The addition of fresh stripper is usually a losing proposition depending on the stripper formulation and other factors. Other factors include the amount of stripped resist film in the sump, the reactivity of the exposed resist with the stripper ingredients, and whether or not the resist film is breaking up into particles/skins or is partially dissolving.
Figure 1 shows the relative behavior of a monoethanolamine (MEA)/choline-based resist stripper. These two chemicals are found in many of the commercially available resist strippers on the market today. Please note that in Figure 1, while representing a typical resist stripper operation, there are subtle differences from one resist to another. However, the general shape of the curve is representative.
Notice that the speed over the first 30% of the stripper bath is very high and almost completely uniform. As the choline depletes, the stripper starts stripping with the MEA. Consequently, the speed drops suddenly and dramatically and is uniform through its life. At this point, the stripper is acting as if it were a pure MEA-based product and choline was never present. For an outer layer stripper formulation, it makes sense to not have an MEA/choline-based mixture. Perhaps the choline with the potential for a solvent assist is a more cost-effective process for photoresist stripping of outer layers.
Figure 2: Chart showing pH as monitoring tool for MES/choline-based resist stripper.
Meanwhile, what is the best way to control the performance of the resist stripper? Notice in Figure 2 that the stripper containing choline starts at a pH over 13. When the pH drops to 11.5, no choline remains, so all remaining stripping occurs with only the MEA. This is a handy way to control this stripping chemistry and a much better approach than the traditional titration, which does not address quality or strength of amine present and only looks at the overall quantity of alkalinity present.
Figure 2 shows that controlling this type of chemistry by monitoring the pH, not by titration, is the best way to ensure the quality of stripping. This process is set up to run the line until the minimum acceptable quality of stripping is observed, followed by checking the pH. This pH becomes the minimum measurement at which the bath gives acceptable results. As one can see, photoresist stripping is a blend of art and science. However, in the end, it is about science. More details about resist stripping to come in a future column.
More Columns from Trouble in Your Tank
Trouble in Your Tank: Metallizing Flexible Circuit Materials—Mitigating Deposit StressTrouble in Your Tank: Can You Drill the Perfect Hole?
Trouble in Your Tank: Yield Improvement and Reliability
Trouble in Your Tank: Causes of Plating Voids, Pre-electroless Copper
Trouble in Your Tank: Organic Addition Agents in Electrolytic Copper Plating
Trouble in Your Tank: Interconnect Defect—The Three Degrees of Separation
Trouble in Your Tank: Things You Can Do for Better Wet Process Control
Trouble in Your Tank: Processes to Support IC Substrates and Advanced Packaging, Part 5