-
- News
- Books
Featured Books
- pcb007 Magazine
Latest Issues
Current IssueInventing the Future with SEL
Two years after launching its state-of-the-art PCB facility, SEL shares lessons in vision, execution, and innovation, plus insights from industry icons and technology leaders shaping the future of PCB fabrication.
Sales: From Pitch to PO
From the first cold call to finally receiving that first purchase order, the July PCB007 Magazine breaks down some critical parts of the sales stack. To up your sales game, read on!
The Hole Truth: Via Integrity in an HDI World
From the drilled hole to registration across multiple sequential lamination cycles, to the quality of your copper plating, via reliability in an HDI world is becoming an ever-greater challenge. This month we look at “The Hole Truth,” from creating the “perfect” via to how you can assure via quality and reliability, the first time, every time.
- Articles
- Columns
- Links
- Media kit
||| MENU - pcb007 Magazine
Estimated reading time: 6 minutes
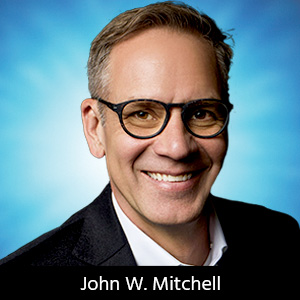
One World, One Industry: Separating Hype From Reality—What’s Next for the Future of Electronics?
As IPC looks to the future of the electronics industry to determine what services to develop in the areas of standards, education, and advocacy, we will rely on a newly created role at IPC—chief technologist—to assist us in that effort. Matt Kelly, a familiar face in IPC standards development and widely recognized in the global electronics industry as a thought leader and an innovator, was recently hired as IPC’s chief technologist. I sat down with Matt to ask him about his new role, as well as industry trends.
John Mitchell: When looking at something as broad as “the future of electronics,” how do you focus on what trends will be the most critical to supporting IPC members?
Matt Kelly: That’s a great question, John. As we can likely agree, predicting the future is a tough business—especially today, as emerging and disruptive technologies are rapidly evolving. To have a shot at getting this right, I focus on “cutting through the noise.” With so much information at our fingertips and so many technologies advancing at the same time, I concentrate on separating hype from reality. To do this, I rely on the engineering and business experience I’ve gained over the past 20 years in the electronics industry.
To ensure I identify critical trends for IPC members, I use a two-step approach. First, I leverage my network to understand what is most important, focusing on gathering critical “voice of the customer” (VOC) input from subject-matter experts and IPC members from around the world. Second, I examine promising trends through a business value lens. I focus on ROI value delivery by identifying real business issues and then applying appropriate solutions, including base operations management practices and new Industry 4.0 technologies as needed.
Mitchell: There is a great deal of interest in the “factory of the future,” implying that the current factory will be undergoing tremendous change soon. Can you explain what some of those changes might be and how they will affect the day-to-day operations of a factory?
Kelly: I first want to address timing expectations. We should expect a “factory of the future” transformation to be a gradual but steady transition with varying adoption levels by geography. In Europe, companies have been in-vesting and transforming since 2008 (e.g., Germany—the birthplace of Industry 4.0). Companies in Asia have been working since 2014 and are now leading the way with large scale implementation of new Industry 4.0 advancements. Adoption in North America is lagging but is critical in ensuring manufacturing competitiveness moving forward.
As for new advancements in electronics manufacturing factories, I see companies first in-vesting and implementing solutions in the following areas as they provide early ROI returns: digital transformation, secure cloud computing networks, and manufacturing operations/supply chain data analytics. This first group is likely to be followed by connected worker enhancement, cobot/robot automation, artificial intelligence/machine learning, and additive manufacturing.
Generally, these technologies are funded and implemented as individual solution blocks within a factory, as opposed to being installed as fully integrated end-to-end solutions. The main reason for this is the high CAPEX expense for new solutions. Thus, project-based installation is expected to continue.
From an employee perspective, as companies migrate to a factory of the future solutions, new technologies are not meant to fully replace the workforce; rather, these advancements will affect the workforce to change how they work. While there will be some level of workforce reduction, employees will be expected to upskill, be more versatile, and be responsible for several areas simultaneously. To do this, they will need to leverage data analytics, AI insights, and automation to help them manage many more activities in a day.
Mitchell: You most recently worked at IBM in Toronto as a senior technical staff member and master inventor, and you are widely published in technical publications. How do you see your creative background informing the work you will do as IPC’s chief technologist?
Kelly: Engineers are notorious for their bad spelling and reluctance to write things down. They would rather be spending their time solving problems and developing new solutions. Early in my career, I was taught by my research supervisor at 3M a very important lesson, which I still use as guidance today: “Communication is the most important part of being an engineer. At the end of the day, if you don’t write down what you’ve learned or observed, then you have nothing to pass along to others.” I have never forgotten this advice, and it is the reason why I have written over 80 technical publications and 25 patent disclosures to the industry.
Moving forward as IPC’s chief technologist, I plan to continue writing and communicating. I plan to work with trade publishers, issue IPC position papers to industry and government bodies, issue state-of-technology reports, and present at various trade shows and conferences around the world. The intent is to increase IPC’s technical strength and visibility within the industry and our membership.
Mitchell: Part of your role will entail industry intelligence and the launch of an industry Chief Technologist Council (CTC). Can you explain what each of those initiatives will cover and how they will affect the industry and IPC members in particular?
Kelly: The CTC is a collection of the electronic industry’s top technology leadership spanning OEM, EMS, and PCB companies. Members consist of CTOs, engineering VPs, directors, fellows, distinguished engineers, senior technical staff, and chief engineers. Quarterly meetings will be held throughout the year, discussing various technology and “factory of the future” topics. The intent of the Council is to obtain VOC input, keep a pulse on the industry, and continuously monitor IPC member key plans regarding electronics manufacturing technology needs. Insights will be gathered and reported periodically to various IPC bodies. Council contributions will help shape IPC strategic direction and external communications to the industry moving forward. The CTC will hold its first kick-off meeting in Q2 of 2020, pending CO-VID-19 recovery.
Mitchell: You’ve been deeply involved in IPC standards development, serving on several committees and earning a Rising Star Award for your efforts. What will your role be with committees now that you are on staff at IPC?
Kelly: As I’ve just come from industry, I’ll leverage my network built over the past 20 years to obtain industry feedback and drive adoption of key technology standards moving forward. I will continue to be involved in IPC standards and council development, with a shift in focus toward new “factory of the future” technology standards. We are currently working on defining a new “factory of the future” standards category, which will include the following areas. It’s a mix of brand new and existing standards as a grouped offering (Table 1).
Mitchell: We hear so much about standards and education addressing reliability and quality. From your vantage point, what are the similarities and differences between those two terms?
Kelly: Reliability and quality are related; how-ever, there are important differences. The terms are similar in the fact that they are used to mea-sure the “goodness” of a product (or service). Both are linked; we can ensure reliability by controlling quality. Both need to be assessed—not one instead of the other. The reason for this is that quality and reliability measure product “goodness” at different periods in time. Quality is measured as-built before initial use. However, reliability is measured during/after use. Think of quality as present-day and reliability as later in the future.
Quality is a static measure of a product meeting its specification as manufactured, whereas reliability is a dynamic measure of product performance. Quality is observed, whereas re-liability is experienced. As a consumer, you buy based on quality. You come back and buy again based upon reliability.
This column originally appeared in the May 2020 issue of PCB007 Magazine, click here.
More Columns from One World, One Industry
One World, One Industry: IPC APEX EXPO 2025 Marks a Special Anniversary YearOne World, One Industry: Mapping the Future of the Electronics Workforce
One World, One Industry: Mastering Technology Prognostication
One World, One Industry: To Thrive, Surround Yourself with Good People
One World, One Industry: Sustainability Challenges—A Collaborative Approach
One World, One Industry: What’s Next Becomes Now at IPC APEX EXPO 2024
One World, One Industry: ‘Blocking and Tackling’ During Tough Economic Times
One World, One Industry: Developing Your Team to Become Great Implementors