Making Waves with a Hammer and a 3D Printer
September 16, 2019 | PennEngineeringEstimated reading time: 1 minute
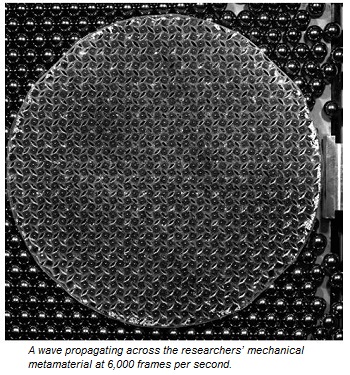
For Jordan Raney, assistant professor in the Department of Mechanical Engineering and Applied Mechanics, cutting-edge science sometimes involves whacking a rubber disc with a hammer.
In a recent experiment, he and Chengyang Mo, a graduate student in Raney’s Architected Materials Laboratory, used a 3D-printer to make this unusual, Frisbee-sized structure. It consists of hundreds of connected rubber squares, each with a ball bearing inside. It’s an example of a “mechanical metamaterial,” a class of systems that exhibit unusual physical behaviors stemming from their internal geometry rather than from the properties of the materials of which they’re made.
Raney and Mo were trying to understand the propagation of a unique type of nonlinear wave called a soliton. To do that, they placed their structure on top of ball bearings and set up a high-speed camera to record the wave’s motion at 6,000 frames per second. Then, according to their paper, published in the journal Physical Review Letters, they “excited the sample with an impactor” — or hit it with a $6 mallet from the hardware store.
Their study is the first to show how these waves travel in a soft 2D system.
“This is interesting because, in 2D, the wave changes dramatically depending on where you hit the squares,” says Mo. “When the impact is applied at a certain angle, the wave focuses itself and does not disperse as it moves.”
This behavior has been previously observed in granular materials, like sand, where it has been referred to as a “sound bullet.”
“It’s like a disturbance at the edge of a pond,” says Raney, “but instead of spreading outward in a circular fashion, the wave travels across the pond as one compact pulse. That way, all the energy of the input can be received by the output rather than spreading.”
A better understanding of mechanical metamaterials like the one Raney, Mo and their co-authors created could have biomedical applications, as impacting the body’s tissues with controlled pulses of energy could have diagnostic or therapeutic value. Aerospace, naval or automotive applications are also possible, with mechanical metamaterials rerouting the force of an impact away from people or payloads.
Suggested Items
I-Connect007 Editor’s Choice: Five Must-Reads for the Week
06/27/2025 | Nolan Johnson, I-Connect007While news outside our industry keeps our attention occupied, the big news inside the industry is the rechristening of IPC as the Global Electronics Association. My must-reads begins with Marcy LaRont’s exclusive and informative interview with Dr. John Mitchell, president and CEO of the Global Electronics Association. For designers, have we finally reached the point in time where autorouters will fulfill their potential?
Knocking Down the Bone Pile: Tin Whisker Mitigation in Aerospace Applications, Part 3
06/25/2025 | Nash Bell -- Column: Knocking Down the Bone PileTin whiskers are slender, hair-like metallic growths that can develop on the surface of tin-plated electronic components. Typically measuring a few micrometers in diameter and growing several millimeters in length, they form through an electrochemical process influenced by environmental factors such as temperature variations, mechanical or compressive stress, and the aging of solder alloys.
RTX, the Singapore Economic Development Board Sign MOU Outlining 10-year Growth Roadmap
06/20/2025 | RTXRTX and the Singapore Economic Development Board (EDB) have signed a Memorandum of Understanding (MoU) which outlines a 10-year roadmap to further long-term strategic collaboration in Singapore.
Indra Signs Agreement with AXISCADES to Boost Production of Cutting-Edge Systems in India
06/18/2025 | PRNewswireParis Air Show -- Indra and the Indian technology company AXISCADES have signed an agreement to collaborate on the production of solutions for the aerospace and defense markets.
GKN Aerospace Delivers First High Voltage EWIS System for Clean Aviation’s SWITCH Project
06/16/2025 | GKN AerospaceGKN Aerospace has completed and delivered the first high voltage Electrical Wiring Interconnection System (EWIS) for the Clean Aviation SWITCH project.