Moving E-Cars Into the Fast Lane
October 2, 2019 | Fraunhofer-GesellschaftEstimated reading time: 2 minutes
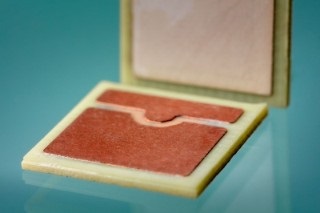
Researchers have been looking into silicon carbide, a promising alternative material for the semiconductor industry, for several years now. The Fraunhofer Institute for Reliability and Microintegration IZM joined forces with partners in the SiC Module project to ramp up this type of power semiconductor for industrial manufacturing. Their effort goes to boost the efficiency of drivetrains in electric vehicles and extend these vehicles’ range.
Embedded silicon carbide on its way to mass manufacturing for e-mobility applications.
Electromobility has its naysayers, with some skeptics pointing to limitations such as electric cars’ top speed and maximum range. Both depend on the built-in power electronics, the electronic heart of e-mobility. Size, weight and efficiency are three make-or-break factors for power electronics destined for installation in e-cars. Silicon carbide (SiC), a new semiconductor material, ticks all three boxes. It is more efficient yet leaves a smaller footprint than conventional semiconductors such as silicon.
Even so, silicon carbide is not to be found in any e-car on the road today. As it stands, this semiconductor material is still confined to research labs. To port it from the lab to the factory, the SiC Module project has factored all the conditions of industrial manufacturing into the equation from the outset. The module’s design is a case in point: Researchers at the Fraunhofer IZM are basing it on the structure of the classic printed circuit board that the industry has long favored. This should expedite its rollout.
Shorter power lines, better power routing
The module is also benefitting from the latest scientific advances. Rather than wire-bonding the semiconductor to the package, the researchers decided to embed it directly in the circuit with a galvanic-assisted copper contact to shorten the wires and optimize power routing. The team also brought the potential customer on board for this development effort. In the project’s first year, they drew up a specification sheet pinpointing the electrical, thermal and performance requirements for the module and semiconductor. The researchers worked closely with users, catering to their wishes when they determined the product specs. Automakers, component suppliers and OEMs were directly involved in the effort to map out the power-electronic modules’ size, layout and electrical circuits. This collective sought to make the most of the space available in the vehicles’ powertrain. Lars Böttcher, group leader at the Fraunhofer IZM and head of the SiC sub-project project, says, “We’re going beyond a general proof of concept because we are developing more than just a prototype in this project”. The goal is to ramp up both the new semiconductor material silicon carbide and the embedding technology for mass production.
The Federal Ministry of Education and Research is funding the project with 3.89 million euros as part of the E-Mobility Call. Slated to run from January 2018 to December 2020, the project involves six partners alongside the Fraunhofer IZM: AixControl – Gesellschaft für leistungselektronische Systemlösungen mbH, Conti Temic microelectronic GmbH, Rheinisch-Westfälischen Technischen Hochschule Aachen, Robert Bosch GmbH, Schweizer Electronic AG, and TLK-Thermo GmbH.
Suggested Items
The Evolution of Picosecond Laser Drilling
06/19/2025 | Marcy LaRont, PCB007 MagazineIs it hard to imagine a single laser pulse reduced not only from nanoseconds to picoseconds in its pulse duration, but even to femtoseconds? Well, buckle up because it seems we are there. In this interview, Dr. Stefan Rung, technical director of laser machines at Schmoll Maschinen GmbH, traces the technology trajectory of the laser drill from the CO2 laser to cutting-edge picosecond and hybrid laser drilling systems, highlighting the benefits and limitations of each method, and demonstrating how laser innovations are shaping the future of PCB fabrication.
Day 2: More Cutting-edge Insights at the EIPC Summer Conference
06/18/2025 | Pete Starkey, I-Connect007The European Institute for the PCB Community (EIPC) summer conference took place this year in Edinburgh, Scotland, June 3-4. This is the third of three articles on the conference. The other two cover Day 1’s sessions and the opening keynote speech. Below is a recap of the second day’s sessions.
Day 1: Cutting Edge Insights at the EIPC Summer Conference
06/17/2025 | Pete Starkey, I-Connect007The European Institute for the PCB Community (EIPC) Summer Conference took place this year in Edinburgh, Scotland, June 3-4. This is the second of three articles on the conference. The other two cover the keynote speeches and Day 2 of the technical conference. Below is a recap of the first day’s sessions.
Preventing Surface Prep Defects and Ensuring Reliability
06/10/2025 | Marcy LaRont, PCB007 MagazineIn printed circuit board (PCB) fabrication, surface preparation is a critical process that ensures strong adhesion, reliable plating, and long-term product performance. Without proper surface treatment, manufacturers may encounter defects such as delamination, poor solder mask adhesion, and plating failures. This article examines key surface preparation techniques, common defects resulting from improper processes, and real-world case studies that illustrate best practices.
RF PCB Design Tips and Tricks
05/08/2025 | Cherie Litson, EPTAC MIT CID/CID+There are many great books, videos, and information online about designing PCBs for RF circuits. A few of my favorite RF sources are Hans Rosenberg, Stephen Chavez, and Rick Hartley, but there are many more. These PCB design engineers have a very good perspective on what it takes to take an RF design from schematic concept to PCB layout.