-
- News
- Books
Featured Books
- pcb007 Magazine
Latest Issues
Current IssueThe Hole Truth: Via Integrity in an HDI World
From the drilled hole to registration across multiple sequential lamination cycles, to the quality of your copper plating, via reliability in an HDI world is becoming an ever-greater challenge. This month we look at “The Hole Truth,” from creating the “perfect” via to how you can assure via quality and reliability, the first time, every time.
In Pursuit of Perfection: Defect Reduction
For bare PCB board fabrication, defect reduction is a critical aspect of a company's bottom line profitability. In this issue, we examine how imaging, etching, and plating processes can provide information and insight into reducing defects and increasing yields.
Voices of the Industry
We take the pulse of the PCB industry by sharing insights from leading fabricators and suppliers in this month's issue. We've gathered their thoughts on the new U.S. administration, spending, the war in Ukraine, and their most pressing needs. It’s an eye-opening and enlightening look behind the curtain.
- Articles
- Columns
- Links
- Media kit
||| MENU - pcb007 Magazine
Just Ask Happy: The Proper Order of Design Techniques to Improve Connectivity
June 23, 2020 | I-Connect007 Editorial TeamEstimated reading time: Less than a minute
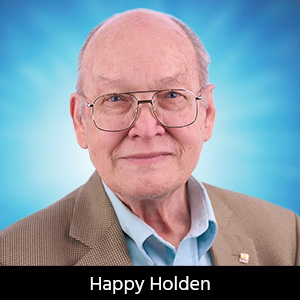
We asked for you to send in your questions for Happy Holden, and you took us up on it! The questions you've posed run the gamut, covering technology, the worldwide fab market, and everything in between.
Here is a question that relates to a topic near and dear to Happy's heart: improving connectivity.
Q: There are usually several ways to improve connectivity on any board (including HDI boards). But are there any general principles for which order these features should be added to achieve the best results?
A: From a connectivity and density improvement standpoint, the use of blind vias (either drilled or lasered) offers the greatest gain, especially since the pitch of active components that drives density is shrinking. Next is the reduction of the diameter of via holes and smaller annual rings. Reducing traces and spaces comes next if you do not run into impedance and signal losses, and then blind vias. The final step is adding more layers.
To pose a question for Happy Holden, take the survey by clicking here.
Suggested Items
Global PCB Connections: The Future of HDI PCBs
01/16/2025 | Jerome Larez -- Column: Global PCB ConnectionsHigh-density interconnect (HDI) printed circuit boards (PCBs) transform modern electronics by providing increased functionality, reduced sizes, and enhanced performance in complex designs. They do so by using advanced techniques, such as finer line and space definitions, microvias, and additional board layers. Specialized via structures—namely blind, buried, and stacked vias—offer complex routing while conserving space. This allows for the development of highly compact electronic devices. This article delves into HDI PCB technology, the function and benefits of blind, buried, and stacked vias, and their impact on PCB performance and design.
Quiet Power: An Evolution in PCB Design Costs
09/04/2024 | Istvan Novak -- Column: Quiet PowerIn this column, I want to cover my experiences, particularly where costs are concerned, with printed circuit boards from the 1960s to the present day. I grew up in an apartment building in downtown Budapest, where I began doing hobby projects building circuits from our kitchen table. Now, I’m lecturing about the most recent advances in signal integrity at Oxford University. We’ve come a long way. Over the decades, new technologies allowed users to have more layers, lower-loss dielectrics, fine-pitch surface connections, blind and buried vias, and HDI and HDI+ board constructions that allow us to design higher-performing systems. I expect this trend to continue.
Trouble in Your Tank: Processes to Support IC Substrates, Advanced Packaging—Part 1
03/07/2023 | Michael Carano -- Column: Trouble in Your TankThere has been much written and discussed over the last 18 months relating to semiconductor fabrication and the well-founded concerns that the U.S., in particular, has fallen behind in domestic chip manufacturing. In response to this issue, the United States government has enacted the CHIPS for America Act. Funding under this legislation is designed to drive more chip fabrication domestically. While this is all fine and good, once these advanced chips are manufactured, where will they go? As has been said ad nauseum, “Chips don’t float.”
A Challenge Facing Aerospace Designers In 2023
01/24/2023 | Lee Ritchey, Speeding EdgeAs the aerospace industry has been tasked with fitting increasingly complex electronics in existing airframes the demands on PCB substrates have begun to overtask the existing state of the art in PCB fabrication. Recently, I was called in to troubleshoot some reliability problems with a very dense PCB that had components on both sides and required the use of stacked blind vias and buried vias. The usual name for this kind of design is “build-up fabrication,” requiring many trips through the lamination, drilling, and plating operations at a fabricator.
PCB Plating Still Comes Down to Physics
06/21/2022 | I-Connect007 Editorial TeamWe asked columnist Michael Carano to discuss the latest innovations in plating equipment and chemicals, as well as some of the drivers in this segment, and the biggest challenges and opportunities he sees in plating today. As Michael points out, despite all of the technological advances in this industry, process engineers still need a solid understanding of Faraday’s Law and Ohm’s Law to successfully plate PCBs.