Data Rate Increase on the International Space Station Supports Future Exploration
August 26, 2019 | NASAEstimated reading time: 2 minutes
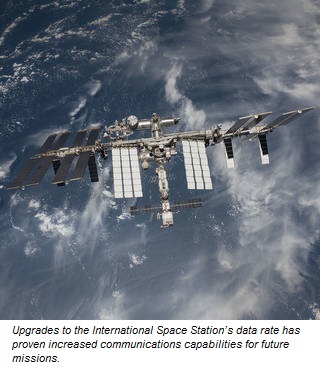
NASA recently doubled the rate at which data from the International Space Station returns to Earth, paving the way for similar future upgrades on Gateway, NASA’s upcoming outpost in lunar orbit, and other exploration missions. This new data rate will enable the space station to send back more science data faster than ever before.
NASA’s missions, both near and far, rely on quick and effective communications to relay critical mission data to control centers and scientists here on Earth. The station now supports a 600 megabit-per-second (Mbps) connection, doubling the amount of data that the station can transmit and receive at a time.
“NASA’s communications networks play a pivotal role in every NASA mission, enabling data from human spaceflight, space and Earth science research missions and technological demonstrations to reach Earth for the benefit of humanity,” said George Morrow, the acting center director of NASA’s Goddard Space Flight Center in Greenbelt, Maryland. “This increase in data rate capability for the International Space Station underlines our commitment to provide high-quality operational services for NASA exploration missions today and in the future.”
The space station’s unique environment allows astronauts to conduct research that would not otherwise be possible on Earth. These experiments and technology demonstrations are increasingly reliant on high data rates between the station and researchers on Earth. The work on the orbiting laboratory provides knowledge in human research, experience in long-duration spaceflight, and capabilities for technology demonstrations that may enable future missions. With the data rate increase, the station can now accommodate new experiments and technology demonstrations that require higher resolution or more detailed data than was previously possible.
The space station communicates with Earth through radio frequency signals using a system of Tracking and Data Relay Satellites (TDRS) and ground-based antennas called the Space Network. The TDRS are placed in a high orbit above the Earth, over various strategic locations so that they can relay data to the ground from anywhere in orbit. Landlines then send the signal to various NASA centers, and their computer systems turn the radio signal back into readable data. To send data back, the process repeats in the other direction. This happens with less than a one-second delay in communication.
“This project demonstrated that advanced radio frequency waveforms can be used efficiently to increase data rates and improve performance for high-rate communication services,” said Risha George, the upgrade project lead for the Space Network. “Operational use of these advanced waveforms proves that they can also be used for future missions, such as on the Gateway, a small spaceship that will orbit the Moon and provide a stepping stone to human exploration on Mars.”
Several components in this global communications system were upgraded to support the increased data rate, including a new digital ground architecture for the Space Network. Technicians updated the space station’s software-based modem, improved data processors at various NASA centers, and enhanced routers, interfaces and other equipment and software at the ground stations. The circuits and bandwidth of the terrestrial data lines between the various Earth-based components were also upgraded. The team then performed extensive testing to ensure the upgrades worked correctly. All of this was done while still providing real-time support to the more than 40 missions the network regularly supports.
“Partnerships like this are crucial to our continued success as an agency,” said Penny Roberts, the upgrade project lead for the space station. “Our continued partnership will transition us to 600 Mbps, and who knows where else we will go together.”
Suggested Items
Specially Developed for Laser Plastic Welding from LPKF
06/25/2025 | LPKFLPKF introduces TherMoPro, a thermographic analysis system specifically developed for laser plastic welding that transforms thermal data into concrete actionable insights. Through automated capture, evaluation, and interpretation of surface temperature patterns immediately after welding, the system provides unprecedented process transparency that correlates with product joining quality and long-term product stability.
Smart Automation: The Power of Data Integration in Electronics Manufacturing
06/24/2025 | Josh Casper -- Column: Smart AutomationAs EMS companies adopt automation, machine data collection and integration are among the biggest challenges. It’s now commonplace for equipment to collect and output vast amounts of data, sometimes more than a manufacturer knows what to do with. While many OEM equipment vendors offer full-line solutions, most EMS companies still take a vendor-agnostic approach, selecting the equipment companies that best serve their needs rather than a single-vendor solution.
Keysight, NTT, and NTT Innovative Devices Achieve 280 Gbps World Record Data Rate with Sub-Terahertz for 6G
06/17/2025 | Keysight TechnologiesKeysight Technologies, Inc. in collaboration with NTT Corporation and NTT Innovative Devices Corporation (NTT Innovative Devices), today announced a groundbreaking world record in data rate achieved using sub-THz frequencies.
Priority Software Announces the New, Game-Changing aiERP
06/12/2025 | Priority SoftwarePriority Software Ltd., a leading global provider of ERP and business management software announces its revolutionary aiERP, leveraging the power of AI to transform business operations.
Breaking Silos with Intelligence: Connectivity of Component-level Data Across the SMT Line
06/09/2025 | Dr. Eyal Weiss, CybordAs the complexity and demands of electronics manufacturing continue to rise, the smart factory is no longer a distant vision; it has become a necessity. While machine connectivity and line-level data integration have gained traction in recent years, one of the most overlooked opportunities lies in the component itself. Specifically, in the data captured just milliseconds before a component is placed onto the PCB, which often goes unexamined and is permanently lost once reflow begins.