MFLEX Increases Growth
April 24, 2020 | Happy Holden, I-Connect007Estimated reading time: 4 minutes
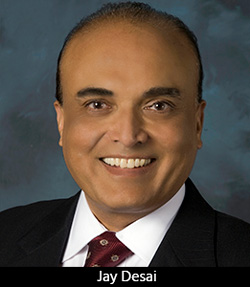
Happy Holden spoke with Jay Desai of MFLEX about the latest flex work the company has been doing and its aim to transition toward more automation and a smart factory approach.
Happy Holden: I have the pleasure of talking with my old friend and luminary, Jay Desai, from MFLEX. We’re going to get an update on what MFLEX has been up to the last few years.
Jay Desai: Thanks for inviting me for this interview, and thank you for our years of friendship and mentorship. Hopefully, like you, I will get the "IPC Dinosaur" pin one of these years soon. MFLEX has been in the flex manufacturing and assembly business since 1984. We’ve been around for 35 years. The company started in Anaheim, California, manufacturing bare flex circuits, and five years later started assembly on the flex circuits we were manufacturing. In 2004, we moved to Suzhou, China, and have been there ever since.
We have three manufacturing facilities in China. There are two in Suzhou: one is focused on bare flex manufacturing, and the other focused on assembly. Our third factory for both flex manufacturing and assembly was set up two years ago in a city called Yancheng, which is about three hours north of Suzhou.
It has been very interesting. MFLEX has been able to leverage our manufacturing capabilities from these three factories and provide local engineering and program management support to our customers globally. You can say, “We think globally, but act locally,” because that’s what customers really want, whether it is in the Americas, Europe, or Asia. Our core strength is to leverage our manufacturing in China along with the front-end engineering and program management support that customers globally desire.
Three years ago, we were acquired by our mother company, DSBJ, which is also based in Suzhou. Collectively, between DSBJ and MFLEX, we are one of the largest employers in Suzhou. After the acquisition, the focus was on capacity and capability expansion, which resulted in tremendous growth since 2017. This has been beneficial for us and our customers to take advantage of the capacity and the capability expansion. All of this has resulted in MFLEX now being in the top three leading global FPC suppliers, in terms of flex manufacturing and assembly.
Holden: For those of you that don’t know a lot of the history of flex circuits, during my time at Hewlett Packard, I essentially learned everything about flex circuits from MFLEX. MFLEX was significant in the design of the flex in HP calculators, and a lot of engineering value added there. When I came across them again while working for Foxconn, I found they again were contributing to modern mobile phones. People don’t recognize or realize how significant their engineering has been in the whole flex arena.
After the acquisition, I kind of lost track, especially with their vice president—Don Pucci. Don Pucci and I go back to his days at Digital Equipment Corporation (DEC) during the computer wars in the ‘70s and ‘80s, where it was Hewlett Packard versus DEC. Jay has been a flex man all along on the technical side of it.
Jay, what do you see for the future of MFLEX?
Desai: That’s a very good question, Happy. Thank you for your kind words. Flex is a big enabler for more applications and functionality to achieve miniaturization. Whether we talk about thinness, fine pitch, or high density, it’s very much adaptable with automation. One of the major efforts that have gone into the capacity and capability expansion over the last three years that I mentioned is a lot of automation. In the last decade, we’ve seen a lot more enabling applications with flex because of that thinness—especially in the consumer electronics products—and a variety of different mobility products, such as tablets, smartphones, smartwatches, and other wearables. That whole arena has really exploded for flex circuit applications. Now, especially with the advent of the 5G coming on board, we see a lot more applications driven by flex as well.
We are focusing very heavily, as you mentioned, on engineering activities targeting toward high-speed 5G applications and low-loss materials. A lot of effort in the area of materials technology development is on how to make these flex circuits more robust, and more reliable is the key. Another big thing that has happened is the automotive market, especially for newer applications for electric vehicles and battery management systems. Currently, we are doing flex circuits that are 2.2 meters long, and we think that there might be opportunities for making even longer flex circuits, like 2.5 or 2.6 meters, and do assembly on them. That’s a big challenge.
Holden: Are you continuing to work on the liquid crystal polymer film?
Desai: Yes. That’s one of the materials sets that we are looking at amongst others for the high-speed applications for lower insertion loss targeted for higher frequencies. That’s in the works.
Holden: We can expect next year to talk to you about what you’re rolling out for 5G or automotive. Do you have any final thoughts?
Desai: One other thing I did miss that I want to mention is we are working on smart factory initiatives for both the bare flex and the assembly facilities. Quite a bit of effort is being put into that. We have a roadmap that goes all the way out to 2025, which we refer to as the digital factory roadmap.
Holden: We’ll look forward to getting a progress report each year up to 2025 on the rollout of a digital factory for flex assembly, which is significant. Thank you for your time, Jay.
Desai: Thank you, Happy. I appreciate you having me.
Holden: This was enjoyable.
Testimonial
"In a year when every marketing dollar mattered, I chose to keep I-Connect007 in our 2025 plan. Their commitment to high-quality, insightful content aligns with Koh Young’s values and helps readers navigate a changing industry. "
Brent Fischthal - Koh YoungSuggested Items
Meet the Author Podcast: Martyn Gaudion Unpacks the Secrets of High-Speed PCB Design
07/16/2025 | I-Connect007In this special Meet the Author episode of the On the Line with… podcast, Nolan Johnson sits down with Martyn Gaudion, signal integrity expert, managing director of Polar Instruments, and three-time author in I-Connect007’s popular The Printed Circuit Designer’s Guide to... series.
Intervala Hosts Employee Car and Motorcycle Show, Benefit Nonprofits
08/27/2024 | IntervalaIntervala hosted an employee car and motorcycle show, aptly named the Vala-Cruise and it was a roaring success! Employees had the chance to show off their prized wheels, and it was incredible to see the variety and passion on display.
KIC Honored with IPC Recognition for 25 Years of Membership and Contributions to Electronics Manufacturing Industry
06/24/2024 | KICKIC, a renowned pioneer in thermal process and temperature measurement solutions for electronics manufacturing, is proud to announce that it has been recognized by IPC for 25 years of membership and significant contributions to electronics manufacturing.
Boeing Starliner Spacecraft Completes Successful Crewed Docking with International Space Station
06/07/2024 | BoeingNASA astronauts Barry "Butch" Wilmore and Sunita "Suni" Williams successfully docked Boeing's Starliner spacecraft to the International Space Station (ISS), about 26 hours after launching from Cape Canaveral Space Force Station.
KIC’s Miles Moreau to Present Profiling Basics and Best Practices at SMTA Wisconsin Chapter PCBA Profile Workshop
01/25/2024 | KICKIC, a renowned pioneer in thermal process and temperature measurement solutions for electronics manufacturing, announces that Miles Moreau, General Manager, will be a featured speaker at the SMTA Wisconsin Chapter In-Person PCBA Profile Workshop.