Plasmonic Technology Opens the Way to Mass Manufacture of High-Performance Chips
June 24, 2019 | CORDISEstimated reading time: 2 minutes
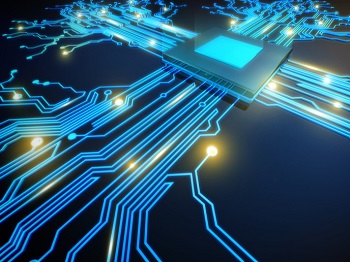
Photonics technology plays an important role in the European and global economies, driving innovation in sectors such as ICT, medicine, energy, military, manufacturing, agriculture and space. As its use spreads, it becomes increasingly important to find ways to mass produce photonics devices at low cost. This implies merging the technology with standardised production processes that are compatible with advanced electronics integrated circuit technologies. In other words, combining photonic and electronic functionalities in one chip.
The problem lies in incompatible dimensions. While electronic chip sizes are measured in nanometres, photonics chips exist in the order of micro- or millimetres. The EU-funded PLASMOfab project took up—and overcame—this challenge with the help of plasmonic technology. Ten industrial partners and academic and research institutes combined their know-how and expertise in photonic integrated circuits (PICs) and optoelectronics to create a plasmo-photonic chip. Now successfully completed, the project has made the mass manufacture of these high-performance components possible.
The PLASMOfab team’s work has brought about great advances in the technology used in optical data communications and biosensing for point-of-care applications. It has developed plasmonics that are compatible with complementary metal-oxide-semiconductor (CMOS) technology already used in electronics, and has used this technology to consolidate advanced PICs with electronic ICs in mass production. Standardised CMOS processes were used to merge CMOS-compatible metals like aluminium, titanium nitride and copper, and photonic structures with electronics.
Key Achievements
A major achievement of the project was the development of a novel ultra-compact plasmonic transmitter. The device has a footprint of 90 x 5.5 µm² and transmits 0.8 TBit/s (800 Gbit/s) through 4 individual 0.2 TBit/s transmitters. The project team also demonstrated how low propagation losses can be achieved using CMOS-compatible aluminium plasmonic waveguides co-integrated with silicon nitride photonics. Their findings were published in the journal ‘Scientific Reports’.
“PLASMOfab’s main goal has been to address the ever increasing needs for low energy, small size, high complexity and high performance mass manufactured PICs,” said Assistant Professor Nikos Pleros of project coordinator Aristotle University of Thessaloniki, Greece, in a press release posted on the ‘Synopsys’ website. “We have achieved this by developing a revolutionary yet CMOS-compatible fabrication platform for seamless co-integration of active plasmonics with photonic and electronic components.”
The partners expect that by further developing this technology they will be able to demonstrate the marked advantages that CMOS-compatible plasmonics have when applied to PICs. “When the best of all three worlds of plasmonics, photonics, and electronics converge in a single integration platform, PICs with unprecedented performance and functionality will be realized, targeting a diverse set of applications and industrial needs while meeting mass production requirements,” explained lead researcher Dr Dimitris Tsiokos of Aristotle University.
PLASMOfab (A generic CMOS-compatible platform for co-integrated plasmonics/photonics/electronics PICs towards volume manufacturing of low energy, small size and high performance photonic devices) concluded in December 2018. Its research has led to the launch of two new companies whose goals will be to commercialise the new technologies.
Suggested Items
The Evolution of Picosecond Laser Drilling
06/19/2025 | Marcy LaRont, PCB007 MagazineIs it hard to imagine a single laser pulse reduced not only from nanoseconds to picoseconds in its pulse duration, but even to femtoseconds? Well, buckle up because it seems we are there. In this interview, Dr. Stefan Rung, technical director of laser machines at Schmoll Maschinen GmbH, traces the technology trajectory of the laser drill from the CO2 laser to cutting-edge picosecond and hybrid laser drilling systems, highlighting the benefits and limitations of each method, and demonstrating how laser innovations are shaping the future of PCB fabrication.
Day 2: More Cutting-edge Insights at the EIPC Summer Conference
06/18/2025 | Pete Starkey, I-Connect007The European Institute for the PCB Community (EIPC) summer conference took place this year in Edinburgh, Scotland, June 3-4. This is the third of three articles on the conference. The other two cover Day 1’s sessions and the opening keynote speech. Below is a recap of the second day’s sessions.
Day 1: Cutting Edge Insights at the EIPC Summer Conference
06/17/2025 | Pete Starkey, I-Connect007The European Institute for the PCB Community (EIPC) Summer Conference took place this year in Edinburgh, Scotland, June 3-4. This is the second of three articles on the conference. The other two cover the keynote speeches and Day 2 of the technical conference. Below is a recap of the first day’s sessions.
Preventing Surface Prep Defects and Ensuring Reliability
06/10/2025 | Marcy LaRont, PCB007 MagazineIn printed circuit board (PCB) fabrication, surface preparation is a critical process that ensures strong adhesion, reliable plating, and long-term product performance. Without proper surface treatment, manufacturers may encounter defects such as delamination, poor solder mask adhesion, and plating failures. This article examines key surface preparation techniques, common defects resulting from improper processes, and real-world case studies that illustrate best practices.
RF PCB Design Tips and Tricks
05/08/2025 | Cherie Litson, EPTAC MIT CID/CID+There are many great books, videos, and information online about designing PCBs for RF circuits. A few of my favorite RF sources are Hans Rosenberg, Stephen Chavez, and Rick Hartley, but there are many more. These PCB design engineers have a very good perspective on what it takes to take an RF design from schematic concept to PCB layout.