Ventec Names Sven Schnell Tech Sales Engineer for Germany, E. Europe
May 1, 2019 | Ventec International Group Co., Ltd.Estimated reading time: 2 minutes
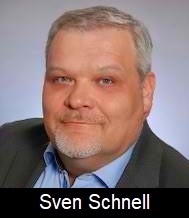
Ventec International Group Co., Ltd. has appointed Sven Schnell technical sales engineer. Sven will support sales activities in Germany and Eastern Europe, specializing in Ventec's advanced IMS/Thermal Management solutions including a distributed range of Thermal Interface Materials (TIM) from EMI Thermal.
Following the recent appointment of Jürgen Knörchen as Sales Director DACH in April and driven by the growing market and Ventec's strengthening position in the German-speaking region, Ventec is continuing to expand its sales force and adding further technical sales expertise. In his role as Technical Sales Engineer, Sven will be responsible for business development activities in Germany and Eastern Europe, specializing in thermal management solutions to help the company further develop its presence in the region. With his extensive knowledge and experience in applications requiring thermal performance beyond FR-4, Sven will play a key role in driving forward Ventec's insulated metal substrate (IMS) material families, thermally conductive and standard laminates and prepregs for multilayer PCBs as well as a complementary range of thermal interface materials (TIM) under Ventec's distributor agreement with EMI Thermal.
Sven has over 25 years of technical experience, joining Ventec from Henkel and Bergquist where he started out as Field Sales Manager and most recently acted as Account Manager for Siemens AG. He previously worked in sales & engineering roles with leading companies such as Würth, Hirose Electric and AVX/Elco and has a technical education in electronics.
"I am pleased to welcome Sven to our expanding technical team in Germany. His extensive industry knowledge and his specialist expertise for IMS materials will further enhance our commitment to providing technical support at the highest level to our German-speaking customers," said Jürgen Knörchen, Sales Director DACH at Ventec International Group. Mark Goodwin, COO EMEA & Americas added, "Building on the momentum from our IPO on the Taiwanese Stock Exchange this month, we continue to invest in our strong and skilled global team to help meet the growing demand for Ventec products & solutions."
About Ventec International Group
Ventec International is a premier supplier to the Global PCB industry. With volume manufacturing facilities in Taiwan and China and distribution locations and manufacturing sites in both the US and Europe, Ventec specializes in advanced copper clad glass reinforced and metal backed substrates. Ventec materials, which include high-quality enhanced FR4, high-speed/low-loss- & high-performance IMS material technology and an advanced range of thermal management solutions, are manufactured by Ventec using strict quality-controlled processes that are certified to AS9100 Revision D, IATF 16949:2016 and ISO 9001:2015, and are backed by a fully controlled and managed global supply chain, sales- and technical support-network. For more information, visit www.venteclaminates.com.
Visit I-007eBooks to download your copy of Ventec micro eBook today:
The Printed Circuit Designer's Guide to...Thermal Management with Insulated Metal Substrates
Suggested Items
The Evolution of Picosecond Laser Drilling
06/19/2025 | Marcy LaRont, PCB007 MagazineIs it hard to imagine a single laser pulse reduced not only from nanoseconds to picoseconds in its pulse duration, but even to femtoseconds? Well, buckle up because it seems we are there. In this interview, Dr. Stefan Rung, technical director of laser machines at Schmoll Maschinen GmbH, traces the technology trajectory of the laser drill from the CO2 laser to cutting-edge picosecond and hybrid laser drilling systems, highlighting the benefits and limitations of each method, and demonstrating how laser innovations are shaping the future of PCB fabrication.
Day 2: More Cutting-edge Insights at the EIPC Summer Conference
06/18/2025 | Pete Starkey, I-Connect007The European Institute for the PCB Community (EIPC) summer conference took place this year in Edinburgh, Scotland, June 3-4. This is the third of three articles on the conference. The other two cover Day 1’s sessions and the opening keynote speech. Below is a recap of the second day’s sessions.
Day 1: Cutting Edge Insights at the EIPC Summer Conference
06/17/2025 | Pete Starkey, I-Connect007The European Institute for the PCB Community (EIPC) Summer Conference took place this year in Edinburgh, Scotland, June 3-4. This is the second of three articles on the conference. The other two cover the keynote speeches and Day 2 of the technical conference. Below is a recap of the first day’s sessions.
Preventing Surface Prep Defects and Ensuring Reliability
06/10/2025 | Marcy LaRont, PCB007 MagazineIn printed circuit board (PCB) fabrication, surface preparation is a critical process that ensures strong adhesion, reliable plating, and long-term product performance. Without proper surface treatment, manufacturers may encounter defects such as delamination, poor solder mask adhesion, and plating failures. This article examines key surface preparation techniques, common defects resulting from improper processes, and real-world case studies that illustrate best practices.
RF PCB Design Tips and Tricks
05/08/2025 | Cherie Litson, EPTAC MIT CID/CID+There are many great books, videos, and information online about designing PCBs for RF circuits. A few of my favorite RF sources are Hans Rosenberg, Stephen Chavez, and Rick Hartley, but there are many more. These PCB design engineers have a very good perspective on what it takes to take an RF design from schematic concept to PCB layout.