-
- News
- Books
Featured Books
- pcb007 Magazine
Latest Issues
Current IssueInventing the Future with SEL
Two years after launching its state-of-the-art PCB facility, SEL shares lessons in vision, execution, and innovation, plus insights from industry icons and technology leaders shaping the future of PCB fabrication.
Sales: From Pitch to PO
From the first cold call to finally receiving that first purchase order, the July PCB007 Magazine breaks down some critical parts of the sales stack. To up your sales game, read on!
The Hole Truth: Via Integrity in an HDI World
From the drilled hole to registration across multiple sequential lamination cycles, to the quality of your copper plating, via reliability in an HDI world is becoming an ever-greater challenge. This month we look at “The Hole Truth,” from creating the “perfect” via to how you can assure via quality and reliability, the first time, every time.
- Articles
- Columns
- Links
- Media kit
||| MENU - pcb007 Magazine
Gallium Oxide—the New Star in the Semiconductor Sky?
January 23, 2019 | Forschungsverbund Berlin e. V.Estimated reading time: 6 minutes
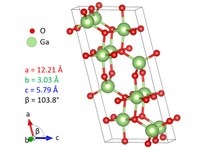
When it comes to crystals—and we’re talking about the really big bulk crystals used in electronic/photonic technology platforms for research, development and service—the Leibniz-Institut für Kristallzüchtung (IKZ) is the first port of call. Here, from an extremely hot molten mass, they grow isotopically pure silicon crystals to the size of 2-litre bottles for special applications (like the new standard kilogram, for example) and develop refined and new methods for producing conductive oxides of such metals as tin, zinc, and indium in the form of single crystals.
For some years now, the scientists at IKZ have also been intensely researching the material gallium oxide (Ga2O3). This new semiconductor has a relatively large bandgap of 4.8 electron volts, which means—in the field of power electronics especially, where high electric voltages are converted to low voltages—gallium oxide could overtake, at least partly, the stage from the current stars: silicon (Si), silicon carbide (SiC), and gallium nitride (GaN).
“So far, SiC has been the only substrate that has been easily produced without significant defects, but the growth rates during epitaxy are relatively slow. And for GaN, there are still no efficient processes for producing decent single crystals of large volume. So, instead, it gets deposited onto foreign substrates like sapphire or silicon, but their different lattice constants lead to misfit dislocations during epitaxy. And that is bad for the functionality of the components,” explains Dr. Martin Albrecht, Head of the Simulation & Characterisation Department of IKZ.
It is a very different story for gallium oxide: “We can already grow single crystals from the melt of about 5 x 10 cm in size. And this new material can even be doped over a wide range—from 1014 to 1020 cm-3.”
Getting this far, however, has been a long journey. Although the experiments with gallium oxide were done in 60-ties of the last century, the real development of that compound started in last few years. In 2009, IKZ then started to grow and develop bulk single crystals of this material, and it has demanded a lot of finesse on the part of the researchers. “Gallium oxide melts at about 1800°C and tends to degrade into gallium suboxide, metallic gallium, and molecular oxygen. So, in order to grow a single crystal from the melt, we need a very high oxygen pressure in the growth atmosphere,” explains Dr. Zbigniew Galazka, a crystal growth specialist at IKZ. Except that, iridium crucibles used to melt gallium oxide intensively oxidize in the presence of so much oxygen. “But for every problem there is a solution,” Galazka says with a glint of triumph. And this solution they found by closely studying the thermodynamics of the “terrible trio” of gallium oxide, oxygen, and iridium. Yes, iridium oxidizes into iridium dioxide that is very harmful, but only at low to moderate temperatures. At high temperatures, iridium trioxide is formed instead of iridium dioxide, which is gaseous and evaporates. So the researchers came up with a trick, which they have since internationally patented, and that is to introduce only a small amount of oxygen into a growth furnace at the beginning of the process (heating-up), called the Czochralski method, and only when the temperature rises to above 1200 - 1400 °C they increase the oxygen amount and evacuate the gaseous iridium trioxide far away from the growing crystal. This enabled us to grow large, 2-inch diameter Ga2O3 single crystals with further scale-up capabilities. Such large volumes of the crystals decrease the costs per volume unit and more importantly, large wafers for epitaxy and final devices can be prepared.
From the obtained crystals, they fabricated wafers and sent them to colleagues at the University of Santa Barbara, California, who used them as substrates in molecular beam epitaxy to deposit gallium oxide layers onto them and produce homoepitaxial structures. “Then, as other projects at the Institute came to an end in 2012, our director said: We can grow excellent crystals. We have experience with epitaxy. So why should the colleagues in the US have all the fun?” recounts Dr. Günter Wagner, Head of the Semiconducting Oxide Layers Workgroup. And with that, funds were acquired from the Leibniz Association (and since then from the Federal Ministry for Education and Research) and a facility for gas phase epitaxy was acquired. Ever since, the IKZ researchers have been vapour depositing their own gallium oxide onto own single crystal wafers.
Thus began the fiddly work, and some grappling in the dark, since nobody really knew what properties the new material had. Is the band gap direct or indirect? What defects may develop? And what are the optical properties of that semiconductor? To answer fundamental questions like these, one needs access to the material in good, reproducible quality. Martin Albrecht’s group closely examined the atomic arrangement in the single crystals under the electron microscope. “While other metal oxides crystallise out in a cubic or diamond structure, gallium oxide forms monoclinic crystals. That means the lattice constants a, b and c are slightly different (see Fig. 1). We first had to figure out which of the surfaces is most suitable for deposition,” Martin Albrecht explains. Once that was determined, the single crystals had to be cut in the appropriate direction and polished, for which they were sent to the Berlin company CrysTec.
Yet, even when polished to perfection, no crystal wafer is atomically smooth; the slightest stepped structure will always remain. Albrecht’s studies give the epitaxy specialists key pointers on how to grow ultra-thin oxide layers onto them in controlled fashion. “The step spacing, growth temperature and diffusion length of the atoms are all decisive parameters,” Albrecht explains. “The process is thermally controlled. Only when everything is perfectly tuned will the atoms overcome the barriers to become caught and chemically bonded in the right positions. You can think of it as much like little orbs in an egg carton.”
When a new material is researched, there are two distinct phases, says Günter Wagner. In the beginning, it doesn’t matter how high the production costs are or how slow the process is. “We are passing that stage now, and know that we can produce an excellent semiconductor at high quality and reproducibility.” The aim of the second phase is to arouse industrial interest in the material. “So, we are now figuring out the parameters for how to produce gallium oxide at equal quality but faster, cheaper and on a larger scale.” The Ferdinand-Braun-Institut (FBH) is already “whittling away” on components, Wagner adds, which will next be tested at the Power Electronics Laboratory of the Technische Universität (TU) Berlin. The project is incidentally a part of GraFOx, the science campus for the research of high performance semiconductors, funded by the Leibniz Association since 2016, in which IKZ, the Paul-Drude-Institut für Festkörperelektronik (PDI), the Fritz-Haber-Institut (Max Planck Society), the TU Berlin and Humboldt-Universität zu Berlin are involved.
The new semiconductor will allow extremely fast, low-loss electric circuits to be built. “Internationally, in particular in Japan and the US, the interest in this material and its potential applications has grown very fast over the past three years. It is also being funded by state-level programmes. As for applications, our focus is on power management as used in wind generators, tramways, fast trains, and electric cars,” says Wagner. In close cooperation with universities, research institutes and industrial partners, IKZ wants to establish in future the Ga2O3 material basis for high performance devices beyond today´s materials platforms Si, SiC and GaN in the important application field of power electronics.
Testimonial
"The I-Connect007 team is outstanding—kind, responsive, and a true marketing partner. Their design team created fresh, eye-catching ads, and their editorial support polished our content to let our brand shine. Thank you all! "
Sweeney Ng - CEE PCBSuggested Items
Indium Expert to Present on AI Thermal Challenges at INEMI Forum on Complex Integrated Electronics
08/26/2025 | Indium CorporationIndium Corporation Assistant Product Manager Foo Siang Hooi will deliver a technical presentation on addressing thermal challenges in AI and high-performance computing (HPC) with metal-based thermal interface materials (TIMs) at the International Electronics Manufacturing Initiative (INEMI) Forum on Complex Integrated Electronics, to be held September 17-18 in Penang, Malaysia.
Indium Corporation to Showcase Innovative Materials Enabling AI Technology at SEMICON Taiwan
08/20/2025 | Indium CorporationIndium Corporation®, a leading materials refiner, smelter, manufacturer, and supplier to the global electronics, semiconductor, AI, thin-film, and thermal management markets, will showcase its heterogeneous integration and assembly (HIA) products and thermal interface materials (TIMs) at SEMICON Taiwan, to be held September 10-12 in Taipei, Taiwan.
Indium Corporation Promotes Two Leaders in EMEA (Europe, Middle East, and Africa) Markets
08/05/2025 | Indium CorporationWith its commitment to innovation and growth through employee development, Indium Corporation today announced the promotions of Andy Seager to Associate Director, Continental Sales (EMEA), and Karthik Vijay to Senior Technical Manager (EMEA). These advancements reflect their contributions to the company’s continued innovative efforts with customers across Europe, the Middle East, and Africa (EMEA).
Indium Corporation Introduces New Flip-Chip Flux for Semiconductor Devices
07/31/2025 | Indium CorporationIndium Corporation, a leading materials refiner, smelter, manufacturer, and supplier, today announced the global availability of WS-910 Flip-Chip Flux, a new water-soluble flip-chip dipping flux designed to meet the demands of cutting-edge semiconductor devices.
Indium Corporation Welcomes 15 College Students to Award-Winning Summer Internship Program
07/24/2025 | Indium CorporationIndium Corporation, a premier materials refiner, smelter, manufacturer, and supplier to the global electronics, semiconductor, thin-film, and thermal management markets, is pleased to welcome 15 new interns into its award-winning summer internship program.