ATS Extrusion Profile Heat Sink Solutions Offer Cost-Effective Flexibility
June 9, 2020 | New Yorker Electronics Co.Estimated reading time: 1 minute
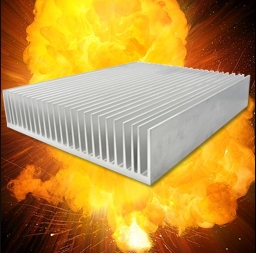
New Yorker Electronics has announced the global distribution of the newly expanded line of Heat Sink Extrusions from Advanced Thermal Solutions (ATS). The Extrusion Profiles series is comprised of aluminum alloy, the most cost-effective solution for the majority of electronic cooling applications.
The standard bar length is 300mm for easier design prototype manufacturing, however ATS maintains a vast inventory of profiles in a wide variety of sizes. In addition, engineers and designers can cut the extrusion bar to the appropriate heat sink design. This also works particularly well for MIL applications that cannot reveal project details. The ATS Extrusion Profile series is also well-matched to Altera, AMD, Freescale, Intel, TI and Xilinx applications.
The Extrusion Profiles are available in Straight Fin, STAR LED and Linear LED designs and custom finishes (anodization) available upon request. Other types of Heat Sink Extrusions from ATS include Straight Fin Extrusions, Slant Fin Extrusions, Pin Fin Extrusions and LED Extrusions. These high aspect ratio heat sinks are ideal for applications where there is adequate airflow to take optimum advantage from these designs.
ATS also offers an array of heat sink extrusion profiles with different thermal performances, fin-to-fin spacing, lengths and heights. Extrusion profiles enable engineers to either select or start their design from a pre-tooled extrusion profile for the cooling solution. There is no MOQ and no NRE required; so for standard extrusion profile or design expertise, New Yorker Electronics is able to fulfill orders quickly.
Suggested Items
Material Selection and RF Design
04/21/2025 | Andy Shaughnessy, Design007 MagazineInnovation rarely sleeps in this industry, and the RF laminate segment offers a perfect example. RF materials have continued to evolve, providing PCB designers much more than an either/or choice. I asked materials expert Alun Morgan, technology ambassador for the Ventec International Group, to walk us through the available RF material sets and how smart material selection can ease the burden on RF designers and design engineers.
Real Time with... IPC APEX EXPO 2025: Aster–Enhancing Design for Effective Testing Strategies
04/18/2025 | Real Time with...IPC APEX EXPOWill Webb, technical director at Aster, stresses the importance of testability in design, emphasizing early engagement to identify testing issues. This discussion covers the integration of testing with Industry 4.0, the need for good test coverage, and adherence to industry standards. Innovations like boundary scan testing and new tools for cluster testing are introduced, highlighting advancements in optimizing testing workflows and collaboration with other tools.
Real Time with... IPC APEX EXPO 2025: Emerging Trends in Design and Technology
04/16/2025 | Real Time with...IPC APEX EXPOAndy Shaughnessy speaks with IPC design instructor Kris Moyer to discuss emerging design trends. They cover UHDI technology, 3D printing, and optical data transmission, emphasizing the importance of a skilled workforce. The role of AI in design is highlighted, along with the need for understanding physics and mechanics as designs become more complex. The conversation concludes with a focus on enhancing math skills for better signal integrity.
Electronic System Design Industry Posts $4.9 Billion in Revenue in Q4 2024
04/15/2025 | SEMIElectronic System Design (ESD) industry revenue increased 11% to $4,927.3 million in the fourth quarter of 2024 from the $4440.9 million reported in the fourth quarter of 2023, the ESD Alliance, a SEMI Technology Community, announced in its latest Electronic Design Market Data (EDMD) report.
Connect the Dots: Involving Manufacturers Earlier Prevents Downstream Issues
04/17/2025 | Matt Stevenson -- Column: Connect the DotsIf you have read any of my earlier columns, you know I am passionate about helping designers design for the reality of manufacturing. Designing for manufacturability (DFM) is a team sport. DFM is a design process that looks forward to the manufacturing process and integrates with it so that manufacturing requirements and capabilities can be accurately reflected in the design work.