Fast, Flexible Ionic Transistors for Bioelectronic Devices
February 28, 2019 | Columbia EngineeringEstimated reading time: 5 minutes
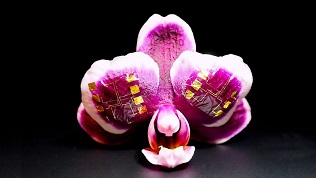
Many major advances in medicine, especially in neurology, have been sparked by recent advances in electronic systems that can acquire, process, and interact with biological substrates. These bioelectronic systems, which are increasingly used to understand dynamic living organisms and to treat human disease, require devices that can record body signals, process them, detect patterns, and deliver electrical or chemical stimulation to address problems.
Image Caption: IGT-based NAND and NOR gates conform to the surface of orchid petals (left). Scale bar, 1cm. Optical micrographs of NOR (upper right) and NAND (lower right) logic gates. Input (I1, I2) and output (O) configuration is indicated. Scale bar, 100 mm.
Transistors, the devices that amplify or switch electronic signals on circuits, form the backbone of these systems. However, they must meet numerous criteria to operate efficiently and safely in biological environments such as the human body. To date, researchers have not been able to build transistors that have all the features needed for safe, reliable, and fast operation in these environments over extended periods of time.
A team led by Dion Khodagholy, assistant professor of electrical engineering at Columbia Engineering, and Jennifer N. Gelinas, Columbia University Medical Center, Department of Neurology, and the Institute for Genomic Medicine, has developed the first biocompatible ion-driven transistor that is fast enough to enable real-time signal sensing and stimulation of brain signals.
(A) Schematic illustration of IGT cross-section and wiring diagram for device operation (upper). D-sorbitol creates an ion reservoir, maintaining mobile ions (green) that can travel within the channel; PEDOT-rich regions are shown in light blue and PSS lamellas in white (lower).
(B) Optical micrograph displaying the top view of an individual transistor. Scale bar, 20 µm. Inset shows a cross-section scanning electron microscopy image acquired at a tilt angle of 30°. Ion membrane (light red), channel (light blue) and Au contacts for gate (G) and source (S; beige) are visible. Scale bar, 5 µm.
The internal-ion-gated organic electrochemical transistor (IGT) operates via mobile ions contained within a conducting polymer channel to enable both volumetric capacitance (ionic interactions involving the entire bulk of the channel) and shortened ionic transit time. The IGT has large transconductance (amplification rate), high speed, and can be independently gated as well as microfabricated to create scalable conformable integrated circuits. In their study published today in Science Advances, the researchers demonstrate the ability of their IGT to provide a miniaturized, soft, conformable interface with human skin, using local amplification to record high quality neural signals, suitable for advanced data processing.
“We’ve made a transistor that can communicate using ions, the body’s charge carriers, at speeds fast enough to perform complex computations required for neurophysiology, the study of the nervous system function,” Khodagholy says. “Our transistor’s channel is made out of fully biocompatible materials and can interact with both ions and electrons, making communication with neural signals of the body more efficient. We’ll now be able to build safer, smaller, and smarter bioelectronic devices, such as brain-machine interfaces, wearable electronics, and responsive therapeutic stimulation devices, that can be implanted in humans over long periods of time.”
In the past, traditional silicon-based transistors have been used in bioelectronic devices, but they must be carefully encapsulated to avoid contact with body fluids—both for the safety of the patient and the proper operation of the device. This requirement makes implants based on these transistors bulky and rigid. In parallel, a good deal of work has been done in the organic electronics field to create inherently flexible transistors out of plastic, including designs such as electrolyte-gated or electrochemical transistors that can modulate their output based on ionic currents. However, these devices cannot operate fast enough to perform the computations required for bioelectronic devices used in neurophysiology applications.
Khodagholy and his postdoctoral research fellow George Spyropoulos, the first author of this work, built a transistor channel based on conducting polymers to enable ionic modulation, and, in order to make the device fast, they modified the material to have its own mobile ions. By shortening the distance that ions needed to travel within the polymer structure, they improved the speed of the transistor by an order of magnitude compared to other ionic devices of the same size.
Page 1 of 2
Suggested Items
Happy’s Tech Talk #38: Novel Metallization for UHDI
05/07/2025 | Happy Holden -- Column: Happy’s Tech TalkI have been involved in high-density electronics substrates since 1970 when I joined Hewlett-Packard’s RF semiconductor group after college. Figure 1 shows the difference between trace/space lithography for substrates and silicon starting in 1970. My projects involved sapphire circuits for RF devices, but the figure displays the state of PCBs and integrated CMOS circuits and their packaging, not discreet RF devices. Even then, semiconductors were 50X higher density.
New Database of Materials Accelerates Electronics Innovation
05/05/2025 | ACN NewswireIn a collaboration between Murata Manufacturing Co., Ltd., and the National Institute for Materials Science (NIMS), researchers have built a comprehensive new database of dielectric material properties curated from thousands of scientific papers.
New Database of Materials Accelerates Electronics Innovation
05/02/2025 | ACN NewswireIn a collaboration between Murata Manufacturing Co., Ltd., and the National Institute for Materials Science (NIMS), researchers have built a comprehensive new database of dielectric material properties curated from thousands of scientific papers.
Micron Announces Business Unit Reorganization to Capitalize on AI Growth Across All Market Segments
04/23/2025 | MicronMicron Technology, Inc., a leader in innovative memory and storage solutions, announced a market segment-based reorganization of its business units to capitalize on the transformative growth driven by AI, from data centers to edge devices.
Connected Commercial Drone Market to Reach $37.3 Billion Worldwide by 2029
04/04/2025 | Berg InsightBerg Insight, a leading IoT market research provider, today released a new report covering connected commercial drones used for industrial and governmental purposes.