Ventec Focuses on High-mix Manufacturing
April 9, 2019 | Barry Matties, I-Connect007Estimated reading time: 4 minutes
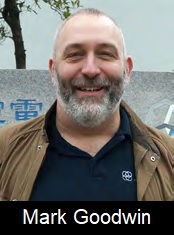
The I-Connect007 team recently toured Ventec International Group’s Suzhou factory where a modern, flexible manufacturing concept designed for fast delivery is enhancing their established volume manufacturing of specialty, high-reliability epoxy laminates and prepregs. The ongoing investment in the facility to offer flexible world-class high-mix manufacturing capabilities for polyimide, thermal management, low-loss, and signal integrity material solutions supports Ventec’s growth strategy in these specialty niches with fast global deliveries.
After a quick 20-minute high-speed train ride from Shanghai to Suzhou, we arrived at Ventec’s headquarters and lamination production facility. The facility also houses their highly active R&D center. Ventec, now a publicly traded company on the Taipei Stock Exchange, was founded in 2000. Since that time, they have established a global presence with additional manufacturing locations, service centers, and sales offices in key locations across Asia, Europe, and America.
In Suzhou, Ventec COO Mark Goodwin gave us a tour of the highly flexible manufacturing facility. When it comes to laminate production, you don’t usually think of it as a high-mix, low-volume business—especially in China—but that’s exactly how Ventec sees it. The factory is tooled with equipment capable of meeting their customer’s everchanging delivery needs.
When we asked Goodwin about their strategy, he explained it very simply. Read on to also hear Goodwin’s thoughts on supply chain integrity, UL testing and approval, standards, and the impact of Brexit.
Mark Goodwin: Our strategy is to make the right products available to customers quickly. It doesn’t work to have great products with long lead times to deliver them; customers lose interest. Thus, our whole strategy is not just to bring new products to the specialty sectors within the market, but to deliver them fast in relatively small quantities. We have presses down to 10 and even 6 daylights (openings) for our specialty products as well as the standard laminating presses of 20 daylights and double-sheet format for our FR-4 business.
Having much smaller presses allows us to close them on smaller volumes and deliver very quickly. Typical lead times into Europe are 10 days including transit times if we have enough prepreg on hand. That includes manufacturing cycle time plus transit time and customs clearance. If we don’t have prepreg, it might be 12–14 days, but it’s certainly not four to six weeks.
Barry Matties: Ventec started in 2000 and the growth has been phenomenal.
Goodwin: I’ve been involved since 2006, and have been responsible for EMEA and the Americas where our growth has been strong.
Matties: How are you doing in Asia?
Goodwin: That’s growing as well. You can see from some of the information we’ve shared with you today that our traditional FR-4 laminate business in certain sectors is being diluted, which is quite deliberate. We have focused our growth on specialty products that are being demanded by the market. Other sectors are shrinking as a percentage of our business but are staying stable in volume. The dicey FR-4 business is really being diluted as we’re steering that towards our thermal management and signal integrity products, and polyimides—all of the specialties.
Matties: And you are seeing growth in all of those.
Goodwin: Yes.
Matties: Is this a market-driven factor or a business choice that you’re making?
Goodwin: It’s both, but it’s driven by a strategy that we don’t want to be the biggest laminator in the world; we want to be first and we want to be fast. We also want to be flexible in terms of delivery to customers and competitive in price. You need all of those things. It’s no good having a great product but no delivery and a price point people can’t live with. You have to have all three: price, availability, and performance.
Matties: One of the advantages that Ventec enjoys is the distribution network that’s built in. Talk a little bit about that.
Goodwin: For me, it’s all about customer intimacy. We know our customers very well. We’re really close to our customers, and increasingly so with our OEM activity; we’re close to our customers’ customers as well. That is important with the new products—signal integrity, tec-speed 20.0 for 5G applications, etc.—it’s an OEM sell, so we’re gaining some traction there. It will take some time because we’re coming up against well-established competitors, but we have a drop-in product with tec-speed 20.0. In my opinion, it will come; something will give. Everybody told me we’d never get established in the polyimide business, but look where we are now; we’re the market leader in Europe and the world leaders in terms of product quality.
We make very clean laminates and prepregs, and you’ve seen some state-of-the-art equipment today walking around the factory including specialist filtration and a high degree of automated optical inspection on our prepreg treaters. They find and catch any inclusions before pressing laminates, but it is also part of a feedback loop driving the quality and the cleanliness of the product forward and making it better. That’s the more important part.
To read the full article, which appeared in the March 2019 issue of PCB007 Magazine, click here.
Visit I-007eBooks to download your copy of Ventec micro eBook today:
The Printed Circuit Designer's Guide to...Thermal Management with Insulated Metal Substrates
Testimonial
"In a year when every marketing dollar mattered, I chose to keep I-Connect007 in our 2025 plan. Their commitment to high-quality, insightful content aligns with Koh Young’s values and helps readers navigate a changing industry. "
Brent Fischthal - Koh YoungSuggested Items
VVDN Expands Manufacturing Footprint into the UAE to Meet Global Demand
08/20/2025 | PRNewswireVVDN Technologies, a global provider of software, product engineering and electronics manufacturing services & solutions, today announced it is setting up a new manufacturing facility in the UAE as part of its global expansion strategy.
Haylo Labs Acquires Plessey Semiconductors
08/20/2025 | Haylo LabsHaylo Labs has acquired Plessey Semiconductors, the UK’s leading innovator in microLED display technology.
Kimball Electronics Veterans ERG Members Proudly Participate in the 5th Annual Honor and Remember Run
08/20/2025 | Kimball ElectronicsVeterans and Military Service Advocacy (VMSA) Employee Resource Group (ERG) members Michael Mosher (Database Administration Engineer), Michael Stone (Test Technician Team Lead), and Joshua Belcher (Application Development Manager) took part in the 5th Annual Honor & Remember Run, a meaningful event dedicated to honoring fallen service members. The race featured a powerful memorial wall constructed from dog tags.
Meet Incap UK at the Electronic Component Show 2025
08/20/2025 | IncapIncap UK is pleased to be exhibiting at the Electronic Component Show 2025. This one-day event will take place on 18 September at the Kassam Stadium in Oxford, bringing together design engineers, purchasing professionals, manufacturers, distributors, and service providers to discover new products, solutions, and contacts. You will find us at stand 52.
Hon Hai Rotating CEO Yang Qiujin Wins 2025 Golden Yang Award for Women’s Power in Technology
08/20/2025 | Hon Hai Precision Industry Co., Ltd.Amid the global rise of "female-powered technology," Yang Qiujin, Rotating CEO of Hon Hai Precision Industry Co., Ltd. (TWSE: 2317), the world's largest platform solutions provider, has been awarded the "2025 Golden Yang Award - Female-Powered Technology" by the China Software Association/China Software Industry Association.