AOTCO Awarded ISO 13485 Certification
July 20, 2020 | PR NewswireEstimated reading time: 1 minute
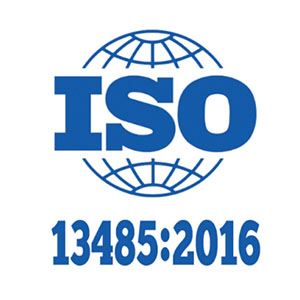
AOTCO Metal Finishing, a leading national provider of specialty surface finishing services, announces that it has been awarded ISO 13485:2016 certification. Achieving certification under this internationally recognized standard signifies that AOTCO's quality system meets the strict regulations and demanding requirements of the medical device industry.
"ISO 13485 has been widely requested by our medical industry clients, who would like to collaborate with AOTCO across a wider range of projects," said Matt Smith, AOTCO's President.
While AOTCO has supported medical manufacturers for years, its medical business has grown in importance during the COVID-19 epidemic. "Many of our clients were scrambling to deliver critical, life-saving equipment as part of the national medical emergency response," Smith explained. "So, we ramped up production and set aside dedicated capacity for high-priority jobs such as components for ventilators and other hospital equipment."
Delivering time-sensitive jobs is nothing new for AOTCO. In fact, the company's name is an acronym for the "Always On Time Company." Founded in 1975, AOTCO provides specialty metal finishing services – such as electroplating, anodizing, and passivation – to leading companies in advanced technology industries such as aerospace, medical, and optical. Over the years, AOTCO has developed a reputation for innovative solutions and exceptional quality – especially on complex jobs requiring selective plating, multi-material plating, or finishing of exotic materials such as beryllium.
In addition to ISO 13485, AOTCO also holds merit-status certification under NADCAP, the aerospace and defense contractor accreditation program. "The fact that we hold both NADCAP and ISO 13485 gives our customers the assurance that they are dealing with a top quality plater," Smith said. "If you have a job that needs to be done right and done on time – or if you have a job that is proving challenging for other platers – AOTCO is the place to call."
Suggested Items
Moog Announces Acquisition of COTSWORKS
07/07/2025 | BUSINESS WIREMoog Inc., a worldwide designer, manufacturer and systems integrator of high-performance precision motion and fluid controls and control systems, announced the acquisition of COTSWORKS Inc., an aerospace and defense fiber optics transceiver component manufacturer, for a purchase price of $63 million.
S&K Aerospace Awarded Major Contract Under DLA Maritime Acquisition Advancement Program
07/02/2025 | BUSINESS WIRES&K Aerospace, LLC has been awarded a significant contract under the Defense Logistics Agency’s (DLA) Maritime Acquisition Advancement Program, managed by the U.S. Naval Supply Command - Weapon Systems Support (NAVSUP WSS) in Mechanicsburg, PA.
Green Circuits to Exhibit Full-Service Electronics Manufacturing Solutions at 2025 SMD Symposium
07/02/2025 | Green CircuitsGreen Circuits, a full-service Electronics Manufacturing Services (EMS) partner to leading OEMs, is pleased to announce its participation in the 2025 SMD Symposium, taking place August 5-7 at the Von Braun Center in Huntsville, Alabama.
I-Connect007 Editor’s Choice: Five Must-Reads for the Week
06/27/2025 | Nolan Johnson, I-Connect007While news outside our industry keeps our attention occupied, the big news inside the industry is the rechristening of IPC as the Global Electronics Association. My must-reads begins with Marcy LaRont’s exclusive and informative interview with Dr. John Mitchell, president and CEO of the Global Electronics Association. For designers, have we finally reached the point in time where autorouters will fulfill their potential?
Knocking Down the Bone Pile: Tin Whisker Mitigation in Aerospace Applications, Part 3
06/25/2025 | Nash Bell -- Column: Knocking Down the Bone PileTin whiskers are slender, hair-like metallic growths that can develop on the surface of tin-plated electronic components. Typically measuring a few micrometers in diameter and growing several millimeters in length, they form through an electrochemical process influenced by environmental factors such as temperature variations, mechanical or compressive stress, and the aging of solder alloys.