The iNEMI 2019 Roadmap: Flexible Hybrid Electronics
June 4, 2020 | Pete Starkey, I-Connect007Estimated reading time: 4 minutes
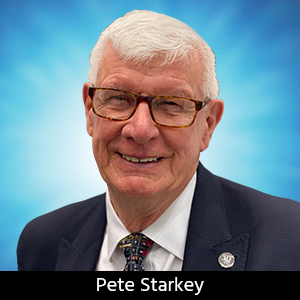
The emerging trend for “electronics on everything, everything with electronics” was the theme of iNEMI’s webinar presentation of the highlights of its recently published Flexible Hybrid Electronics Roadmap Chapter, delivered by Girish Wable, senior engineering services manager with Jabil. The session was introduced by Grace O’Malley, iNEMI vice president of global operations, who described the International Electronics Manufacturing Initiative as an industry-led, not-for-profit, R&D consortium of approximately 90 leading electronics manufacturers, suppliers, associations, government agencies, and universities engaged in roadmapping the future technology requirements of the global electronics industry; they identify and prioritise technology and infrastructure gaps and help to eliminate them through timely deployment projects.
Girish Wable explained that the concept of flexible hybrid electronics was a combination of technologies that integrated packaged SMT components and bare silicon dice with printed traces and printed functional devices into systems that could bend, fold, stretch, and conform while preserving the full operational integrity of traditional electronic architectures. Value drivers were the ability to make thinner, more flexible, possibly stretchable, and more functional interfaces to develop comfortable, compliant, and easy-to-use devices and, in the context of the industrial internet of things (IIoT), to distribute and deploy these sensors and to collect and communicate their data over a wide area. As well as opportunities to consolidate bills of materials, reduce weight, and simplify assembly steps, one of the principal cost drivers was the possibility of incorporating electronics in the physical materials from which products were made: textiles, glass, rigid plastics, and flexible and stretchable polyester and polyurethane films, for example. Prospective applications in printed electronics were stimulating the development of novel inks for creating functional circuits, devices, and components.
Wable described a practical approach to realising the value and helping to enable the cost benefits of flexible hybrid electronics: “Printing what you can, then integrating or placing what you cannot, depending on the level of maturity for each technology, the availability of each technology, and the associated cost.” Although such assemblies were inevitably a compromise, the benefits of flexible printed electronics could be realised whilst retaining the processing capability of conventional circuits.
Wable illustrated a progression from a conventional assembly of surface-mount packaged sensors and processors attached to plated copper traces on an FR-4 substrate through surface-mount packaged sensors and processors attached to printed silver or plated copper on a flexible substrate, shown as part of a shirt-sleeve, to a more complex assembly of thin-die and bare-die processors integrated with a variety of printed features, such as traces, antennae, sensors, batteries, and indicators—all on a flexible substrate. Listing some examples of the market pulling the technology versus the technology pushing the market, Wable commented that recent events might boost interest in flexible hybrid electronics platforms for low- or no-touch applications for remote monitoring and human-machine interfaces.
This chapter of the roadmap covered device categorisation, material and device performance, design tools, production methods, system integration, product reliability, and product life cycle. It highlighted key areas that required additional effort to accelerate the growth and establishment of the flexible hybrid electronics ecosystem. Its scope included flexible, stretchable, and conformal substrates; stretchable direct-deposited conductors and active surfaces, traces, devices, and components; low-temperature component-attachment materials; incorporation of SMT and ultra-thin integrated-circuit components; integration into products; and encapsulation. The chapter reviewed commercial developments and the status of standardisation, and summarised activities in the U.S., Canada, Europe, Singapore, China, Taiwan, Japan, Korea, and India.
It also included a section on design challenges, workflows, and methodologies. Whereas it had previously been necessary for assemblers to use workarounds, digital design tools were becoming available with the seamless capability for functional design, simulation, and verification for both conventional silicon and ultra-thin flexible silicon electronics. Design automation was a critical enabler for flexible hybrid electronics, along with design guidelines and standards.
Other critical enablers were improved materials to cost-effectively achieve increased conductivity and functionality with improved manufacturing consistency, together with low-cost thermally and dimensionally stable substrates and low-temperature interconnect and encapsulation materials. It was vital to secure supply-chain continuity for ultra-thin silicon dice and to develop equipment capable of high-yield high-volume assembly as well as reliable inspection and test.
Wable also discussed other project considerations. Successful acceleration in the development and adoption of flexible hybrid electronics would depend on the acceptability of value versus cost, the availability of automated design and simulation tools, and the effective qualification of materials and manufacturing equipment. Further objectives would be to achieve consensus on workflow architectures for hybrid approaches to develop characterisation tools for inspection and test and establish acceleration factors for correlating reliability. He acknowledged the contributions of the many collaborators world-wide to the content of the chapter.
Flexible hybrid electronics technology may be at a relatively early stage of development but continues its evolution as an alternative to conventional silicon electronics for an enormous range of existing and potential applications. The technology can combine the benefits of low-cost printed electronics and high-performance ultra-thin silicon devices with plastic film substrates and low-cost high-throughput manufacturing methods to offer opportunities for innovative designs in biomedical monitoring, IIoT and automotive sensors, smart packaging, and myriad consumer electronics applications. Advances in electrical, electronic, and optical functional ink; semiconductor materials processes; and organic light-emitting diode and organic photovoltaic technologies—together with the availability of low-temperature attach materials and alternative circuit fabrication techniques on flexible plastic, glass, and textile substrates—will continue to add to the scope of flexible hybrid electronics developments.
This iNEMI 2019 Roadmap webinar provided an enlightening and informative insight into what can be achieved by imaginative integration of low-cost printed electronics and high-performance silicon devices on flexible and stretchable substrate materials, as well as the enormous scope for continuing development of the concept in the coming decade. Further information can be found on iNEMI’s website.
Testimonial
"Our marketing partnership with I-Connect007 is already delivering. Just a day after our press release went live, we received a direct inquiry about our updated products!"
Rachael Temple - AlltematedSuggested Items
PEDC Call for Abstracts Deadline Extended to Aug. 31
08/20/2025 | I-Connect007 Editorial TeamThe second Pan-European Electronics Design Conference (PEDC) will take place Jan. 21-22, 2026, in Prague, Czech Republic. The call for abstracts deadline has been extended to Aug. 31. Organized jointly by the German Electronics Design and Manufacturing Association (FED) and the Global Electronics Association (formerly IPC), PEDC serves as a European platform for knowledge exchange, networking, and innovation in electronics design and development.
Nano Silver Inks Market Forecast Report 2025-2030
08/20/2025 | Globe NewswireThe Nano Silver Inks Market is expected to grow from USD 427.415 million in 2025 to USD 836.160 million in 2030, at a CAGR of 14.36%.
VVDN Expands Manufacturing Footprint into the UAE to Meet Global Demand
08/20/2025 | PRNewswireVVDN Technologies, a global provider of software, product engineering and electronics manufacturing services & solutions, today announced it is setting up a new manufacturing facility in the UAE as part of its global expansion strategy.
Kimball Electronics Veterans ERG Members Proudly Participate in the 5th Annual Honor and Remember Run
08/20/2025 | Kimball ElectronicsVeterans and Military Service Advocacy (VMSA) Employee Resource Group (ERG) members Michael Mosher (Database Administration Engineer), Michael Stone (Test Technician Team Lead), and Joshua Belcher (Application Development Manager) took part in the 5th Annual Honor & Remember Run, a meaningful event dedicated to honoring fallen service members. The race featured a powerful memorial wall constructed from dog tags.
Meet Incap UK at the Electronic Component Show 2025
08/20/2025 | IncapIncap UK is pleased to be exhibiting at the Electronic Component Show 2025. This one-day event will take place on 18 September at the Kassam Stadium in Oxford, bringing together design engineers, purchasing professionals, manufacturers, distributors, and service providers to discover new products, solutions, and contacts. You will find us at stand 52.