Flexible Bipolar Plates Made of Polymers Make It Possible to Build Compact Batteries
January 25, 2019 | Fraunhofer IISBEstimated reading time: 3 minutes
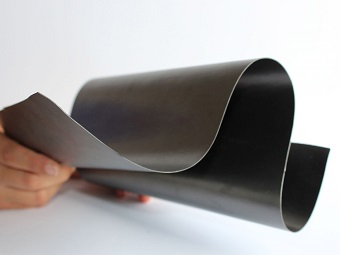
Whether used for power supply or in electric cars, current battery systems are based on a series of interconnected individual cells, which has certain disadvantages in terms of efficiency and manufacturing. Bipolar battery setups, in contrast, comprise compact stacks of individual cells. A new type of flexible and extremely thin bipolar plate allows batteries to be manufactured cost effectively.
Conventional battery systems are extremely complex. They usually consist of several individual cells that are connected with each other via wires. Not only is this costly and time-consuming, it also entails the danger of hot spots—areas in which the wires get too hot. In addition, every single one of these cells has to be packaged, meaning that a large portion of the battery consists of inactive material that does not contribute to battery performance. Bipolar batteries are designed to solve this problem by connecting the individual cells with each other using flat bipolar plates. However, this gives rise to other challenges: either the bipolar plates are made of metal and are thus prone to corrosion, or they are made of a carbon-polymer composite, in which case they have to be at least several millimeters thick as a result of the manufacturing process.
Material Savings of More Than 80%
Researchers at the Fraunhofer Institute for Environmental, Safety and Energy Technology UMSICHT in Oberhausen have now developed an alternative. “We manufacture bipolar plates from polymers that have been made electrically conductive,” says Dr.-Ing. Anna Grevé, department head at Fraunhofer UMSICHT. “In this way, we can produce very thin plates and—compared with conventional cells connected by wires—save over 80% of the material used.” In addition, the material offers numerous other advantages, such as the fact that it does not corrode. Another major advantage is that the material can be subsequently reshaped. This makes it possible, for example, to emboss structures, which are important for fuel cells. Moreover, the innovative new bipolar plates can be welded together, so the resulting battery system is absolutely tight. Conventional bipolar plates, in contrast, are unsuitable for welding due to the thermal and mechanical stressing of the material during manufacture. Joining them in such a way that neither gases nor liquids can pass through the joints requires seals. However, seals become quickly porous, and they also take up space. A further advantage of the new material is that the researchers are able to adapt the properties of the bipolar plates to specific requirements. “We can make plates that are so flexible that you can wrap them around your finger, as well as ones that are completely stiff,” specifies Grevé.
Cost-Effective Manufacture through Roll-To-Roll Technique
The primary challenge consisted in developing the material and the manufacturing process. “We use commercially available polymers and graphites, but the secret is in the recipe,” says Grevé. As the material is made up of about 80% graphites and only about 20% polymer, the processing methods have little in common with ordinary polymer processing. The team of researchers at Fraunhofer UMSICHT opted for the roll-to-roll technique, which allows cost-effective manufacturing, and adapted it using a lot of know-how. After all, the ingredients that go into the manufactured plates must be distributed homogeneously, and the plates also have to be mechanically stable and completely tight. Because of the initial structure of the materials, this was no easy feat. However, the experts also mastered this challenge. “We were able to fulfill all requirements in one process. Consequently, the plates can be used just as they are when they come out of the machine,” explains Grevé. Another advantage of the technique is that the plates can be manufactured in any size.
Suggested Items
Infineon Advances on 300-millimeter GaN Manufacturing Roadmap as Leading Integrated Device Manufacturer (IDM)
07/10/2025 | InfineonAs the demand for gallium nitride (GaN) semiconductors continues to grow, Infineon Technologies AG is poised to capitalize on this trend and solidify its position as a leading Integrated Device Manufacturer (IDM) in the GaN market.
TTCI Joins Printed Circuit Engineering Association to Strengthen Design-to-Test Collaboration and Workforce Development
07/09/2025 | The Test Connection Inc.The Test Connection Inc. (TTCI), a leading provider of electronic test and manufacturing solutions, is proud to announce its membership in the Printed Circuit Engineering Association (PCEA), further expanding the company’s efforts to support cross-functional collaboration, industry standards, and technical education in the printed circuit design and manufacturing community.
GlobalFoundries to Acquire MIPS to Accelerate AI and Compute Capabilities
07/09/2025 | GlobalFoundriesGlobalFoundries announced a definitive agreement to acquire MIPS, a leading supplier of AI and processor IP. This strategic acquisition will expand GF’s portfolio of customizable IP offerings, allowing it to further differentiate its process technologies with IP and software capabilities.
LITEON Technology Reports Consolidated June Sales of NT$13.6 Billion, Up 16% Y-o-Y
07/08/2025 | LITEON TechnologyLITEON Technology reported its June consolidated revenue of NT$13.6 billion. Thanks to the growth from power management in cloud computing, advanced server, and networking, the revenue is up 2% M-o-M, 16% Y-o-Y. The cumulative sales for January to June totaled NT$76.8 billion, up 24%, Y-o-Y.
Inside Aimtron’s Cross-border EMS Strategy
07/08/2025 | Nolan Johnson, SMT007 MagazineMukesh Vasani immigrated from a very small farming village in India to the U.S. in 1995 as a civil engineer. After shifting into electronics, Mukesh built his Chicago-based company, Aimtron, into a successful enterprise by combining quality with competitive pricing. He leveraged his roots in India to expand manufacturing without compromising on quality.