-
- News
- Books
Featured Books
- pcb007 Magazine
Latest Issues
Current IssueInventing the Future with SEL
Two years after launching its state-of-the-art PCB facility, SEL shares lessons in vision, execution, and innovation, plus insights from industry icons and technology leaders shaping the future of PCB fabrication.
Sales: From Pitch to PO
From the first cold call to finally receiving that first purchase order, the July PCB007 Magazine breaks down some critical parts of the sales stack. To up your sales game, read on!
The Hole Truth: Via Integrity in an HDI World
From the drilled hole to registration across multiple sequential lamination cycles, to the quality of your copper plating, via reliability in an HDI world is becoming an ever-greater challenge. This month we look at “The Hole Truth,” from creating the “perfect” via to how you can assure via quality and reliability, the first time, every time.
- Articles
- Columns
- Links
- Media kit
||| MENU - pcb007 Magazine
Estimated reading time: 4 minutes
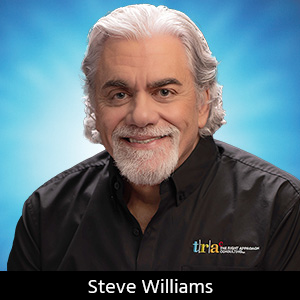
The Right Approach: The Founding Fathers of Quality—Ishikawa and Shewhart
This column continues the series of installments, each highlighting one of the seven founding fathers of quality (as selected by the author). It is important to understand and acknowledge their revolutionary contributions that still form the foundation of modern quality practices.
Dr. Kaoru Ishikawa (1915–1989)
Dr. Ishikawa was revolutionary in that he wanted to change the way people think about work. His vision was one of company-wide, total quality management, and argued that an over-reliance on the quality professional would limit the potential for improvement. Ishikawa believed that by empowering all personnel with quality, responsibility would result in a synergy not possible with the typical silo approach to quality. He urged management to resist becoming content with simply improving product quality, teaching that quality improvement can always go one step further by using statistics to drive process improvement.
Dr. Ishikawa is perhaps best known for his cause and effect diagram, also known as a fishbone or Ishikawa diagram. Ishikawa’s vision with this tool was not to merely address the symptoms, but to drive issues to root cause by pinpointing problems from the bottom up. Ishikawa also started the quality circles movement, which is still used today by many companies in the form of quality improvement teams. Dr. Ishikawa was the first quality pioneer to emphasize what he termed the “seven basic quality tools” as a foundation for any quality system (Figure 1). My favorite Ishikawa quote is, “Quality control which cannot show results is not quality control. Let us engage in QC which makes so much money for the company that we do not know what to do with it.”
Core Attributes of the Ishikawa Philosophy
Here are Ishikawa’s seven basic quality tools.
- Cause and effect diagram: Identifies root cause by brainstorming many possible causes for a problem, and then sorts the causes into categories.
- Pareto chart: Bar graph representation of a histogram sorted by descending frequency used to prioritize data based on the Pareto principle (80/20 rule), where 80% of a problem comes from 20% of the causes.
- Flowchart: A visual representation (picture) of a process.
- Check sheet: A customized form for collecting and analyzing data.
- Scatter diagram: Graphs pairs of numerical data, one variable on each axis, to look for trends, patterns, or relationships in the data.
- Control charts: Graphs used to study how a process changes over time.
- Histogram: A graph for showing frequency distributions and how often each different value in a set of data occurs and determining whether a process has a normal or bell-shaped distribution.
Walter A. Shewhart (1891–1967)
Dr. Walter A. Shewhart was one of W. Edwards Deming’s early mentors, promoting the ?utilization of his own groundbreaking creation: the SPC control chart. Shewhart believed that management did not have sufficient access to the real-time data needed to effectively manage and control processes in a manufacturing environment. To this end, Shewhart developed a set of statistical process control methods that focus on reducing process variation to improve quality.
He was also the creator of the Shewhart cycle, better known as the plan–do–check–act (PDCA) cycle, which seeks continuous improvement by combining constant evaluation of management policy and procedures with statistical analysis. It is not hard to appreciate Shewhart’s passion for statistics when considering his most recognizable quote: “The long-range contribution of statistics depends not so much upon getting a lot of highly trained statisticians into industry as it does in creating a statistically minded generation of physicists, chemists, engineers, and others who will in any way have a hand in developing and directing the production processes of tomorrow.”
Core Attributes of the Shewhart Philosophy
The Shewhart cycle (Figure 2) is a basic model for continuous improvement that can be used in a variety of situations, such as beginning improvement projects; developing a new or improved process, product, or service; defining a repetitive work process; performing root-cause analysis; or implementing any change. The Shewhart cycle was later improved on by Dr. Deming.
PDCA Cycle
Plan the activity that is going to take place. In this step, a gap analysis is done, looking at the current state and desired future state and planning for how to close the gap. Identification of potential solutions occurs during the “plan” stage.
Do test the various potential solutions.
Check results to see if any of the potential solutions tested had the desired effect and assess the effectiveness of successful solutions.
Act on what you have learned, implementing the best of the potential solutions. If you have accomplished your objective, put controls into place so that the issue never comes back again. If you have not accomplished your objective, go through the cycle again, starting with the plan step.
Conclusion
It is interesting how long it took the American industry to adopt Dr. Ishikawa’s philosophy of empowering all personnel with quality responsibility. Not until the latest 2015 revision of ISO 9001 did the international standard require that all employees, starting with top management, be responsible for the QMS. His seven basic quality tools are still prevalent in most quality management systems to this day. Shewhart’s PDCA improvement tool is now a requirement in ISO 9001:2015, which validates the relevance of Shewhart’s work from over 70 years ago. It is hard to find an organization today that is not running their processes using some form of SPC or statistical methods. These facts demonstrate just how far ahead of its time these founding fathers were.
This column originally appeared in the February issue of PCB007 Magazine.
More Columns from The Right Approach
The Right Approach: ‘Twas the Night Before Christmas (Harley-style)The Right Approach: I Hear the Train A Comin'
The Right Approach: Culture Change is Key to a QMS
The Right Approach: Leadership 101—Be a Heretic, Not a Sheep
The Right Approach: Leadership 101—The Law of Legacy
The Right Approach: Leadership 101: The Law of Explosive Growth
The Right Approach: Leadership 101—The Law of Timing
The Right Approach: The Law of Sacrifice