Solder Joint Reliability With IMS Materials
October 13, 2020 | Pete Starkey, I-Connect007Estimated reading time: 3 minutes
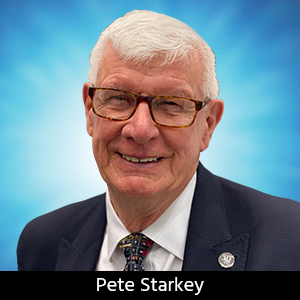
I had the opportunity to attend a technical webinar on thermal management hosted by American Standard Circuits and featuring Ventec International Group’s range of insulated metal substrate materials. The webinar was moderated by Anaya Vardya, president and CEO of American Standard Circuits, and the speakers were Ventec’s Global Head of IMS Technology Chris Hanson and Technical Manager Denis McCarthy. The group identified factors that influence thermo-mechanical robustness and provided a logical solution.
Following a review of markets and applications for Ventec’s portfolio, emphasising how the company recognises and responds to industry needs, the discussion focused on its roadmap for thermal management materials and their next generation of specialist developments.
Chris Hanson described a case history, illustrating how a particular reliability issue emerging in critical automotive applications had been identified and overcome by systematic research and development. He utilised Ventec’s expertise in metallurgical and dielectric technologies to provide an integrated solution.
The problem was one of solder joint fatigue in LED headlight assemblies, resulting from shear stresses generated by differential expansion-contraction during thermal cycling in operation. Although an obvious primary consideration in maintaining LED performance in terms of light output and service life is efficient heat dissipation, the benefit is limited if the assembly fails prematurely because of cracks in solder joints. Failure of this type had been observed by a major automotive OEM, who cooperated with Ventec in establishing the cause and evaluating a solution.
Ventec formulated a low-modulus variant of their 4W/mK, non-glass VT-4B5 dielectric, designated VT-4B5L, and used it in combination with a low-expansion aluminium alloy designated CTE II (19.0 ppm/°C compared to 23.8 ppm/°C for regular 5052 aluminium).
A representative IMS test circuit design with a pattern of soldered LEDs was used for evaluation. Ventec supplied a series of laminate panels based on the CTE II low-expansion aluminium alloy, with standard and low-modulus dielectrics in 100-micron and 50-micron thicknesses. A control material was included, based on regular 5052 aluminium with 100-micron standard-modulus dielectric.
The OEM fabricated and assembled the test circuits under identical conditions, and a standard automotive-industry thermal shock testing procedure was used for comparison of their thermo-mechanical robustness. The test cycle was to hold at -40°C for 21 minutes, transfer in less than 30 seconds to +105°C for 35 minutes, and then transfer in less than 30 seconds back to -40°C, repeated for 1016 cycles in three stages with electrical testing at each stage.
Samples from equivalent areas of each construction were microsectioned after 469 cycles and 1016 cycles, and Hanson showed many examples of actual cross-sections, displaying some instances of crack initiation and propagation through the solder joint. Severe cracking—and in certain cases, complete rupture of the solder joint—could be clearly seen in examples of the reference construction on 5052 aluminium with standard-modulus dielectric after 1016 cycles.
The best performance came from the material composed of CTE II aluminium alloy and 100-micron VT-4B5L low-modulus dielectric. This was slightly better than a similar construction with 50-micron VT-4B5L, which was significantly better than a similar construction with 50-micron VT-4B5 standard-modulus dielectric, which was better than the reference material. Interestingly, a second reference material, based on copper rather than aluminium, showed no benefit in solder joint reliability.
The conclusion was consistent with expectations. The combination of the low-expansion aluminium base-plate material and the low-modulus dielectric gave the most significant improvement in solder joint reliability, and it was proposed that this combination be used in all future designs that might experience solder joint stress.
The webinar provided plenty of valuable technical information for which I am grateful to Chris Hanson and Denis McCarthy. And many thanks to Anaya Vardya for hosting and moderating the event.
Further Reading
- Anaya Vardya, American Standard Circuits, The Printed Circuit Designer's Guide to... Thermal Management: A Fabricator's Perspective.
- Didier Mauve and Ian Mayoh, Ventec International Group, The Printed Circuit Designer's Guide to... Thermal Management with Insulated Metal Substrates.
Suggested Items
Hands-On Demos Now Available for Apollo Seiko’s EF and AF Selective Soldering Lines
06/30/2025 | Apollo SeikoApollo Seiko, a leading innovator in soldering technology, is excited to spotlight its expanded lineup of EF and AF Series Selective Soldering Systems, now available for live demonstrations in its newly dedicated demo room.
Indium Corporation Expert to Present on Automotive and Industrial Solder Bonding Solutions at Global Electronics Association Workshop
06/26/2025 | IndiumIndium Corporation Principal Engineer, Advanced Materials, Andy Mackie, Ph.D., MSc, will deliver a technical presentation on innovative solder bonding solutions for automotive and industrial applications at the Global Electronics A
Fresh PCB Concepts: Assembly Challenges with Micro Components and Standard Solder Mask Practices
06/26/2025 | Team NCAB -- Column: Fresh PCB ConceptsMicro components have redefined what is possible in PCB design. With package sizes like 01005 and 0201 becoming more common in high-density layouts, designers are now expected to pack more performance into smaller spaces than ever before. While these advancements support miniaturization and functionality, they introduce new assembly challenges, particularly with traditional solder mask and legend application processes.
Knocking Down the Bone Pile: Tin Whisker Mitigation in Aerospace Applications, Part 3
06/25/2025 | Nash Bell -- Column: Knocking Down the Bone PileTin whiskers are slender, hair-like metallic growths that can develop on the surface of tin-plated electronic components. Typically measuring a few micrometers in diameter and growing several millimeters in length, they form through an electrochemical process influenced by environmental factors such as temperature variations, mechanical or compressive stress, and the aging of solder alloys.
SolderKing’s Successful Approach to Modern Soldering Needs
06/18/2025 | Nolan Johnson, I-Connect007Chris Ward, co-founder of the family-owned SolderKing, discusses his company's rapid growth and recent recognition with the King’s Award for Enterprise. Chris shares how SolderKing has achieved these award-winning levels of service in such a short timeframe. Their secret? Being flexible in a changing market, technical prowess, and strong customer support.