Photovoltaic-Powered Sensors for the “Internet of Things”
September 27, 2019 | MITEstimated reading time: 5 minutes
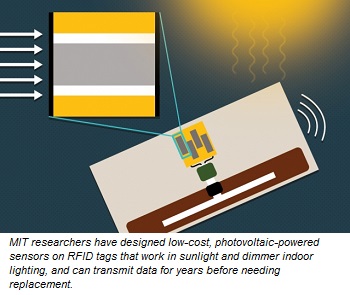
By 2025, experts estimate the number of “internet of things” devices — including sensors that gather real-time data about infrastructure and the environment — could rise to 75 billion worldwide. As it stands, however, those sensors require batteries that must be replaced frequently, which can be problematic for long-term monitoring.
MIT researchers have designed photovoltaic-powered sensors that could potentially transmit data for years before they need to be replaced. To do so, they mounted thin-film perovskite cells — known for their potential low cost, flexibility, and relative ease of fabrication — as energy-harvesters on inexpensive radio-frequency identification (RFID) tags.
The cells could power the sensors in both bright sunlight and dimmer indoor conditions. Moreover, the team found the solar power actually gives the sensors a major power boost that enables greater data-transmission distances and the ability to integrate multiple sensors onto a single RFID tag.
“In the future, there could be billions of sensors all around us. With that scale, you’ll need a lot of batteries that you’ll have to recharge constantly. But what if you could self-power them using the ambient light? You could deploy them and forget them for months or years at a time,” says Sai Nithin Kantareddy, a PhD student in the MIT Auto-ID Laboratory. “This work is basically building enhanced RFID tags using energy harvesters for a range of applications.”
In a pair of papers published in the journals Advanced Functional Materials and IEEE Sensors, MIT Auto-ID Laboratory and MIT Photovoltaics Research Laboratory researchers describe using the sensors to continuously monitor indoor and outdoor temperatures over several days. The sensors transmitted data continuously at distances five times greater than traditional RFID tags — with no batteries required. Longer data-transmission ranges mean, among other things, that one reader can be used to collect data from multiple sensors simultaneously.
Depending on certain factors in their environment, such as moisture and heat, the sensors can be left inside or outside for months or, potentially, years at a time before they degrade enough to require replacement. That can be valuable for any application requiring long-term sensing, indoors and outdoors, including tracking cargo in supply chains, monitoring soil, and monitoring the energy used by equipment in buildings and homes.
Joining Kantareddy on the papers are: Department of Mechanical Engineering (MechE) postdoc Ian Matthews, researcher Shijing Sun, chemical engineering student Mariya Layurova, researcher Janak Thapa, researcher Ian Marius Peters, and Georgia Tech Professor Juan-Pablo Correa-Baena, who are all members of the Photovoltaics Research Laboratory; Rahul Bhattacharyya, a researcher in the AutoID Lab; Tonio Buonassisi, a professor in MechE; and Sanjay E. Sarma, the Fred Fort Flowers and Daniel Fort Flowers Professor of Mechanical Engineering.
Combining Two Low-Cost Technologies
In recent attempts to create self-powered sensors, other researchers have used solar cells as energy sources for internet of things (IoT) devices. But those are basically shrunken-down versions of traditional solar cells — not perovskite. The traditional cells can be efficient, long-lasting, and powerful under certain conditions “but are really infeasible for ubiquitous IoT sensors,” Kantareddy says.
Traditional solar cells, for instance, are bulky and expensive to manufacture, plus they are inflexible and cannot be made transparent, which can be useful for temperature-monitoring sensors placed on windows and car windshields. They’re also really only designed to efficiently harvest energy from powerful sunlight, not low indoor light.
Perovskite cells, on the other hand, can be printed using easy roll-to-roll manufacturing techniques for a few cents each; made thin, flexible, and transparent; and tuned to harvest energy from any kind of indoor and outdoor lighting.
The idea, then, was combining a low-cost power source with low-cost RFID tags, which are battery-free stickers used to monitor billions of products worldwide. The stickers are equipped with tiny, ultra-high-frequency antennas that each cost around three to five cents to make.
RFID tags rely on a communication technique called “backscatter,” that transmits data by reflecting modulated wireless signals off the tag and back to a reader. A wireless device called a reader — basically similar to a Wi-Fi router — pings the tag, which powers up and backscatters a unique signal containing information about the product it’s stuck to.
Traditionally, the tags harvest a little of the radio-frequency energy sent by the reader to power up a little chip inside that stores data, and uses the remaining energy to modulate the returning signal. But that amounts to only a few microwatts of power, which limits their communication range to less than a meter.
The researchers’ sensor consists of an RFID tag built on a plastic substrate. Directly connected to an integrated circuit on the tag is an array of perovskite solar cells. As with traditional systems, a reader sweeps the room, and each tag responds. But instead of using energy from the reader, it draws harvested energy from the perovskite cell to power up its circuit and send data by backscattering RF signals.
Page 1 of 2
Suggested Items
Specially Developed for Laser Plastic Welding from LPKF
06/25/2025 | LPKFLPKF introduces TherMoPro, a thermographic analysis system specifically developed for laser plastic welding that transforms thermal data into concrete actionable insights. Through automated capture, evaluation, and interpretation of surface temperature patterns immediately after welding, the system provides unprecedented process transparency that correlates with product joining quality and long-term product stability.
Smart Automation: The Power of Data Integration in Electronics Manufacturing
06/24/2025 | Josh Casper -- Column: Smart AutomationAs EMS companies adopt automation, machine data collection and integration are among the biggest challenges. It’s now commonplace for equipment to collect and output vast amounts of data, sometimes more than a manufacturer knows what to do with. While many OEM equipment vendors offer full-line solutions, most EMS companies still take a vendor-agnostic approach, selecting the equipment companies that best serve their needs rather than a single-vendor solution.
Keysight, NTT, and NTT Innovative Devices Achieve 280 Gbps World Record Data Rate with Sub-Terahertz for 6G
06/17/2025 | Keysight TechnologiesKeysight Technologies, Inc. in collaboration with NTT Corporation and NTT Innovative Devices Corporation (NTT Innovative Devices), today announced a groundbreaking world record in data rate achieved using sub-THz frequencies.
Priority Software Announces the New, Game-Changing aiERP
06/12/2025 | Priority SoftwarePriority Software Ltd., a leading global provider of ERP and business management software announces its revolutionary aiERP, leveraging the power of AI to transform business operations.
Breaking Silos with Intelligence: Connectivity of Component-level Data Across the SMT Line
06/09/2025 | Dr. Eyal Weiss, CybordAs the complexity and demands of electronics manufacturing continue to rise, the smart factory is no longer a distant vision; it has become a necessity. While machine connectivity and line-level data integration have gained traction in recent years, one of the most overlooked opportunities lies in the component itself. Specifically, in the data captured just milliseconds before a component is placed onto the PCB, which often goes unexamined and is permanently lost once reflow begins.