-
- News
- Books
Featured Books
- pcb007 Magazine
Latest Issues
Current IssueThe Hole Truth: Via Integrity in an HDI World
From the drilled hole to registration across multiple sequential lamination cycles, to the quality of your copper plating, via reliability in an HDI world is becoming an ever-greater challenge. This month we look at “The Hole Truth,” from creating the “perfect” via to how you can assure via quality and reliability, the first time, every time.
In Pursuit of Perfection: Defect Reduction
For bare PCB board fabrication, defect reduction is a critical aspect of a company's bottom line profitability. In this issue, we examine how imaging, etching, and plating processes can provide information and insight into reducing defects and increasing yields.
Voices of the Industry
We take the pulse of the PCB industry by sharing insights from leading fabricators and suppliers in this month's issue. We've gathered their thoughts on the new U.S. administration, spending, the war in Ukraine, and their most pressing needs. It’s an eye-opening and enlightening look behind the curtain.
- Articles
- Columns
- Links
- Media kit
||| MENU - pcb007 Magazine
Communication, Part 4: The Top 5 Causes of Engineering Delays
October 25, 2019 | Steve Williams, The Right Approach Consulting LLCEstimated reading time: 3 minutes
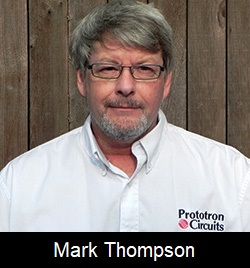
Editor’s note: Read Part 1, Part 2, and Part 3, and stay tuned for Parts 5 and 6 of this series.
In Part 4 of this series on how PCB fabricators and designers can better communicate, Bob Chandler from CA Design and Mark Thompson from Prototron Circuits address the top five causes of engineering delays.
Steve Williams: Our topic for today is the top five causes for engineering delays at the board shop. Mark, let’s start with you.
Mark Thompson: From where I sit, the first cause is conflicting or improper notes that don’t reflect the data that’s been supplied. The second cause is bad data, such as silkscreens that have been left on signal layers that are creating broken nets. The third cause is when changes are made to the agreed-upon impedance geometry. Somebody might come to me and say, “I have an eight-layer board. Layers one, three, six, and eight are 50-ohm, 90-ohm, and 100-ohm, and they’re based on this material type, this copper weight, and this color of solder mask.” If something changes—such as if they copper pour stuff too close and it changes from a free space geometry to a co-planner structure, or if they changed the color of the solder mask—I have to review everything.
The fourth is missing files, which we frequently experience, such as IPC-6012 Class 3 jobs that are missing netlists, where we’re then obligated to run an IPC netlist. The last cause is sending something and then not getting a response. It’s great that somebody will order something in a three-day turn and ask us to manufacture it in that amount of time, but if I’m quick in responding, we expect them to respond in a timely manner as well. However, it doesn’t always happen that way; sometimes, there’s a delay of one to three days.
Williams: That’s quite the laundry list. I know that none of that stuff applies to CA Design, Bob, but what do you have to say about the five causes Mark mentioned? Is this what you hear from your customers when they talk about other design services and some of the challenges they have with them?
Bob Chandler: Most of those items are very typical and come down to one main cause: communication. Talk to your customers before and after. Make sure that you get the information for controlled impedance in advance, as well as for blind and buried vias, and stick to it. Also, talk to the fabrication house when you send it to see if they have any problems and answer their questions when they come back. It all comes back down to communication.
Williams: That’s a great point. One of my favorite consultants/business strategists is Tom Peters. I saw him speak one time, and he talked about an interview with the CEO of a Fortune 500 company. Tom asked, “What’s the secret to your success?” And the CEO said, “We’ve discovered an incredible technique on how to satisfy our customers: We actually talk to them,” so your points on communication is spot on. I think Mark would agree.
Thompson: Yes. And much of what we have discussed, and will discuss, in this series starts with that same conversation.
Williams: I know what Mark would say, but how would you suggest opening up those communication channels between the board shop and the designer, Bob? Who should own that or initiate first?
Chandler: The designer should own that a great deal. The electrical engineer in charge of the project and should ensure that it happens, and the designer should be able to talk directly to the fabrication house to get the answers they need to lay out the board properly.
Thompson: I completely agree.
Williams: And board shops aren’t without some skin in the game either; they have an obligation to keep the communication going.
Thompson: Absolutely.
Williams: Very good. This is a topic that everyone in the PCB industry faces, and if you ask anybody in the business, they would probably come up with a similar list to Mark’s. I appreciate both of your time.
Thompson: It was great to talk to you again.
Chandler: Thank you.
Steve Williams is the president of The Right Approach Consulting and an I-Connect007 columnist.
Bob Chandler is CTO of CA Design (cadesign.net) and a senior Allegro/OrCAD trainer and consultant.
Mark Thompson, CID+, is in engineering support at Prototron Circuits and an I-Connect007 columnist. Thompson is also the author of The Printed Circuit Designer's Guide to… Producing the Perfect Data Package. Visit I-007eBooks.com to download this book and other free, educational titles.
Suggested Items
KYZEN to Highlight Understencil and PCB Cleaners at SMTA Querétaro Expo and Tech Forum
07/09/2025 | KYZEN'KYZEN, the global leader in innovative environmentally responsible cleaning chemistries, will exhibit at the SMTA Querétaro Expo & Tech Forum, scheduled to take place Thursday, July 24, at Centro de Congresos y Teatro Metropolitano de Querétaro.
Driving Innovation: Direct Imaging vs. Conventional Exposure
07/01/2025 | Simon Khesin -- Column: Driving InnovationMy first camera used Kodak film. I even experimented with developing photos in the bathroom, though I usually dropped the film off at a Kodak center and received the prints two weeks later, only to discover that some images were out of focus or poorly framed. Today, every smartphone contains a high-quality camera capable of producing stunning images instantly.
Hands-On Demos Now Available for Apollo Seiko’s EF and AF Selective Soldering Lines
06/30/2025 | Apollo SeikoApollo Seiko, a leading innovator in soldering technology, is excited to spotlight its expanded lineup of EF and AF Series Selective Soldering Systems, now available for live demonstrations in its newly dedicated demo room.
Indium Corporation Expert to Present on Automotive and Industrial Solder Bonding Solutions at Global Electronics Association Workshop
06/26/2025 | IndiumIndium Corporation Principal Engineer, Advanced Materials, Andy Mackie, Ph.D., MSc, will deliver a technical presentation on innovative solder bonding solutions for automotive and industrial applications at the Global Electronics A
Fresh PCB Concepts: Assembly Challenges with Micro Components and Standard Solder Mask Practices
06/26/2025 | Team NCAB -- Column: Fresh PCB ConceptsMicro components have redefined what is possible in PCB design. With package sizes like 01005 and 0201 becoming more common in high-density layouts, designers are now expected to pack more performance into smaller spaces than ever before. While these advancements support miniaturization and functionality, they introduce new assembly challenges, particularly with traditional solder mask and legend application processes.