Super PCB's Jessica Zhang on LEDs and Other Trending Business Areas
May 3, 2019 | Patty Goldman, I-Connect007Estimated reading time: 4 minutes
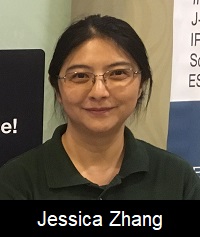
Patty Goldman spoke with Super PCB Program Manager Jessica Zhang at the recent West Penn SMTA Expo. Zhang provides an overview of the company and shares new business trends they’re seeing, including LEDs, wearable devices, and more.
Patty Goldman: Jessica, tell me a bit about yourself, and then we’ll talk about Super PCB.
Jessica Zhang: I’m a program manager at Super PCB and have been with the company for a long time. I love this company because it has a family environment—we all work as a team! Since 2003, we have been providing PCB prototypes and PCB production to different customers in various industries. We have a very thorough product line, including rigid boards, flex circuits, rigid-flex, aluminum boards for LED (which are becoming very popular), HDI, and so on.
We can provide such a complete product line because we are not just one factory. We work with multiple factories both overseas and in the United States. Some factories specialize in fast-turn prototypes; some in mass production.
Our engineering support in Plano, Texas will preview the Gerber files before we send them to the factory for manufacturing. This speeds up the manufacturing process. Some of our customers used to buy directly from China. A simple engineering question will go back and forth multiple days because of the time difference and language barrier. They switched to us because our local engineering team responds to engineering questions, typically within a day. Though our long-term relationships and buying power are important benefits, our customers also enjoy better pricing compared to going to China directly.
Goldman: Do you do any manufacturing in Texas or is it all overseas?
Zhang: We do not manufacture in Texas; that’s where our sales and technical support teams are located. As far as manufacturing, most of our partners are in Asia. We also have some in the United States for the ITAR requirements and domestic needs.
Goldman: So, what is your background in circuit boards?
Zhang: I’m from an engineering background. I have a master’s degree in electrical engineering from University of Texas. I started my career with major telecommunications equipment makers as a design engineer. I know the industry from both the vendor and customer sides.
Goldman: Where do you see your new business coming from, and what kind of circuit boards are you seeing the most these days?
Zhang: We continue seeing a lot of growth in LED. LEDs are replacing traditional lighting, so we see a lot of demand in that. We provide LED PCBs, both with FR-4 and the metal base, such as aluminum, copper, steel, etc. We’re also seeing a lot of growth in rigid-flex boards for medical devices and wearables—that’s a very hot trend right now. 5G, IOT and AI applications are the other hot areas.
Goldman: Those are the big ones. What else can you tell me about the types of boards, customers, or industries that you’re most involved with?
Zhang: Well, because we have a very complete product line, we don’t specialize in one industry, which is one of our advantages. Because we work with so many factories, we can be competitive with a lot of different boards. We work with all variety of industries, such as medical and telecommunications. A lot of our customers are contract manufacturers because they have very diverse needs due to the wide range of their customers.
Goldman: Suppose you receive a design for a PCB from a contract manufacturer, and you have a question about the design. Who do you talk to at the contract manufacturer?
Zhang: Their engineer. We do the design rule check for them, so if there is an engineering question, we’ll work with their engineer to resolve any questions before we send it to production.
Goldman: Then, they must have to turn around and work with their customer because the contract manufacturer doesn’t do the design, right? Is there a three-way conversation?
Zhang: Not necessarily. Often, we work with their end customer in the beginning at the prototype stage, and they refer us to their contract manufacturer. So, at the earliest stage, we’ve already resolved any issues.
Goldman: Do you have your prototypes made in the U.S. or China?
Zhang: Both. It depends on the customer. Some are more cost-sensitive and want it made overseas, while some need it very quickly. Others, such as military contracts, need it to be made domestically. Thus, it’s really up to the customer to decide.
Goldman: Do you travel to China yourself?
Zhang: Yes. I go back and forth. We’ve had very close relationships with the factories we work with for a very long time. And we are very committed to quality control, so we audit them, which is why we frequently travel back and forth.
Goldman: How has your experience been at the show today?
Zhang: Super PCB is a long-time SMTA member. We attend SMTA International in Chicago annually, and we do a few smaller shows throughout the country. We also attend our local shows in Texas every year, and we will be in Cleveland for the Ohio Expo. We find that the SMTA shows are well-run. The quality of attendees and exhibitors is high, and we are able to conduct successful business. Today is no exception.
Goldman: Thank you so much.
Zhang: Thank you.
Suggested Items
The Evolution of Picosecond Laser Drilling
06/19/2025 | Marcy LaRont, PCB007 MagazineIs it hard to imagine a single laser pulse reduced not only from nanoseconds to picoseconds in its pulse duration, but even to femtoseconds? Well, buckle up because it seems we are there. In this interview, Dr. Stefan Rung, technical director of laser machines at Schmoll Maschinen GmbH, traces the technology trajectory of the laser drill from the CO2 laser to cutting-edge picosecond and hybrid laser drilling systems, highlighting the benefits and limitations of each method, and demonstrating how laser innovations are shaping the future of PCB fabrication.
Day 2: More Cutting-edge Insights at the EIPC Summer Conference
06/18/2025 | Pete Starkey, I-Connect007The European Institute for the PCB Community (EIPC) summer conference took place this year in Edinburgh, Scotland, June 3-4. This is the third of three articles on the conference. The other two cover Day 1’s sessions and the opening keynote speech. Below is a recap of the second day’s sessions.
Day 1: Cutting Edge Insights at the EIPC Summer Conference
06/17/2025 | Pete Starkey, I-Connect007The European Institute for the PCB Community (EIPC) Summer Conference took place this year in Edinburgh, Scotland, June 3-4. This is the second of three articles on the conference. The other two cover the keynote speeches and Day 2 of the technical conference. Below is a recap of the first day’s sessions.
Preventing Surface Prep Defects and Ensuring Reliability
06/10/2025 | Marcy LaRont, PCB007 MagazineIn printed circuit board (PCB) fabrication, surface preparation is a critical process that ensures strong adhesion, reliable plating, and long-term product performance. Without proper surface treatment, manufacturers may encounter defects such as delamination, poor solder mask adhesion, and plating failures. This article examines key surface preparation techniques, common defects resulting from improper processes, and real-world case studies that illustrate best practices.
RF PCB Design Tips and Tricks
05/08/2025 | Cherie Litson, EPTAC MIT CID/CID+There are many great books, videos, and information online about designing PCBs for RF circuits. A few of my favorite RF sources are Hans Rosenberg, Stephen Chavez, and Rick Hartley, but there are many more. These PCB design engineers have a very good perspective on what it takes to take an RF design from schematic concept to PCB layout.