Highly Flexible High-Energy Textile Lithium Battery to Cope with Surging Demand for Wearable Electronics
May 27, 2019 | The Hong Kong Polytechnic UniversityEstimated reading time: 2 minutes
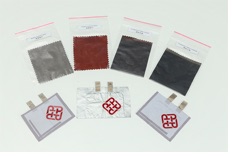
Researchers at The Hong Kong Polytechnic University (PolyU) have developed a highly flexible, high-energy textile lithium battery that offers more stable, durable and safe energy supply for wearable electronics with a myriad of applications, such as in healthcare monitoring, intelligent textiles, smartphones, global positioning system (GPS) tracking and internet of things (IoT).
PolyU's novel lightweight Textile Lithium Battery demonstrates high energy density of more than 450 Wh/L, and excellent flexibility — with a bending radius of less than 1mm, and foldability of over 1,000 cycles with marginal capacity degradation. In comparison, the existing bendable lithium batterycan only reach a bending radius of about 25 mm, and with much lower performance of less than 200 Wh/L. The Textile Lithium Battery, of less than 0.5 mm thick, also possesses fast charging/discharging capability, and long cycle life comparable with conventional lithium batteries.
The innovation developed by the research team of PolyU's Institute of Textiles and Clothing (ITC) has snatched three prizes at the 47th International Exhibition of Inventions of Geneva held in April this year, namely a Gold Medal and two Special Merit Awards.
Professor ZHENG Zijian, who leads the ITC research team, said, "Wearable technology has been named as the next global big market opportunity after smartphones. Global market revenues for wearable devices are forecasted to grow by leaps and bounds, of over 20% annually, to reach US$100 billion by 2024. As all wearable electronics will require wearable energy supply, our novel technology in fabricating Textile Lithium Battery offers promising solution to a wide array of next-generation applications, ranging from healthcare, infotainment, sports, aerospace, fashion, IoT to any sensing or tracking uses that may even exceed our imagination of today."
Lithium battery is currently the dominant rechargeable battery in the market due to its relatively high energy density and long cycle life. As conventional bulky heavy lithium battery is hard for use in wearable devices, over the past decade, scientists have put in efforts in developing bendable lithium battery, often by using metal foils as current collectors. However, it is only until the emergence of PolyU's Textile Lithium Battery that the bottlenecks over energy density, flexibility, mechanical robustness and cycling stability being able to be addressed.
Applying PolyU's patented novel technology of Polymer-Assisted Metal Deposition (PAMD), highly conductive metal, copper (Cu) and nickel (Ni) are uniformly and conformally deposited onto pre-treated fabrics. Such fabricated metallic fabrics, featuring low sheet resistance and large surface area, serve as current collectors in battery. After adding active materials to act as cathode and anode, the metallic fabrics, together with separator and electrolyte, are assembled into the Textile Lithium Battery.
Laboratory tests conducted by the ITC team have proven the extremely high mechanical stability, durability and safety of the Textile Lithium Battery under deformation. When the battery is repeatedly folded in half, twisted at different angles or freely crumpled, its voltage window remained unchanged. Bending test showed that the battery can be bent over 1,000 times with marginal capacity degradation. Safety tests conducted by continuous hammering, trimming with scissors and penetrating with nail proved the battery can stably provide power output for the electronic components with no risk of catching fire or burst.
Suggested Items
The Evolution of Picosecond Laser Drilling
06/19/2025 | Marcy LaRont, PCB007 MagazineIs it hard to imagine a single laser pulse reduced not only from nanoseconds to picoseconds in its pulse duration, but even to femtoseconds? Well, buckle up because it seems we are there. In this interview, Dr. Stefan Rung, technical director of laser machines at Schmoll Maschinen GmbH, traces the technology trajectory of the laser drill from the CO2 laser to cutting-edge picosecond and hybrid laser drilling systems, highlighting the benefits and limitations of each method, and demonstrating how laser innovations are shaping the future of PCB fabrication.
Day 2: More Cutting-edge Insights at the EIPC Summer Conference
06/18/2025 | Pete Starkey, I-Connect007The European Institute for the PCB Community (EIPC) summer conference took place this year in Edinburgh, Scotland, June 3-4. This is the third of three articles on the conference. The other two cover Day 1’s sessions and the opening keynote speech. Below is a recap of the second day’s sessions.
Day 1: Cutting Edge Insights at the EIPC Summer Conference
06/17/2025 | Pete Starkey, I-Connect007The European Institute for the PCB Community (EIPC) Summer Conference took place this year in Edinburgh, Scotland, June 3-4. This is the second of three articles on the conference. The other two cover the keynote speeches and Day 2 of the technical conference. Below is a recap of the first day’s sessions.
Preventing Surface Prep Defects and Ensuring Reliability
06/10/2025 | Marcy LaRont, PCB007 MagazineIn printed circuit board (PCB) fabrication, surface preparation is a critical process that ensures strong adhesion, reliable plating, and long-term product performance. Without proper surface treatment, manufacturers may encounter defects such as delamination, poor solder mask adhesion, and plating failures. This article examines key surface preparation techniques, common defects resulting from improper processes, and real-world case studies that illustrate best practices.
RF PCB Design Tips and Tricks
05/08/2025 | Cherie Litson, EPTAC MIT CID/CID+There are many great books, videos, and information online about designing PCBs for RF circuits. A few of my favorite RF sources are Hans Rosenberg, Stephen Chavez, and Rick Hartley, but there are many more. These PCB design engineers have a very good perspective on what it takes to take an RF design from schematic concept to PCB layout.