The new products from Henkel address exactly these needs. Loctite ECI 7007 conductive carbon-ink, made for personal hygiene products, lays the foundation for smart diapers while ECI 8000 E&C series enables smart heating solutions for the smart home. Furthermore, stretchable Loctite conductive inks are able to be processed into the surface of an automotive interior, making it possible to integrate e.g. motion sensors, heating or charging devices directly via the smart surface.
Henkel Drives Smart Living, Mobility and Hygiene With Functional Material Solutions for Printed Electronics
April 2, 2020 | HenkelEstimated reading time: 4 minutes
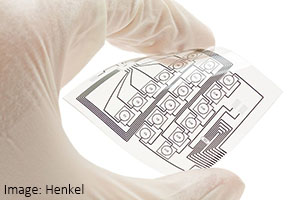
The digital transformation poses a variety of challenges to all industries. One of them is surely the pressure to leverage the potential of new technologies to enhance performance. At the same time, emerging technologies make new approaches possible: printed electronics evolve the traditional electronics in terms of efficiency and flexibility to open up completely new application fields, from personal hygiene products to smart surfaces for home or mobility applications. Being on top of this development, functional ink plays a key role in printed electronics, transforming a substrate into a conductive surface.
Printed Electronics: a game-changer for high volume applications
“While we see an increasing importance of technological innovations in our daily live, such as the Internet of Things or 5G, industries need to make sure, to keep up with these developments. As electronic components become more cost-efficient and processable in huge quantities, applicational fields multiply while new and evolved technologies open up completely new possibilities—such as printed electronics,” says Stijn Gillissen, Henkel Global Head of Printed Electronics. “Printed Electronics will impact a variety of industries—from living to hygiene to mobility—which are constantly confronted with new customer demands to become more innovative and digital. Particularly this technology can be the answer for manufacturers and converters especially—but not exclusively when it comes to FMCG.” Observing a shift from medium to high volume applications early, Henkel started to bring the technologies forward in order to leverage the full potential of printed electronics. “With functional ink being an integral part for printed electronics, Henkel is able to benefit this development with its expertise and broad range of functional material innovations.” explains Stijn Gillissen.
Making living and mobility smarter than ever before—with Loctite functional inks
With the Henkel Loctite ECI 7007 carbon-based ink Henkel provides a product to actively support the digitalization of the living and hygiene sector. It is made for high speed production and thus optimally suits the requirements in the processing of FMCGs. The highly flexible ink is able to be applied on a very thin substrate and functions as a conductor to a moisture sensor for smart diapers. The printed electronics solution detects moisture and informs the caregiver. “The innovations in our Loctite-range, optimized for printed electronics, offer various benefits for smart living. Smart diapers, empowered by Henkel functional ink, improve comfort for the wearer, increase caregivers’ efficiency and make the use of diapers more efficient and more sustainable as research implies a significant decrease of diaper use, since they will only be changed when needed,” summarizes Gillissen.
Another innovation for smart homes is empowered by Henkel’s conductive carbon PTC inks Loctite ECI 8000 E&C series. These inks can be printed on almost any surface to create a uniform, self-regulating heater that will never overheat. These very thin printed heaters offer designers new possibilities to integrate heating functionality in places they could not before. Heated surfaces in for example construction & furniture are now possible using this technology.
“The automotive sector is also an industry which is under the pressure to constantly innovate,” observes Gillissen “Henkel Adhesive Technologies supplies powerful solutions to bring the digitalization of cars one step ahead, as printed electronics make automotive interior smarter than ever before”. The stretchable Loctite conductive inks are able to be thermoformed perfectly matching the requirements of in-molded electronics, which are processed in automotive interiors. With this technology, automotive dashboards without buttons to press are possible: controlling temperature or infotainment via the smart surface.
Taking printed electronics to the next level—with strong partnerships
Printed electronic devices require a complex interplay of different components and technologies. Bringing the entire value-chain together, Henkel follows a partnership-approach that unites and connects producers and experts of all related fields.
Bare Conductive, for instance, is a partner for the development of product solutions in the field of smart surfaces. “Together with our partners like Henkel, we leverage class-leading materials science to make any surface smart, transforming what it means to make a smart home, a smart office, a smart city, or a smart car. Creating digital-transformation from unexpected places,” explains Matt Johnson, CEO & Co-Founder of Bare Conductive.
In cooperation with Quad Industries, specialized in manufacturing of printed electronics, and Byteflies, a wearable health startup, Henkel is developing smart health patches for people suffering from chronical illnesses. The electronic patches are able to monitor patient’s vital data in a less obtrusive way in their home environment thus significantly improving the patient comfort and improving medical treatments.
Additionally, Henkel builds on a partnership for material-supply with CHASM Advanced Materials, Inc., a supplier of innovative transparent conductive materials and inks, to further boost the company’s portfolio with respect to printed electronics.
“At Henkel we rely on a differentiated network of partners. Building on that network, we can provide our customers not only with our products and knowledge, but connections to e.g. circuit designers, printing manufacturers or external IoT-providers. Together we are able to leverage the potential of digital transformation across the entire value chain, utilizing the benefits of printed electronics,” summarizes Gillissen.
Suggested Items
North American EMS Industry Shipments Down 9.3% in May
06/20/2025 | IPCIPC announced the May 2025 findings from its North American Electronics Manufacturing Services (EMS) Statistical Program. The book-to-bill ratio stands at 1.43.
North American PCB Industry Sales Up 21.4% in May
06/20/2025 | IPCIPC announced the May 2025 findings from its North American Printed Circuit Board (PCB) Statistical Program. The book-to-bill ratio stands at 1.03.
Chiplets and the Like are Redefining Microelectronics
06/25/2025 | productronicaThe performance of modern AI and high-performance computing applications can only be achieved with high-performance semiconductor technology.
United Electronics Corporation Advances Manufacturing Capabilities with Schmoll MDI-ST Imaging Equipment
06/24/2025 | United Electronics CorporationUnited Electronics Corporation has successfully installed the advanced Schmoll MDI-ST (XL) imaging equipment at their advanced printed circuit board facility. This significant technology investment represents a continued commitment to delivering superior products and maintaining their position as an industry leader in precision PCB manufacturing.
STMicroelectronics Introduces Advanced Human Presence Detection Solution to Enhance Laptop and PC User Experience
06/24/2025 | STMicroelectronicsSTMicroelectronics, a global semiconductor leader serving customers across the spectrum of electronics applications, introduces a new Human Presence Detection (HPD) technology for laptops, PCs, monitors and accessories, delivering more than 20% power consumption reduction per day in addition to improved security and privacy.