Dale Smith and David Moody: Lenthor Pushing Limits of Flex Technology
July 21, 2020 | Andy Shaughnessy, Design007 MagazineEstimated reading time: 5 minutes
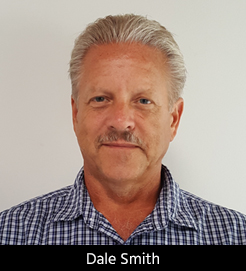
Andy Shaughnessy recently spoke with Dale Smith and David Moody of Lenthor Engineering. Dale is Lenthor’s new chief technology officer, and David is the director of sales/marketing.
In this interview, Dale discusses his background and his responsibilities at Lenthor since joining the company in May. Dale explains his plans to continue implementing the company’s Lean program, as well as pushing the technology limits for their flex customers. David addresses Lenthor’s operations during the COVID-19, when the company stayed up and running with safety measures in place, and what the landscape might look like after the smoke clears.
I-Connect007 continues to deliver original reporting and coverage of the electronics design, electronics manufacturing, and contract manufacturing industries, including up-to-date information from the companies, associations, and supply chains globally. Find the latest news and information at I-Connect007.com.
Related Link:
- To download this audio (mp3) file, click here.
Transcribed text:
Andy Shaughnessy: Hi. I’m Andy Shaughnessy for I-Connect007. Joining me this afternoon are Dale Smith and Dave Moody from Lenthor. How are you guys doing?
Dale Smith: Good. How about yourself?
Shaughnessy: Pretty good. Dale, why don’t you start off by telling us about yourself and your responsibilities at Lenthor?
Smith: I’ve been brought on with Lenthor about the middle of May. I’m the chief technology officer, and I was brought on to basically continue with the lean process and take that to another level, as well as to develop new technology—some of the technology as you see merging with some of our customers, bringing that onboard and adding that capability, and because I’m located on the East Coast, working with some customers that are located in this territory to help again expand Lenthor’s sales capabilities. I’ve been in the business for 35+ years, so I’ve been in for a long time, and it’s mainly all been flex.
Shaughnessy: Why don’t you give us a quick update on Lenthor? I understand you stayed up and running during the pandemic.
David Moody: Yes. Like most companies during the initial outbreak, there were some questions about whether or not we were going to be able to remain operating and what the regulations were going to be. Who was going to be authorized? Were employees going to be allowed to go into a building? But we worked through all of those issues. We did a lot of extensive training with our employees on specific protocols as they got issued by various health districts, and ours is in Santa Clara County, California.
We have been fortunate at this point that everybody has been extremely cooperative, not just the employees, but our suppliers who have had to come to this facility to bring materials and service equipment. We have very strict protocols—temperature taking, mask wearing, social distancing, and all of the things that everybody by now they’re probably way too familiar with. We are fortunate again to say that no one in the company has had contact or has come down with COVID-19. We are just knocking on wood every day that that maintains, and we’ve been able to be up and running and service our customers almost without any hesitation.
Shaughnessy: That’s good. What trends are you seeing in the industry right now?
Smith: I would say one of the biggest ones is filling vias. That seems to be becoming a need in the flex area. In rigid-flex, it’s been there, and it’s quite common in the rigid materials, but now also we’re starting to see trends where they want to have it in the flex materials. It’s a lot more challenging with the flex materials because of thinness and surface topography. Obviously, with rigid materials, it’s been around for quite a long time, and you’re dealing with flat surfaces and things like that—I would say, filling vias with conductive and non-conductive type paste. Obviously, the quick turnaround marketplace is still, due to COVID-19, people asking for products in a reasonably short period of time. That’s why one of the things at Lenthor with the lean initiative is to reduce cycle time. That’s why that’s high on our agenda to see how we can shrink our delivery cycle and shorten that basically as quickly as we can.
Shaughnessy: What are Lenthor’s plans going forward?
Smith: Again, lean is a big item on our list, and we already have a new facility. It was completed in 2014. Mark Lencioni, the owner of the company, actually laid it out in a lean flow. The product flows in a nice pathway through the facility. That helps a great deal with moving any waste and queue times. We want to really expand that area into more of some of the lean initiatives. That’s huge on our list—obviously, new technology with filling vias and also lasering with some of the new laser capabilities, or adding some smaller diameters and cutting and all that type of stuff. Then, the other item that we’re really high on is doing more of the rigid-flex high layer count type of products. Again, that’s a big need in the industry, being able to produce 20, 30 layer technology.
Shaughnessy: Is there anything else either of you would like to add?
Moody: Those areas are a high priority for Lenthor, and we’re actually hiring. Lenthor is quite busy. We do have some positions open in upfront engineering, account management, and those types of things. That’s a good thing for this industry. Also, with some of the customer base—some of the OEMs—we’re seeing they need a new supplier again due to shortages in the industry. We’re also looking at new materials, high-speed materials, and the need for data transmission at higher rates. There are some new materials available that have just come out that we’re definitely going to take a good look at it and see how they fit into our customer demands.
Shaughnessy: Sounds good. Thanks for doing this.
Smith: Thanks for having us, Andy.
Shaughnessy: Sure. Again, I’m Andy Shaughnessy for I-Connect007. I’ve been speaking with Dave Moody and Dale Smith of Lenthor. Thanks for listening.
Testimonial
"The I-Connect007 team is outstanding—kind, responsive, and a true marketing partner. Their design team created fresh, eye-catching ads, and their editorial support polished our content to let our brand shine. Thank you all! "
Sweeney Ng - CEE PCBSuggested Items
PEDC Call for Abstracts Deadline Extended to Aug. 31
08/20/2025 | I-Connect007 Editorial TeamThe second Pan-European Electronics Design Conference (PEDC) will take place Jan. 21-22, 2026, in Prague, Czech Republic. The call for abstracts deadline has been extended to Aug. 31. Organized jointly by the German Electronics Design and Manufacturing Association (FED) and the Global Electronics Association (formerly IPC), PEDC serves as a European platform for knowledge exchange, networking, and innovation in electronics design and development.
Nano Silver Inks Market Forecast Report 2025-2030
08/20/2025 | Globe NewswireThe Nano Silver Inks Market is expected to grow from USD 427.415 million in 2025 to USD 836.160 million in 2030, at a CAGR of 14.36%.
VVDN Expands Manufacturing Footprint into the UAE to Meet Global Demand
08/20/2025 | PRNewswireVVDN Technologies, a global provider of software, product engineering and electronics manufacturing services & solutions, today announced it is setting up a new manufacturing facility in the UAE as part of its global expansion strategy.
Kimball Electronics Veterans ERG Members Proudly Participate in the 5th Annual Honor and Remember Run
08/20/2025 | Kimball ElectronicsVeterans and Military Service Advocacy (VMSA) Employee Resource Group (ERG) members Michael Mosher (Database Administration Engineer), Michael Stone (Test Technician Team Lead), and Joshua Belcher (Application Development Manager) took part in the 5th Annual Honor & Remember Run, a meaningful event dedicated to honoring fallen service members. The race featured a powerful memorial wall constructed from dog tags.
Meet Incap UK at the Electronic Component Show 2025
08/20/2025 | IncapIncap UK is pleased to be exhibiting at the Electronic Component Show 2025. This one-day event will take place on 18 September at the Kassam Stadium in Oxford, bringing together design engineers, purchasing professionals, manufacturers, distributors, and service providers to discover new products, solutions, and contacts. You will find us at stand 52.