Successful Launch for Airbus’ Bartolomeo
March 10, 2020 | Airbus GroupEstimated reading time: 1 minute
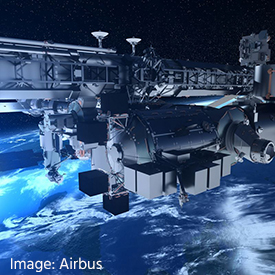
The Airbus-built Bartolomeo platform has been successfully launched on 06 March from Cape Canaveral, Florida. Bartolomeo is now on its journey to the International Space Station (ISS) and will be installed outside of the Columbus Laboratory, the European module of the ISS built by Airbus.
Andreas Hammer, Airbus’ Head of Space Exploration said, “This unique platform will offer new and affordable Earth observation applications and give companies and research institutions the unique opportunity to explore their project quickly and easily in space.”
Bartolomeo—named after Christopher Columbus' younger brother—is funded by Airbus and will be operated with the support of the European Space Agency (ESA). The platform can host up to 12 different payload slots, providing them with a power supply and data transmission back to Earth.
Not only does this provide opportunities for Earth observation, but also environmental and climate research, robotics, material sciences, astrophysics or to test new technologies in space, paving the way for their commercialisation. The platform’s unique vantage point 400 kilometres above the Earth offers unobstructed views of our planet enabling the hosting of external payload in low-Earth-orbit.
Launch opportunities are available on every servicing mission to the ISS which is around every 3 months. The payload accommodation allows slots for a wide range of payload mass going from 5 to 450 kg. They will be provided with optical data downlink capacity of one to two terabytes per day.
In just 12 months any payload can be prepared and ready to operate. Payload sizes, interfaces, preparation before launch and integration process are largely standardised. This reduces lead times and saves costs significantly compared to traditional mission costs.
Bartolomeo is an all-in-one mission service that pioneers sustainable space for a safe and united world.
Suggested Items
Specially Developed for Laser Plastic Welding from LPKF
06/25/2025 | LPKFLPKF introduces TherMoPro, a thermographic analysis system specifically developed for laser plastic welding that transforms thermal data into concrete actionable insights. Through automated capture, evaluation, and interpretation of surface temperature patterns immediately after welding, the system provides unprecedented process transparency that correlates with product joining quality and long-term product stability.
Smart Automation: The Power of Data Integration in Electronics Manufacturing
06/24/2025 | Josh Casper -- Column: Smart AutomationAs EMS companies adopt automation, machine data collection and integration are among the biggest challenges. It’s now commonplace for equipment to collect and output vast amounts of data, sometimes more than a manufacturer knows what to do with. While many OEM equipment vendors offer full-line solutions, most EMS companies still take a vendor-agnostic approach, selecting the equipment companies that best serve their needs rather than a single-vendor solution.
Keysight, NTT, and NTT Innovative Devices Achieve 280 Gbps World Record Data Rate with Sub-Terahertz for 6G
06/17/2025 | Keysight TechnologiesKeysight Technologies, Inc. in collaboration with NTT Corporation and NTT Innovative Devices Corporation (NTT Innovative Devices), today announced a groundbreaking world record in data rate achieved using sub-THz frequencies.
Priority Software Announces the New, Game-Changing aiERP
06/12/2025 | Priority SoftwarePriority Software Ltd., a leading global provider of ERP and business management software announces its revolutionary aiERP, leveraging the power of AI to transform business operations.
Breaking Silos with Intelligence: Connectivity of Component-level Data Across the SMT Line
06/09/2025 | Dr. Eyal Weiss, CybordAs the complexity and demands of electronics manufacturing continue to rise, the smart factory is no longer a distant vision; it has become a necessity. While machine connectivity and line-level data integration have gained traction in recent years, one of the most overlooked opportunities lies in the component itself. Specifically, in the data captured just milliseconds before a component is placed onto the PCB, which often goes unexamined and is permanently lost once reflow begins.