-
- News
- Books
Featured Books
- pcb007 Magazine
Latest Issues
Current IssueInventing the Future with SEL
Two years after launching its state-of-the-art PCB facility, SEL shares lessons in vision, execution, and innovation, plus insights from industry icons and technology leaders shaping the future of PCB fabrication.
Sales: From Pitch to PO
From the first cold call to finally receiving that first purchase order, the July PCB007 Magazine breaks down some critical parts of the sales stack. To up your sales game, read on!
The Hole Truth: Via Integrity in an HDI World
From the drilled hole to registration across multiple sequential lamination cycles, to the quality of your copper plating, via reliability in an HDI world is becoming an ever-greater challenge. This month we look at “The Hole Truth,” from creating the “perfect” via to how you can assure via quality and reliability, the first time, every time.
- Articles
- Columns
- Links
- Media kit
||| MENU - pcb007 Magazine
Estimated reading time: 2 minutes
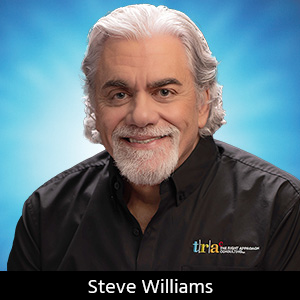
The Right Approach: A Conversation With Prototron’s Van Chiem
I recently spoke with Van Chiem, a process engineer with Prototron Circuits, about developing in-house flex and rigid-flex processes and capabilities at their facility in Tucson, Arizona.
Steve Williams: Van, you have a very diverse technical background in PCBs. Can you tell us a little bit about your past experience and what brought you to Prototron?
Van Chiem: I have over 25 years of experience in this field. I started as a process engineer at Unisys Corporation where we made computer chips and advanced component packaging for interconnections like wire bonding, flip chip, and tab bonding. This is my ninth job in the PCB industry. Another job I had was with Enthone in Connecticut at the time, which is now MacDermid. I was in the research group working on the formulation of solder mask to try and convert it to photodefinable dielectric material for microvia. Instead of drilling, we used a photo process to create a micro via, and then the electroless copper followed by plating the copper to form the microvia with smart circuitry. That was my second job in the industry. I have had seven more jobs, but that might be too much to talk about.
Williams: How about we save the other seven for the next interview (laughs). So, you’ve seen a lot of technology changes in the last 25 years in the industry and were actually one of the original technologists.
Chiem: Well, I don’t like to talk about myself, but I guess you could say that.
Williams: How long have you been at Prototron?
Chiem: About a year and a half.
Williams: And you have already accomplished quite a bit here. Prototron brought you on board for the specific purpose of upgrading their technology in a number of different areas, right?
Chiem: Yes, Kim O’Neil, the general manager here, brought me on especially to develop flex and rigid-flex processes.
Williams: So, you were kind of the R&D lead on developing that technology and getting it to become a viable technology here in Tucson. What was that process like, and what were the challenges?
Chiem: From a technology standpoint, there weren’t any major challenges, as this technology is 20–30 years old and very mature. I used to work at Honeywell back in the ‘90s where we built flex as a chip carrier every day and talked about 3-mil lines and spaces 20 years ago.
To read this entire column, which appeared in the July 2019 issue of Design007 Magazine, click here.
More Columns from The Right Approach
The Right Approach: ‘Twas the Night Before Christmas (Harley-style)The Right Approach: I Hear the Train A Comin'
The Right Approach: Culture Change is Key to a QMS
The Right Approach: Leadership 101—Be a Heretic, Not a Sheep
The Right Approach: Leadership 101—The Law of Legacy
The Right Approach: Leadership 101: The Law of Explosive Growth
The Right Approach: Leadership 101—The Law of Timing
The Right Approach: The Law of Sacrifice