Airbus Achieves World’s First Fully Automatic Refuelling Contacts
April 20, 2020 | Airbus GroupEstimated reading time: 1 minute
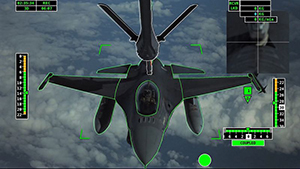
Airbus has achieved the first ever fully automatic air-to-air refuelling (A3R) operation with a boom system. The flight test campaign, conducted earlier in the year over the Atlantic Ocean, involved an Airbus tanker test aircraft equipped with the Airbus A3R solution, with an F-16 fighter aircraft of the Portuguese Air Force acting as a receiver.
This milestone is part of the industrialisation phase of A3R systems ahead of its implementation in the A330 MRTT tanker development.
The campaign achieved a total of 45 flight test hours and 120 dry contacts with the A3R system, covering the whole aerial refuelling envelope, as the F-16 and MRTT consolidate the maturity and capabilities of the development at this stage. The certification phase will start in 2021.
Didier Plantecoste, Airbus Head of Tanker and Derivatives Programmes, said: “The achievement of this key milestone for the A3R programme highlights the A330 MRTT’s excellent capability roadmap development and once more confirms that our tanker is the world’s reference for present and future refuelling operations. Our special thanks go to the Portuguese Air Force for their continued support and help on this crucial development”.
The A3R system requires no additional equipment on the receiver aircraft and is intended to reduce air refuelling operator (ARO) workload, improve safety and optimise the rate of air-to-air refuelling transfer in operational conditions, helping maximise aerial superiority. The goal for the A3R system is to develop technologies that will reach fully autonomous capabilities.
Once the system is activated by the ARO, the A3R flies the boom automatically and keeps the alignment between the boom tip and the receiver receptacle with an accuracy of a couple of centimeters; the proper alignment and the receiver stability is checked in real-time to keep a safe distance between the boom and the receiver and also to determine the optimum moment to extend the telescopic beam to achieve the connection with the receiver. At this point, the fuel transfer is initiated to fill up the receiver aircraft and once completed and the disconnection is commanded, the boom is cleared away from the receiver by retracting the telescopic beam and flying the boom away to keep a safe separation distance. During this process, the ARO simply monitors the operation.
Suggested Items
OSI Systems Lands $17 Million Order for Cargo and Vehicle Inspection Systems
07/07/2025 | BUSINESS WIREOSI Systems, Inc. announced that its Security division received an order valued at approximately $17 million from an international customer for cargo and vehicle inspection systems.
KYOCERA AVX Releases New 3DB Hybrid Couplers
07/04/2025 | PRNewswireKYOCERA AVX, a leading global manufacturer of advanced electronic components engineered to accelerate technological innovation and build a better future, released a new line of integrated thin film (ITF) hybrid couplers designed to facilitate the continued evolution of high-frequency wireless systems in industrial, automotive, telecommunications, and telemetry applications.
Accenture Acquires SYSTEMA to Drive Manufacturing Automation for Semiconductor Clients
07/02/2025 | AccentureAccenture has acquired SYSTEMA, a provider of software solutions and consulting services for manufacturing automation, headquartered in Dresden, Germany.
Driving Innovation: Direct Imaging vs. Conventional Exposure
07/01/2025 | Simon Khesin -- Column: Driving InnovationMy first camera used Kodak film. I even experimented with developing photos in the bathroom, though I usually dropped the film off at a Kodak center and received the prints two weeks later, only to discover that some images were out of focus or poorly framed. Today, every smartphone contains a high-quality camera capable of producing stunning images instantly.
Specially Developed for Laser Plastic Welding from LPKF
06/25/2025 | LPKFLPKF introduces TherMoPro, a thermographic analysis system specifically developed for laser plastic welding that transforms thermal data into concrete actionable insights. Through automated capture, evaluation, and interpretation of surface temperature patterns immediately after welding, the system provides unprecedented process transparency that correlates with product joining quality and long-term product stability.