Selecting the Proper Flex Coverlayer Material
September 6, 2019 | Dave Lackey, American Standard CircuitsEstimated reading time: 4 minutes
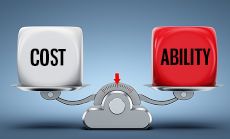
Introduction
What is a flex coverlayer? What’s its purpose? Are they new or have they been around a while? Why do they matter to my design?
Coverlayers are polymer materials used to cover and protect the copper traces of the flex circuit product. As implied, there are a number of different options available for protecting the circuits, and they serve different design requirements in terms of cost, performance, and flexural endurance optimization. When specifying the choice, it is critical to call out not just the type of coverlayer material but also the thickness requirement. This can be very important in certain types of constructions, especially when a flex circuit will experience dynamic flexing during use.
It is also important to know and understand that there are different types of materials available for use as coverlayer materials and that there is no single, ideal solution. The appropriate material choice will be based on a number of factors, such as application, cost, projected life, etc. Coverlayer selection requires a thorough analysis that balances both cost and performance to ensure the proper choice. Key considerations include how much will the flex circuits be bent in the field (install or dynamic), can a hybrid approach be taken (solder mask in SMT locations and coverlayer everywhere else), and is the performance improvement of laser machined coverlayers worth the significant cost increase (and potentially leadtime increase). In any case, due diligence is required to make the proper coverlayer technology choice.
Machining Options for the Coverlayer
Both mechanical and laser machining are common fabricating processes used in today’s printed circuit industry. Each method employs its own distinct equipment set and has its own advantages and disadvantages. Preference for coverlayers among the two typically depends on the application, volume/lead time, and cost.
Mechanical Machining
Certainly, mechanical machine is the triedand-true historical method of fabricating coverlayers. The primary benefit of mechanical machining is that the fabricator can use their existing equipment set used for PCB drilling and fabrication. It is fast, has multiple stations (4–6), there is no learning curve, and every PCB fabricator already has the equipment. Hole quality depends on the drill tool, and there are minimum hole-size limitations to mechanically machining.
Laser Machining
Requires a capital investment for a laser drill; however, the equipment will primarily be used for laser drilling the raw PCBs. Many PCB fabricators do not have existing laser equipment and the cost is much higher than mechanical machines. The actual lasering is faster per hole, but it is a single station. The laser produces a precise hole and has virtually no minimum hole size.
Flex Coverlayer or Flexible Solder Mask
In terms of cost, a flexible solder mask is generally the least expensive. Some one- or two-layer flex circuits that will not be subject to multiple flex cycles or extreme radius bends can be coated with an epoxy-based solder mask that is designed to flex without cracking. However, this is not recommended when the design requires any dynamic or extreme flexing. The other option is a laminated flex coverlayer. These are typically materials that have a makeup that is identical to the flex core material and are best suited for dynamic flexible circuit applications.
The flex coverlayer material is a polyimide sheet with acrylic adhesive on one side. It is usually pre-machined to create openings in the sheet where the final finish is required. The coverlayer sheets are typically applied in a lamination press using special pads to ensure conformity around the copper features on the flex layer. For rigid-flex circuits, the coverlayer is generally cut to only protrude into the rigid portion by no more than 50 mils. The purpose of this is to allow all the plated holes in the rigid-flex to be void of any acrylic adhesive, as it can affect the hole wall plating integrity. Figure 1 shows an example of flexible solder mask and coverlayer being used in flex circuits.
Figure 1: Flexible solder mask and coverlayer used in flex circuits.
It is worthwhile to note here that the bond ply used to laminate flex layers together is like a coverlayer, but it has adhesive on two sides. It is further worth noting that prepregs (glass cloth, which has been pre-impregnated with a thermosetting resin) used for making rigid circuits are used in the construction of rigid-flex circuits where they serve in the role of bond ply. It is also important to note that coverlayer material can come in typical thickness intervals from 0.5–5 mils (12–125 μm) of polyimide and 0.5–3 mils (12–75 μm) of adhesive. Based on the design and application, the adhesive thickness requirement is typically decided by the copper thickness to which it is being bonded. The higher copper weight, the more adhesive is needed. There are various thicknesses of coverlayer coatings, and a general rule of thumb is one mil of adhesive (coverlayer) for every ounce of surface copper it is covering. The same holds true for bond ply.
To read the full article, which appeared in the August 2019 issue of SMT007 Magazine, click here.
Testimonial
"Advertising in PCB007 Magazine has been a great way to showcase our bare board testers to the right audience. The I-Connect007 team makes the process smooth and professional. We’re proud to be featured in such a trusted publication."
Klaus Koziol - atgSuggested Items
Indium Corporation Promotes Two Leaders in EMEA (Europe, Middle East, and Africa) Markets
08/05/2025 | Indium CorporationWith its commitment to innovation and growth through employee development, Indium Corporation today announced the promotions of Andy Seager to Associate Director, Continental Sales (EMEA), and Karthik Vijay to Senior Technical Manager (EMEA). These advancements reflect their contributions to the company’s continued innovative efforts with customers across Europe, the Middle East, and Africa (EMEA).
MacDermid Alpha Electronics Solutions Unveils Unified Global Website to Deepen Customer, Talent, and Stakeholder Engagement
07/31/2025 | MacDermid Alpha Electronics SolutionsMacDermid Alpha Electronics Solutions, the electronics business of Elements Solutions Inc, today launched macdermidalpha.com - a unified global website built to deepen digital engagement. The launch marks a significant milestone in the business’ ongoing commitment to delivering more meaningful, interactive, and impactful experiences for its customers, talent, and stakeholders worldwide.
KOKI to Showcase Analytical Services and New HF1200 Solder Paste at SMTA Guadalajara 2025
07/31/2025 | KOKIKOKI, a global leader in advanced soldering materials and process optimization services, will exhibit at the SMTA Guadalajara Expo & Tech Forum, taking place September 17 & 18, 2025 at Expo Guadalajara, Salón Jalisco Halls D & E in Guadalajara, Mexico.
Weller Tools Supports Future Talent with Exclusive Donation to SMTA Michigan Student Soldering Competition
07/23/2025 | Weller ToolsWeller Tools, the industry leader in hand soldering solutions, is proud to announce its support of the upcoming SMTA Michigan Expo & Tech Forum by donating a limited-edition 80th Anniversary Black Soldering Set to the event’s student soldering competition.
Koh Young Appoints Tom Hattori as President of Koh Young Japan
07/21/2025 | Koh YoungKoh Young Technology, the global leader in True 3D measurement-based inspection solutions, announced the appointment of Tom Hattori as President of Koh Young Japan (JKY).