Multi-board Etching: Managing Rigid-Flex Designs and Conductivity
April 1, 2020 | Hemant Shah, Cadence Design SystemsEstimated reading time: 1 minute
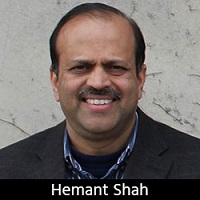
When I was a very young boy, my dad would delight and tease me by flexing his muscles. He did this with a very special flourish. Rather than simply flexing, he would put his thumb in his mouth, blow, and flex, which gave the appearance that huffing and puffing on his thumb made his bicep pop out. This was a great show for a little boy.
In PCB design, we work with a different type of flex. Advances in consumer and industrial electronic devices have allowed manufacturers to produce smaller devices that have more functionality.
Those devices use rigid-flex designs that provide the form factors needed for portability and—many times—include multiple interconnected boards. With all the interconnections between the boards, PCB designers pay equal attention to signal paths and to the electrical connectivity between boards. On the mechanical design side of things, each board must fit within an enclosure that meets the product specifications. As a result, every multi-board design combines electronic design automation (EDA) with mechanical engineering design (MCAD).
The Sum Is Greater Than the Whole
Good troubleshooting techniques involve considering a system as individual parts rather than as a whole. The same techniques apply to your work with multi-board PCB designs. Each board consists of a single unit that has its own lifecycle.
Some product designs may use a single PCB design for multiple functions or for multiple devices. Others may interconnect multiple PCB designs to produce a complete, fully functional system. Depending on the product design, a single PCB design may have multiple uses. No matter the method, the multi-design represents an overall approach to system design.
To read this entire article, which appeared in the February 2020 issue of Design007 Magazine, click here.
Testimonial
"Our marketing partnership with I-Connect007 is already delivering. Just a day after our press release went live, we received a direct inquiry about our updated products!"
Rachael Temple - AlltematedSuggested Items
New Episode Drop: MKS’ ESI’s Role in Optimize the Interconnect
08/21/2025 | I-Connect007In this latest episode, Casey Kruger, director of product marketing at MKS’ ESI, joins On the Line With… host Nolan Johnson to share how CO₂ laser technology delivers faster, more accurate vias in a smaller, more energy-efficient footprint.
PEDC Call for Abstracts Deadline Extended to Aug. 31
08/20/2025 | I-Connect007 Editorial TeamThe second Pan-European Electronics Design Conference (PEDC) will take place Jan. 21-22, 2026, in Prague, Czech Republic. The call for abstracts deadline has been extended to Aug. 31. Organized jointly by the German Electronics Design and Manufacturing Association (FED) and the Global Electronics Association (formerly IPC), PEDC serves as a European platform for knowledge exchange, networking, and innovation in electronics design and development.
Meet the Round 1 Winners of the Bright Manufacturing Student Challenge 2025
08/20/2025 | Tara Dunn, SMTAThe Bright Manufacturing Student Challenge is an opportunity for student teams to design and develop innovative solutions for real-world electronics manufacturing problems. The eight-week competition, sponsored by the Electronics Manufacturing & Assembly Collaborative (EMAC) through electronicsworkforce.com, allows students to showcase their technical skills, creativity, and problem-solving abilities.
University Of Minnesota Team Claims Victory In Bright Manufacturing Challenge 2025 Round 1
08/19/2025 | EMACThe Electronics Manufacturing & Assembly Collaborative (EMAC) recently announced that Team "Rise and Grind Crew" from the University of Minnesota has emerged victorious in Round 1 of the Bright Manufacturing Challenge 2025.
Happy’s Tech Talk #42: Applying Density Equations to UHDI Design
08/19/2025 | Happy Holden -- Column: Happy’s Tech TalkWith the need for faster speeds, more parts on an assembly, and the trend to make things smaller for portability, the printed circuit design and layout process is both creative and challenging. The process involves “applying the density equation” while considering certain boundary conditions, such as electrical and thermal performance. Unfortunately, many designers don’t realize there is a mathematical process to laying out a printed circuit.