-
- News
- Books
Featured Books
- pcb007 Magazine
Latest Issues
Current IssueInventing the Future with SEL
Two years after launching its state-of-the-art PCB facility, SEL shares lessons in vision, execution, and innovation, plus insights from industry icons and technology leaders shaping the future of PCB fabrication.
Sales: From Pitch to PO
From the first cold call to finally receiving that first purchase order, the July PCB007 Magazine breaks down some critical parts of the sales stack. To up your sales game, read on!
The Hole Truth: Via Integrity in an HDI World
From the drilled hole to registration across multiple sequential lamination cycles, to the quality of your copper plating, via reliability in an HDI world is becoming an ever-greater challenge. This month we look at “The Hole Truth,” from creating the “perfect” via to how you can assure via quality and reliability, the first time, every time.
- Articles
- Columns
- Links
- Media kit
||| MENU - pcb007 Magazine
Estimated reading time: 4 minutes
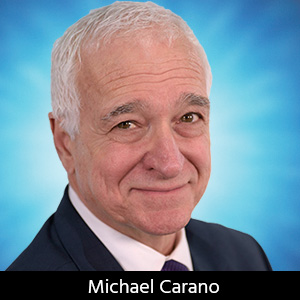
Contact Columnist Form
Trouble in Your Tank: Moving Into Microvias, Part 4
Copper deposit in the vias with electroless copper or alternatives, such as carbon-based direct plate processes to the vias, depends on process control, equipment design, and chemical parameters. When these are not in control, defects arise.
Introduction
Figure 1: Ideally plated blind via.
In "Moving Into Microvias, Part 3," I discussed the importance of desmear, particularly as it relates to higher-performance materials. In Part 4, I will present metallization for HDI blind via processing.
There are a few points to consider first. With respect to HDI and blind vias, the chemistry must find a way into these cup-shaped vias. The chemistry must be replenished as it is depleted to maximize the diffusion of the active ingredients to the vias. Of course, these same principles apply for through-hole vias as well.
Designing plating cells to ensure plating solution movement is critical to providing void-free deposits for HDI designs. I will delve into these cell design methods and other techniques in a future column. For now, let’s discuss metallization and potential issues.
Figure 2: Glass fiber bundles protruding into the drilled via (the arrows show areas where there are apparent voids).
HDI Via Defects
The big concern for HDI and vias is not getting a sufficient thickness of copper in the blind vias. This includes voids at the capture pad, thin or tapered plating as the via wall meets the capture pad, poor throwing power, adhesion failures, etc. Figure 1 depicts an ideal state for plating of blind vias. The plating is uniform in thickness at the capture and along the via sidewall.
However, not everything is this easy. As blind via structures become deeper (3–5 mils) and diameters shrink (from 4 mils to 3 mils or less), fluid dynamics play an increasingly critical role. Allowing for sufficient plating solution exchange in these cup-shaped vias is necessary to ensure that key addition agents—such as brighteners and leveling agents as well as copper ions—are replenished, as these are depleted during the plating operation. The same holds true for conventional electroless copper and direct metalization processes.
Secondly, starting with a quality-formed blind via plays a significant role in plating continuity and uniformity. Figure 2 depicts a poorly drilled via. Glass fibers and more of a cup-shaped via negatively impacts the plating quality.
With poorly formed vias, there is an extreme difficulty with moving plating solutions into the via. A poorly formed via will bring about mass transport limitations. The inability to move fresh plating electrolyte into blind vias will result in thin plating near the junction of the side wall and capture pad. Thin plating thickness presents an area of weakness that can lead to separation or cracking within the copper.
Figure 3: Dark area indicates no copper plating. This is a front light of the blind via.
Figure 4: Front light evaluation, showing no copper voiding issue.
In addition, laser via formation of blind vias can lead to another issue shown in Figure 3. The section shown in the image points to an area where there are voids in the blind via. It is recommended that both front light (FL) and back light (BL) testing be included in the fabricator’s routine quality control protocol. The FL technique is particularly useful because this test helps to determine the location of the voiding. Figure 4 shows an example without voids. Further analysis of the nonconformance found in Figure 3 is shown in Figure 5.
The gap shown in Figure 5 exacerbates the difficulty in getting plating into this gap and eliminating the voided or very thin copper plating. Fluid dynamics do play a significant role in achieving uniform plated deposits. However, when there are these gaps or wedges existing between the copper and the resin, increased solution convection may be insufficient.
Figure 5: SEM view of the via in the flexible circuit (note the gap).
Regardless of the defect shown in Figure 5, what are the potential causes of the gap or wedge seen in the previous image? There could be several causes. However, let’s understand what it is not. In the real-life situation seen previously, the fabricator laid the blame on the micro-etch and the electroless copper process. There was no attempt to look either upstream or downstream in the manufacturing process.
The supplier tech team, however, performed its own investigation. The team asked for data on laser via formation used at this facility and examined materials immediately after laser via formation. As the results showed (Figure 6), the wedge or gap already existed.
Figure 6: Two views of the gap after via formation and before any further processing.
Moving back further into the process, the team noted that gap existed on certain flexible materials supplied by a third party. When the chemical supplier tech team obtained flex materials from a second supplier, examination showed no gap or wedge existed either before or after chemical processing. Of course, chemicals such as those used in desmear or micro-etching, could have led to this defect. But in this situation, this was not the case.
Conclusion
Lesson learned: Don’t assume it is the chemistry. Fabricators, in many instances, may not want to take any responsibilities. As a process troubleshooter, stick to your guns and conduct a thorough upstream and downstream investigation. Ensuring a quality copper deposit in the vias with electroless copper or alternatives, such as carbon-based direct plate processes to the vias, depends on process control, equipment design, and chemical parameters. When these are not in control, defects arise.
Michael Carano is VP of technology and business development for RBP Chemical Technology.
This column was initially published in the July 2019 issue of PCB007 Magazine.
More Columns from Trouble in Your Tank
Trouble in Your Tank: Metallizing Flexible Circuit Materials—Mitigating Deposit StressTrouble in Your Tank: Can You Drill the Perfect Hole?
Trouble in Your Tank: Yield Improvement and Reliability
Trouble in Your Tank: Causes of Plating Voids, Pre-electroless Copper
Trouble in Your Tank: Organic Addition Agents in Electrolytic Copper Plating
Trouble in Your Tank: Interconnect Defect—The Three Degrees of Separation
Trouble in Your Tank: Things You Can Do for Better Wet Process Control
Trouble in Your Tank: Processes to Support IC Substrates and Advanced Packaging, Part 5