Energy-efficient Superconducting Cable for Future Technologies
March 21, 2019 | KITEstimated reading time: 2 minutes
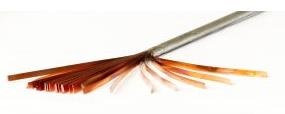
For connecting wind parks, for DC supply on ships, or for lightweight and compact high-current cabling in future electric airplanes: scientists of Karlsruhe Institute of Technology (KIT) have developed a versatile superconducting cable that can be manufactured easily. In case of moderate cooling, it transports electric energy with hardly any losses.
Superconductors transport electrical current at low temperatures with hardly any losses – this makes them attractive for a number of energy-efficient technologies. Usually, however, they require cooling with liquid helium to a temperature near minus 269 degrees Celsius. A new cable made by KIT, the High-temperature Superconductor Cross Conductor (HTS CroCo) can be used at minus 196 degrees Celsius already. “This is due to the special material we use,” say Dr. Walter Fietz and Dr. Michael Wolf of KIT’s Institute for Technical Physics (ITEP). The material is rare-earth barium-copper oxide (REBCO for short), whose superconductivity has been known since 1987. However, long lengths of the superconductor can only be manufactured in the form of thin tapes. “We have developed a method where several REBCO tapes are arranged such that they form a cross. The resulting cable can transport very high currents,” Fietz says.
The HTS CroCo has a higher current-carrying capacity, but needs less space and has a smaller weight than conventional copper or aluminum cables. Manufacture of the cable also is highly efficient. The innovative manufacturing process developed by KIT combines several steps. “Currently, we reach a production speed of one meter per minute on the demonstration scale,” Wolf says. At an accordingly scaled industrial facility, cable lengths of several hundred meters and more might be feasible, which will reduce costs. As the superconducting layer carrying the high current measures only a few thousandths of a millimeter, material expenses are kept within reasonable limits. ”Mass production still is prevented by the high costs for the complex manufacture of REBCO tapes,” Wolf says, “but industry is already developing new processes to reduce costs.”
CroCo is suited for energy-efficient generation of high magnetic fields and for transporting large amounts of electric energy. In future, these cables might be used to integrate large wind parks or solar power plants into the grid and to design leaner “electricity highways”. If liquid hydrogen is used for cooling, CroCo can even transport chemical and electrical energy together. “In principle, a CroCo can be applied wherever space is limited, but the amount of electrical energy to be transported is high,” Fietz says. Hence, application in ships and even in future electric airplanes is feasible.
Being “The Research University in the Helmholtz Association“, KIT creates and imparts knowledge for the society and the environment. It is the objective to make significant contributions to the global challenges in the fields of energy, mobility and information. For this, about 9,300 employees cooperate in a broad range of disciplines in natural sciences, engineering sciences, economics, and the humanities and social sciences. KIT prepares its 25,100 students for responsible tasks in society, industry, and science by offering research-based study programs. Innovation efforts at KIT build a bridge between important scientific findings and their application for the benefit of society, economic prosperity, and the preservation of our natural basis of life.
Suggested Items
The Evolution of Picosecond Laser Drilling
06/19/2025 | Marcy LaRont, PCB007 MagazineIs it hard to imagine a single laser pulse reduced not only from nanoseconds to picoseconds in its pulse duration, but even to femtoseconds? Well, buckle up because it seems we are there. In this interview, Dr. Stefan Rung, technical director of laser machines at Schmoll Maschinen GmbH, traces the technology trajectory of the laser drill from the CO2 laser to cutting-edge picosecond and hybrid laser drilling systems, highlighting the benefits and limitations of each method, and demonstrating how laser innovations are shaping the future of PCB fabrication.
Day 2: More Cutting-edge Insights at the EIPC Summer Conference
06/18/2025 | Pete Starkey, I-Connect007The European Institute for the PCB Community (EIPC) summer conference took place this year in Edinburgh, Scotland, June 3-4. This is the third of three articles on the conference. The other two cover Day 1’s sessions and the opening keynote speech. Below is a recap of the second day’s sessions.
Day 1: Cutting Edge Insights at the EIPC Summer Conference
06/17/2025 | Pete Starkey, I-Connect007The European Institute for the PCB Community (EIPC) Summer Conference took place this year in Edinburgh, Scotland, June 3-4. This is the second of three articles on the conference. The other two cover the keynote speeches and Day 2 of the technical conference. Below is a recap of the first day’s sessions.
Preventing Surface Prep Defects and Ensuring Reliability
06/10/2025 | Marcy LaRont, PCB007 MagazineIn printed circuit board (PCB) fabrication, surface preparation is a critical process that ensures strong adhesion, reliable plating, and long-term product performance. Without proper surface treatment, manufacturers may encounter defects such as delamination, poor solder mask adhesion, and plating failures. This article examines key surface preparation techniques, common defects resulting from improper processes, and real-world case studies that illustrate best practices.
RF PCB Design Tips and Tricks
05/08/2025 | Cherie Litson, EPTAC MIT CID/CID+There are many great books, videos, and information online about designing PCBs for RF circuits. A few of my favorite RF sources are Hans Rosenberg, Stephen Chavez, and Rick Hartley, but there are many more. These PCB design engineers have a very good perspective on what it takes to take an RF design from schematic concept to PCB layout.