-
- News
- Books
Featured Books
- pcb007 Magazine
Latest Issues
Current IssueInventing the Future with SEL
Two years after launching its state-of-the-art PCB facility, SEL shares lessons in vision, execution, and innovation, plus insights from industry icons and technology leaders shaping the future of PCB fabrication.
Sales: From Pitch to PO
From the first cold call to finally receiving that first purchase order, the July PCB007 Magazine breaks down some critical parts of the sales stack. To up your sales game, read on!
The Hole Truth: Via Integrity in an HDI World
From the drilled hole to registration across multiple sequential lamination cycles, to the quality of your copper plating, via reliability in an HDI world is becoming an ever-greater challenge. This month we look at “The Hole Truth,” from creating the “perfect” via to how you can assure via quality and reliability, the first time, every time.
- Articles
- Columns
- Links
- Media kit
||| MENU - pcb007 Magazine
Estimated reading time: 4 minutes
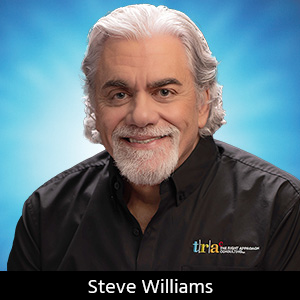
The Right Approach: Guerilla Tactics to Pass Any QMS Audit, Part 3
Continuing the series, “Guerilla Tactics to Pass Any QMS Audit,” I share Tactic 9. Hopefully, you are finding a number of solid strategies you can apply immediately to improve your audit success.
Guerrilla Tactic 9: Documentation Tips To Avoid Audit ‘Dings’
Williams’ Law 9: Teach it, preach it, and audit to it. Prepare so that no question should be able to be asked that an operator does not know the answer to.
Williams’ Law 9.1: If you can’t prove it, it didn’t happen!
Williams’ Law 9.2: The ONE time a supervisor asked someone else to sign for them, the auditor will find it.
Tip 1: KISS: “Keep it simple, Steve.”
The goal is to develop a system that:
- Is effective
- Is easy to understand
- Is flexible
- Minimizes opportunity for error
- Is simple
Tip 2: Standardization
Develop a standardized procedure template. Standardized sections might include the following:
- Responsibilities Section 2.0
- Quality Requirements Section 3.0
- Operations Section 5.0
- PM Section 7.0
- Forms Appendix A
This standardization should facilitate:
- Ease-of-use
- Training
- Recall
- Memorization of structure, not procedure
- Time-to-retrieval
Tip 3: Verbiage
Consider verbiage as follows:
- Functional vagueness
- Precise enough for functionality
- Vague enough for practicality
- Shall/must
- Critical
- Non-compliance would jeopardize operation
- Should/may
- Non-critical
- Non-compliance would not jeopardize operation
- Leaves room for external circumstances
- Examples
- “Bath pH shall be verified and logged onto form 203-004 every two hours.”
- “Workplace should be kept clean on a continual basis.”
Further, always use the term “designee.” For example:
- Don’t: “The molding supervisor shall review and sign-off on the daily SPC results.”
- Do: “The molding supervisor, or his/her designee, shall review and sign-off on the daily SPC results.”
Tip 4: Intelligent Conventions
If you are certified to an international QMS standard, such as ISO 9001 or AS9100, now that the powers that be have “harmonized” the standards, it is a great idea to number your system to align with the standard. For example, procedures, work instructions, forms, and attachments are numbered using the following number scheme with the prefix representing the type of document:
- QM: Quality manual
- QP: QMS procedure
- XX: Manufacturing work instruction (XX=department abbreviation)
- F=Form
- A=Attachment
Some examples include:
- The internal audit procedure that relates to section 9.2 is numbered as QP-920
- F-920-1 is the first form for the internal audit procedure QP-920
- Work instructions can start with WI, a three-digit department code, and a sequential number (e.g., WI-DRL-1=first work instruction for the drill department)
- Same format for forms (WI-DRL-1-1=first form for WI-DRL)
This makes it easy to identify all forms associated with each procedure or work instruction. Also, try to avoid an automatic sequential numbering scheme (QP 102345C) and large procedure numbers.
Tip 5: Reference Documents
Add a “reference documents” section to every procedure:
- Easy form maintenance
- Facilitates training
- Do not include form revision
- Reduces time-to-retrieval
- Assists in revision purge
- Helps maintain system integrity
Tip 6: Purge Control
Develop a control mechanism for revision purges. Don’t take a “hands-off” approach and assume individual departments will effectively purge.
Tip 7: Keep Six Months of Quality Records at the Work Source
Have posted procedures at the work source (paper or electronic). For instance, a 3” binder will easily hold 180 pages (six months). This allows quick and easy access and retrieval, calibrates with six-month surveillance audits, and provides finite history to verify.
Tip 8: ‘Outlaw’ White-Out
Do not allow White-Out in the facility. You can write exceptions into document control procedures for correspondence if absolutely necessary. Have a “controlled substance” mentality; it’s a simple matter of discipline. Teach “line, sign, date” (LSD) and audit to it internally
Tip 9: Eliminate Blanks
Issue edict: No forms shall have blanks. If a form has a section no longer used, remove it and revise the form. For instance:
- Infrequent non-use, line through, or “N/A”: Write clause into the document control procedure
- Blanks throw up red flags that something required wasn’t completed and make it difficult to defend missing information
Tip 10: Include All Forms
All forms should be included in the document control system (manufacturing, office, etc.). Preventive maintenance forms/logs are often overlooked and should be posted at the equipment and highly visible. Forms are quality records, and you would be hard-pressed to find an example that doesn’t contribute to the quality of the product in some form or another.
Tip 11: Resolve All Temporary Process Changes
Use three-month or six-month durations to sync with ISO surveillance audits. Try to resolve all TPCs prior to surveillance audits. If they can’t, or for customer audits, review the entire list of TPCs to make sure they are not expired. Also, verify that all resolved TPCs have been closed out appropriately (i.e., approved with appropriate procedure revision and unapproved with documented reason).
Tip 12: Procedure Revision
Procedure revisions show an auditor that continuous improvement is happening. A red flag to most auditors are procedures that were written five years ago and have not been revised since. For example:
- Preference: Annual procedure revision for a sample of procedures
- Acceptable: Touch all procedures at least once every three years
Don’t forget forms that may need revision accordingly, and don’t go overboard on revisions. Use a temporary process change process to combine multiple small changes.
Conclusion
It is my desire that as we work through the various strategies, techniques, and tactics presented throughout this series, you will appreciate these are tried-and-true, practical applications and lessons learned over the course of my career. I hope you will find some value in them.
This column originally appeared in the June 2020 issue of PCB007 Magazine.
More Columns from The Right Approach
The Right Approach: ‘Twas the Night Before Christmas (Harley-style)The Right Approach: I Hear the Train A Comin'
The Right Approach: Culture Change is Key to a QMS
The Right Approach: Leadership 101—Be a Heretic, Not a Sheep
The Right Approach: Leadership 101—The Law of Legacy
The Right Approach: Leadership 101: The Law of Explosive Growth
The Right Approach: Leadership 101—The Law of Timing
The Right Approach: The Law of Sacrifice