Composite Overwrap 3D-Printed Rocket Thruster Endures Extreme Heat
April 9, 2019 | NASAEstimated reading time: 1 minute
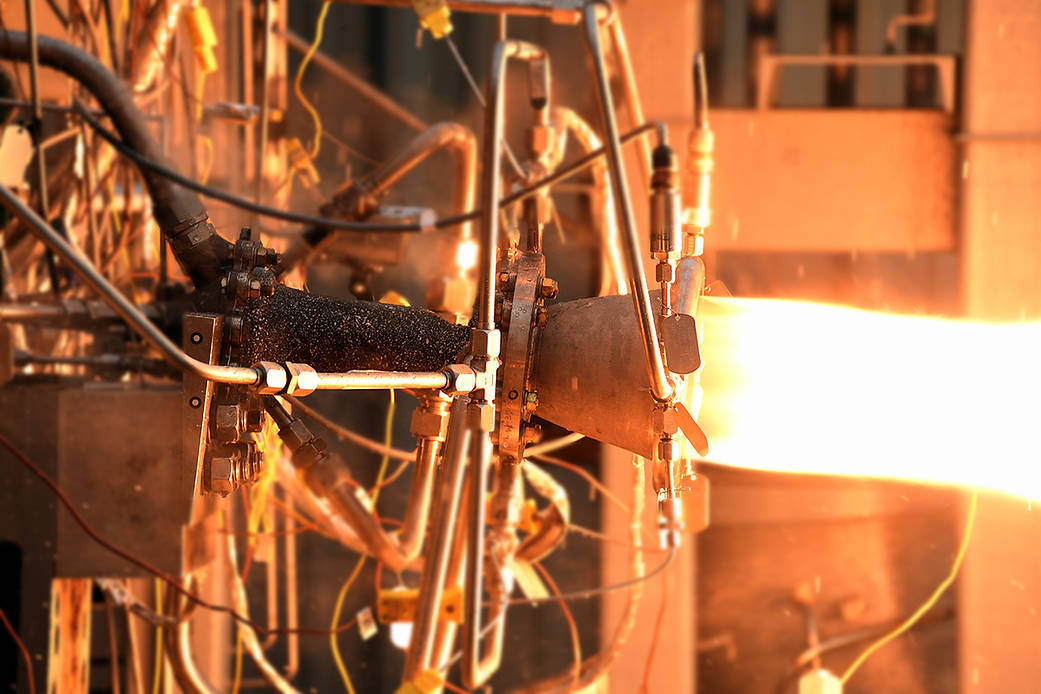
It’s rocket science—one NASA project is revolutionizing how liquid rocket engines are made. Additive manufacturing, better known as 3D printing, combined with advanced composite technology could help rocket engines be lighter, cheaper and easier to make.
Engineers at NASA tested a 2,400 lbf thrust 3D-printed copper rocket thrust chamber with composite overwrap to see if the uniquely made hardware could withstand the heat and structural loads from testing.
A total of 18 hot fire tests at high chamber pressure were conducted at NASA’s Marshall Space Flight Center, and the 3D printed hardware successfully withstood the heat and loads. The tests demonstrated the new 3D-printed and composite technologies, as well as a new additive technique for the nozzle, were feasible for thrust chamber assembly.
The tests were part of NASA’s Rapid Analysis and Manufacturing Propulsion Technology (RAMPT) project. Future RAMPT development work, under a public-private partnership with Auburn University and specialty manufacturing vendors, will mature the design and manufacturing technologies to increase scale, reduce cost and improve performance. Once complete, NASA will transfer the innovative technologies to industry.
Led out of the NASA Space Technology Mission Directorate’s Game Changing Development program, the RAMPT project addresses the longest lead time, highest cost and heaviest component in a rocket engine system.
Suggested Items
The Evolution of Picosecond Laser Drilling
06/19/2025 | Marcy LaRont, PCB007 MagazineIs it hard to imagine a single laser pulse reduced not only from nanoseconds to picoseconds in its pulse duration, but even to femtoseconds? Well, buckle up because it seems we are there. In this interview, Dr. Stefan Rung, technical director of laser machines at Schmoll Maschinen GmbH, traces the technology trajectory of the laser drill from the CO2 laser to cutting-edge picosecond and hybrid laser drilling systems, highlighting the benefits and limitations of each method, and demonstrating how laser innovations are shaping the future of PCB fabrication.
Day 2: More Cutting-edge Insights at the EIPC Summer Conference
06/18/2025 | Pete Starkey, I-Connect007The European Institute for the PCB Community (EIPC) summer conference took place this year in Edinburgh, Scotland, June 3-4. This is the third of three articles on the conference. The other two cover Day 1’s sessions and the opening keynote speech. Below is a recap of the second day’s sessions.
Day 1: Cutting Edge Insights at the EIPC Summer Conference
06/17/2025 | Pete Starkey, I-Connect007The European Institute for the PCB Community (EIPC) Summer Conference took place this year in Edinburgh, Scotland, June 3-4. This is the second of three articles on the conference. The other two cover the keynote speeches and Day 2 of the technical conference. Below is a recap of the first day’s sessions.
Preventing Surface Prep Defects and Ensuring Reliability
06/10/2025 | Marcy LaRont, PCB007 MagazineIn printed circuit board (PCB) fabrication, surface preparation is a critical process that ensures strong adhesion, reliable plating, and long-term product performance. Without proper surface treatment, manufacturers may encounter defects such as delamination, poor solder mask adhesion, and plating failures. This article examines key surface preparation techniques, common defects resulting from improper processes, and real-world case studies that illustrate best practices.
RF PCB Design Tips and Tricks
05/08/2025 | Cherie Litson, EPTAC MIT CID/CID+There are many great books, videos, and information online about designing PCBs for RF circuits. A few of my favorite RF sources are Hans Rosenberg, Stephen Chavez, and Rick Hartley, but there are many more. These PCB design engineers have a very good perspective on what it takes to take an RF design from schematic concept to PCB layout.