-
-
News
News Highlights
- Books
Featured Books
- pcb007 Magazine
Latest Issues
Current IssueThe Hole Truth: Via Integrity in an HDI World
From the drilled hole to registration across multiple sequential lamination cycles, to the quality of your copper plating, via reliability in an HDI world is becoming an ever-greater challenge. This month we look at “The Hole Truth,” from creating the “perfect” via to how you can assure via quality and reliability, the first time, every time.
In Pursuit of Perfection: Defect Reduction
For bare PCB board fabrication, defect reduction is a critical aspect of a company's bottom line profitability. In this issue, we examine how imaging, etching, and plating processes can provide information and insight into reducing defects and increasing yields.
Voices of the Industry
We take the pulse of the PCB industry by sharing insights from leading fabricators and suppliers in this month's issue. We've gathered their thoughts on the new U.S. administration, spending, the war in Ukraine, and their most pressing needs. It’s an eye-opening and enlightening look behind the curtain.
- Articles
- Columns
- Links
- Media kit
||| MENU - pcb007 Magazine
Flexibility Is Key to Direct Imaging Success
January 28, 2020 | Nolan Johnson, I-Connect007Estimated reading time: 10 minutes
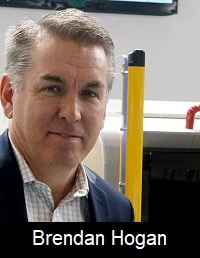
Miva Technologies has a unique perspective, supplying direct imagers to both the semiconductor and PCB markets. Brendan F. Hogan, managing director of MivaTek, explains that while each industry has its own set of requirements and difficulties, the lines are blurring between the two industries, demanding more flexibility from equipment suppliers.
Nolan Johnson: Brendan, let’s start with a quick overview of MivaTek.
Brendan F. Hogan: Miva Technologies is a company that started out in film plotters and chrome mask makers. This set up an interesting dichotomy: while silver film plotters were for the circuit board market, and the chrome mask makers were for semiconductors, the base technology is very similar. Over our last 20 years of business, we’ve now evolved into direct-write methodologies for those two separate market segments. We have direct imagers for circuit boards that can do 50-micron features, and for semiconductors, we direct write 1-micron line and space on complete wafer substrates. It’s a very interesting place to be as the industry evolves from what used to be separate markets to one; the lines are blurring between what’s a micro function and what’s a circuit board function.
Johnson: We certainly see that trend in dimensions being used for PCBs.
Hogan: Whether it’s feature size accuracy for high-frequency circuits—higher-resolution direct imaging produces more accurate feature sizes due to digitization—or the throughput you’re trying to achieve, the problems faced by the machine builder are pretty challenging. And that’s the broad range of customer base with which we work. If you’re dealing in high-volume markets in Asia, you’re constantly driven about throughput. So, can you move the digital imaging data through the system fast enough? The sheer volume of data movement starts to become an obstacle.
Johnson: Is that an even greater problem if you’re in a higher-mix situation?
Hogan: Yes. When you get to the high-resolution applications the expectation is less throughput when you’re doing one-micron features. We have advantages, though, because what high-resolution laser lithography systems can do in a few hours, we can do in a few minutes; however, it’s still very challenging. The throughput question is important, but it’s more about a technical capability rather than the throughput in a lot of cases.
Johnson: I see what you’re saying; it’s more about doing the imaging as fast as possible.
Hogan: Traditional semiconductor fabrication deploys steppers that reproduce a small image repeatedly on the wafer; we can image that entire 12-inch wafer as a panel, allowing a lot of design flexibility. It can be one complete circuit or an array of circuits; the direct-write technology allows for that. It’s a lot of data and capability. The circuit board side is an incredible market, but they’re all about efficiency, throughput, and high volume. By applying the principles of PCBs to microelectronics, we are positioned to handle a broad array of challenges from a different perspective.
Johnson: At this point, there’s development in direct imaging that is a turning point, especially for the PCB side. What should we know about direct imaging right now? What’s coming?
Hogan: The teachable moment for us was our relationship with the CHIPS Consortium at UCLA. This high-technology semiconductor research group is looking to the circuit board people for manufacturing methodologies because there are some unique issues; PCB methods are relevant to microelectronics and semiconductors, and the same is true the other way. The circuit board market could look at the semiconductor aspects and how they scale or the different thought processes they have; there’s a lot to glean. We’ve been in the middle of that, and we’re participating in industry groups on both the semiconductor and circuit board sides for many years.
We see commonality and a shift going on between the two markets. All of our circuit board machines have improved a great deal resulting from our work with the semiconductor applications. Cross-training among the groups could be very useful for most of our mutual clientele, in semiconductors or PCBs.
Johnson: What specifically should the PCB side be looking for in the form of new capabilities and approaches?
Hogan: Feature size control. There are some direct imaging systems that do come from imaging and are focused on the mechanical aspects, but can they control that feature size within a couple of microns everywhere on the panel? The performance of the circuit board is influenced by the precision of the imaging and the shape of the trace. It’s not enough to produce a trace that’s three mils wide. Does it have the right taper? Is it under control and repeatable?
With a lot of the technologies that we’ve introduced, like multi-wavelength control, we can control each of our wavelengths independently so that you can shape the trace. As frequencies get higher, the shape of the trace starts to influence the quality of the signal. Those are all drivers to the quality of the end product. With PCBs, too often, it’s price and throughput, such as “Can you get 100 panels out?” The focus isn’t as much on the result in circuit quality and the influence of that.
Johnson: That’s a completely different way of thinking for somebody who’s been working with PCBs. We have to start thinking about it in the way semiconductor has thought about it for years.
Hogan: The circuit board market is also tiered, and the companies with the most resources are already on the path to that. Those newly introduced to direct imaging have to become more educated. Those are the areas where the industry would benefit from a little more collaboration. Top to bottom, getting everybody to a more common standard in mentality and sharing expertise would be huge.
Johnson: While you’re creating this equipment that sits in the middle, what are the challenges for finding people who can help you?
Hogan: The staffing question is a challenge. Whether you’re talking about business development staffing or application engineering, you become a problem solver when you have new technology, and the ROI is pretty clean. We receive a lot of inquiries from radical thinking, whether it’s a chemical milling job where it wasn’t possible a year or two ago. We’re doing some interesting work in that segment. Having a staff member that is creative and has a broad enough knowledge to handle an application and think it through in an effective manner for the customer is important. The industry is aging, especially on the PCB side, so we’re trying to acquire young talent and get them the experience to think through these problems in a creative way.
Johnson: The PCB side might need more expertise than might be coming out of the semiconductor side; I’m thinking specifically about the pre-engineering phase. What is your assessment of those talent pools?Page 1 of 2
Suggested Items
Driving Innovation: Direct Imaging vs. Conventional Exposure
07/01/2025 | Simon Khesin -- Column: Driving InnovationMy first camera used Kodak film. I even experimented with developing photos in the bathroom, though I usually dropped the film off at a Kodak center and received the prints two weeks later, only to discover that some images were out of focus or poorly framed. Today, every smartphone contains a high-quality camera capable of producing stunning images instantly.
Hands-On Demos Now Available for Apollo Seiko’s EF and AF Selective Soldering Lines
06/30/2025 | Apollo SeikoApollo Seiko, a leading innovator in soldering technology, is excited to spotlight its expanded lineup of EF and AF Series Selective Soldering Systems, now available for live demonstrations in its newly dedicated demo room.
Indium Corporation Expert to Present on Automotive and Industrial Solder Bonding Solutions at Global Electronics Association Workshop
06/26/2025 | IndiumIndium Corporation Principal Engineer, Advanced Materials, Andy Mackie, Ph.D., MSc, will deliver a technical presentation on innovative solder bonding solutions for automotive and industrial applications at the Global Electronics A
Fresh PCB Concepts: Assembly Challenges with Micro Components and Standard Solder Mask Practices
06/26/2025 | Team NCAB -- Column: Fresh PCB ConceptsMicro components have redefined what is possible in PCB design. With package sizes like 01005 and 0201 becoming more common in high-density layouts, designers are now expected to pack more performance into smaller spaces than ever before. While these advancements support miniaturization and functionality, they introduce new assembly challenges, particularly with traditional solder mask and legend application processes.
Knocking Down the Bone Pile: Tin Whisker Mitigation in Aerospace Applications, Part 3
06/25/2025 | Nash Bell -- Column: Knocking Down the Bone PileTin whiskers are slender, hair-like metallic growths that can develop on the surface of tin-plated electronic components. Typically measuring a few micrometers in diameter and growing several millimeters in length, they form through an electrochemical process influenced by environmental factors such as temperature variations, mechanical or compressive stress, and the aging of solder alloys.