-
- News
- Books
Featured Books
- pcb007 Magazine
Latest Issues
Current IssueInventing the Future with SEL
Two years after launching its state-of-the-art PCB facility, SEL shares lessons in vision, execution, and innovation, plus insights from industry icons and technology leaders shaping the future of PCB fabrication.
Sales: From Pitch to PO
From the first cold call to finally receiving that first purchase order, the July PCB007 Magazine breaks down some critical parts of the sales stack. To up your sales game, read on!
The Hole Truth: Via Integrity in an HDI World
From the drilled hole to registration across multiple sequential lamination cycles, to the quality of your copper plating, via reliability in an HDI world is becoming an ever-greater challenge. This month we look at “The Hole Truth,” from creating the “perfect” via to how you can assure via quality and reliability, the first time, every time.
- Articles
- Columns
- Links
- Media kit
||| MENU - pcb007 Magazine
Estimated reading time: 3 minutes
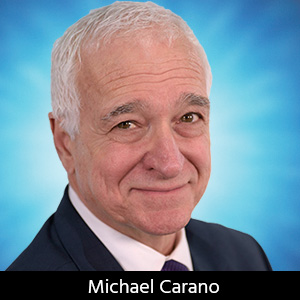
Contact Columnist Form
Trouble in Your Tank: OSP Performance—Effect of Film Thickness and Microetch
Two often overlooked performance attributes for organic solderability preservatives (OSPs) are the organic film thickness and the topography of the copper after microetch. Film thickness up to an extent is critical. However, the copper topography and surface preparation also play a role.
Thus, you should not overlook the critical nature of the overall OSP film thickness. Of course, thickness alone is not sufficient to ensure solderability. The uniformity of the organic film coupled with the film’s ability to minimize oxidation are important as well. The topography of the copper surface influences the uniformity of the OSP film as well as its thickness.
Microetching
Ensuring a clean and properly etched copper surface is necessary to affect the uniform deposition of the organic film on the copper surface. Concerns with thinner organic film where there is significant roughness of the copper are well-founded. Internal studies have shown that hydrogen peroxide microetchants impart a smoother topography to the copper surface than persulphate-based etchants. It is recommended that excessive microroughening be avoided. The concern is that with excessive roughness on the copper, there will be areas that have an insufficient thickness of OSP. In these situations, the thin areas will be more prone to oxidation (Figure 1). Some chemical processes impart rather large roughness profiles, such as those used to enhance solder mask adhesion; these types of etchants should be avoided.
Figure 1: The bottom image shows excessive roughness leading to areas where the OSP film is thin.
The previously described condition becomes more of an issue when the OSP film thickness is thin. But again, the thickness of the overall film does not necessarily imply that thicker is better. It is more about the uniformity of the OSP film and thickness over the peaks and valleys on the microetched copper surface (Figure 2). As a rule of thumb, an OSP film thickness of 1,500–2,000 angstroms (0.15–0.20 microns) is sufficient for lead-free assembly. However, that means minimum thickness over the thinnest areas of the profile.
Figure 2: OSP film over a peroxide-sulfuric acid etched surface (L) and OSP film over a heavily microroughened surface (R).
To ensure sufficient operating window for lead-free assembly with OSP, increase the film thickness to 2,500–3,000 angstroms. Regardless, do not overlook the importance of surface topography and its influence on the solderability or surface preparation. Compare the two pictures in Figure 3; on the left is a copper surface is cleaned with scrubbing only, and on the right is the scrubbed surface with OSP. No other surface preparation was used.
Figure 3: Improperly prepared surface with (L) a scrubbed surface and (R) a scrubbed surface with OSP.
Figure 4: Surface showing both discoloration and normal copper surface after processing in OSP.
Note the dark spots on the right image; these dark spots represent areas on the copper surface where the OSP is too thin or non-existent, which will lead to poor solderability. Again, ensure that the pre-clean line before OSP provides a clean, virgin copper surface with a uniformly etched surface. Ideally, 20–40 microinches of copper should be removed.
In case of insufficient microetching, the copper surface will show a dark color when exposed to air (Figure 4). The discoloration is due to the formation of cupric oxide. This type of oxidation will diminish solderability and further impact solder joint reliability. When the OSP film is too thin or not properly formed over the copper surface, oxygen can more easily reach the copper surface, which leads to discoloration. With increased exposure time and temperatures, the color of the copper layer changed from yellow to red-brown.
Figure 5: Slight discoloration of OSP-protected copper with arrows pointing to discoloration.
The discoloration is particularly troublesome when complex assembly and advanced packaging applications are in use. With respect to the latter, the solder ball attachment equipment must visually detect the solder ball point; in turn, this is required for the machine to be properly aligned with the OSP-coated bonding pad. The discoloration will interfere with the machine vision system and lead to low yields. While a light discoloration shown in Figure 5 will most likely not adversely affect solderability, such a condition will interfere with proper solder ball alignment to the BGA feature.
Michael Carano is VP of technology and business development for RBP Chemical Technology.
This article was originally published in the April 2019 issue of PCB007 Magazine.
More Columns from Trouble in Your Tank
Trouble in Your Tank: Metallizing Flexible Circuit Materials—Mitigating Deposit StressTrouble in Your Tank: Can You Drill the Perfect Hole?
Trouble in Your Tank: Yield Improvement and Reliability
Trouble in Your Tank: Causes of Plating Voids, Pre-electroless Copper
Trouble in Your Tank: Organic Addition Agents in Electrolytic Copper Plating
Trouble in Your Tank: Interconnect Defect—The Three Degrees of Separation
Trouble in Your Tank: Things You Can Do for Better Wet Process Control
Trouble in Your Tank: Processes to Support IC Substrates and Advanced Packaging, Part 5